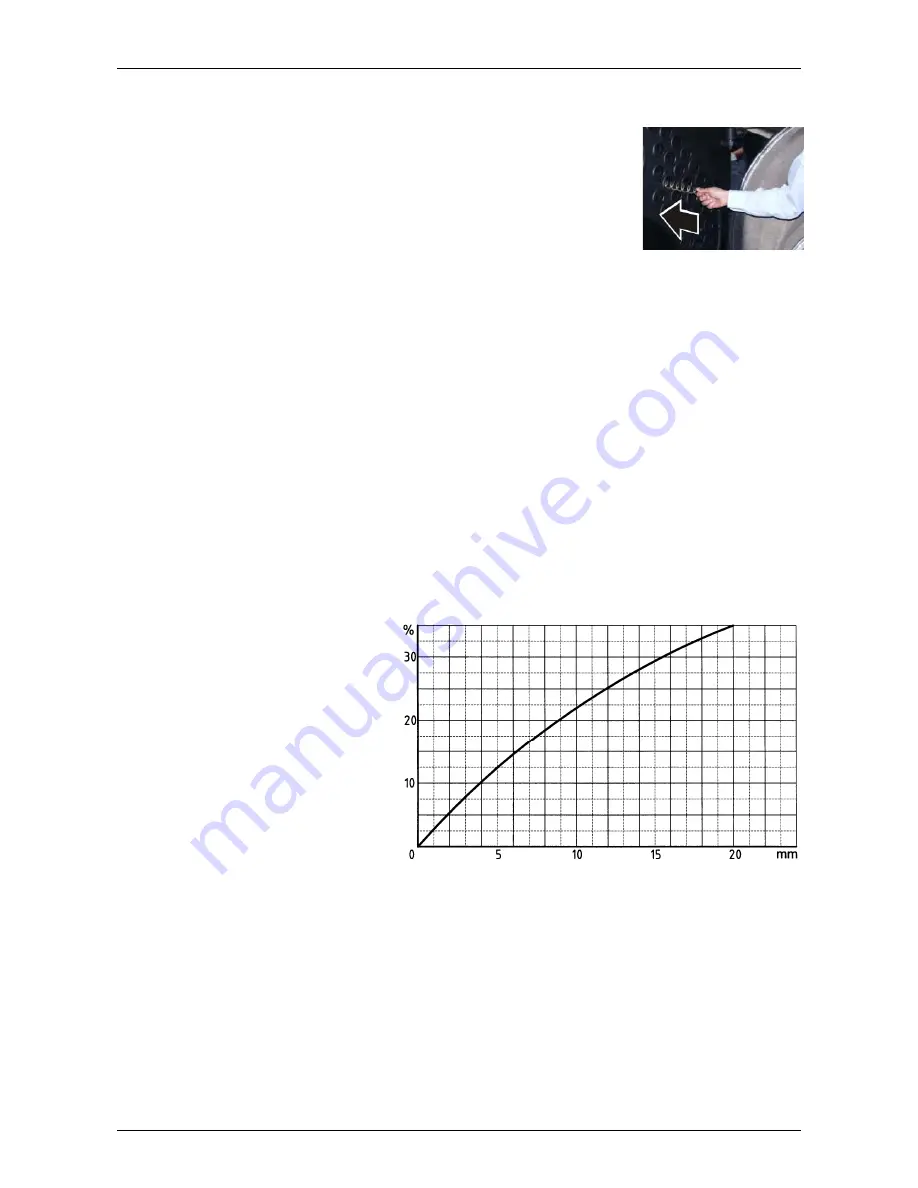
27
5 START UP
WARNING: Before start up, open the door and insert w holly turbolators into
the front end sections of the smoke tubes, ensuring that they hav e been
pushed inside for at least 100 mm.
5.1 PRELIMINARY CHECKS
Before starting the boiler, check that:
- The
rating plate
specifications and power supply network (electricity, water,
gas or fuel oil) specifications correspond;
- The burner
power range
is compatible with the power of the boiler;
- The boiler room also contains the instructions for the burner;
- The
flue gas exhaust pipe
is operating correctly;
- The
air inlet supply
is well dimensioned and free from any obstacle;
- The
manhole
, the
smokebox
and the
burner plate
are closed in order to provide a complete flue gas
seal;
- The system is
full of water
and that any
air pockets
have therefore been eliminated;
- The
anti-freeze
protections are operative;
- The water
circulation pumps
are operating correctly.
- The expansion vessel and the safety valve(s) hav e been connected correctly (with no interception) and
are properly operating.
- Check the electrical parts and thermostat operation.
5.2 WATER TREATMENT
The most common phenomena that occur in heating systems are:
- Scaling
Scale obstructs heat transfer between the combus tion gases and the water, causing an abnormal in-
crease in the temperature of the metal and therefore reducing the life of the boiler.
Scale is found mostly at the point s where the wall temperature is highest and the best remedy, at con-
struction level, is to eliminate areas that overheat.
Scale creates an insulating layer which reduces the thermal transfer of the generator, affecting system ef-
ficiency. This means that the heat produced by burning the fuel is not fully exploited and is lost to the flue.
Scale diagram
Key
%
% fuel not used
mm
mm scale
- Corrosion on the water side
Corrosion of the metal surfaces of the
boiler on the water side is due to the
passage of dissolved iron through its
ions (Fe+). In this process the presence
of dissolved gases and in particular of oxygen and car bon dioxide is very important. Corrosion often oc-
curs with softened or demineralised water which has a more aggressive effect on iron (acid water with Ph
<7): in these cases, although the sy stem is protected from scaling, it is not protected against corrosion
and the water must be treated with corrosion inhibitors.
5.3 FILLING THE SYSTEM
The water must enter the system as slowly as possible and in a quantity proportional to the air bleeding
capacity of the components involved. Filling times vary depending on the capacity and characteristics of
the system but should never be less than 2 or 3 hours.
In the case of a system with closed expansion vessel, water must be let in until the pressure gauge indicator
reaches the static pressure value pre-set by the vessel.
Heat the water to maximum temperature. During this operation the air contained in the water is released
through the automatic air separators or through manual bleed valves. The water discharged from the system
with elimination of the air is made up by the automatic or manual filling valve.
Summary of Contents for REX F
Page 1: ...TECHNICAL MANUAL REX REX F REX K REX K F REX DUAL REX DUAL F PRESSURISED STEEL BOILERS...
Page 2: ......
Page 18: ...18 1 2 6 3 4 5 9...
Page 30: ......
Page 32: ...ASSEMBLY INSTRUCTIONS STAVES LINING...
Page 33: ......