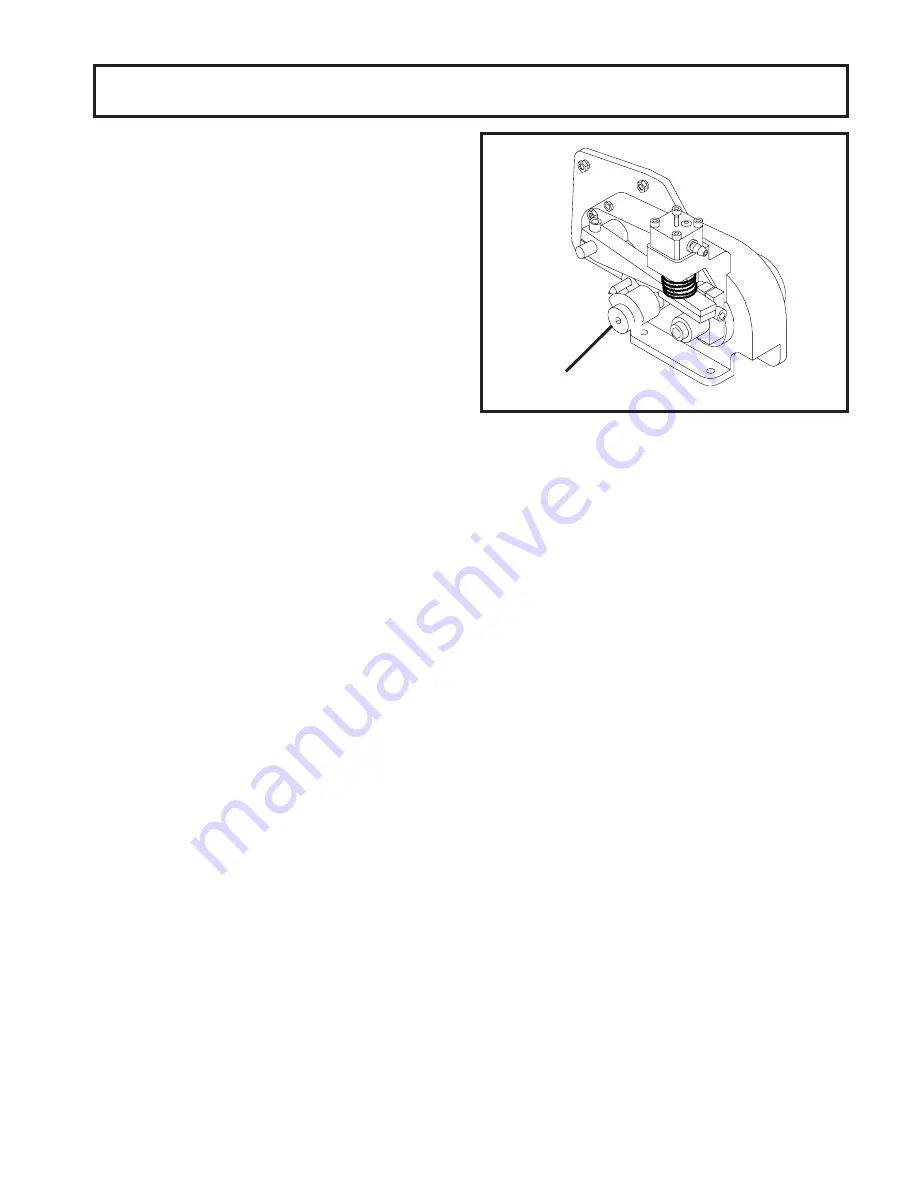
11
4.1 OVER-RUN ADJUSTMENT
The product when served is a combination of air and mix.
Over-run is a measure of the amount of air blended into the
mix.
Over-run can be expressed in terms of the amount of
weight loss for a given volume. For example, if a pint of
liquid mix weighs 18 ounces and a pint of frozen product
with air added weighs 12 ounces, the over-run is said to be
50 percent (18 oz. - 12 oz. = 6 oz., (6 /12) x 100 = 50%.
The over-run can be checked by placing a one pint
container on an ice cream scale and zeroing out the scale.
Then fill a one pint container with frozen product. The
container should be filled over the top and leveled with a
straightedge. The product should not contain any air
pockets. When weighed on an ice cream scale, one pint
of product should weigh 12 to 13 ounces.
The mix pump has been preset at the factory to produce a
product with approximately 40% overrun. Because of
differences in mix formulation, temperatures and baromet-
ric pressure, this figure may vary. It will be necessary for
approximately 2 gallons of mix to be pumped thru the
freezer before changes in the product are noticeable due
to adjustments in overrun.
Overrun is controlled by the length of the air compressor
piston stroke within the piston cylinder. Lengthening the
stroke within the cylinder will increase overrun. Con-
versely, shortening the stroke will decrease overrun. To
perform an overrun adjustment, refer to the following
procedure:
A. Turn the mix pump switch to the OFF position and
unplug the mix pump from its grounded 115V recep-
tacle.
B. Remove the 2 electrical box cover screws and remove
the electrical box cover.
C. On air compressor side of pump, locate the long/
slender piston rocking arm. The rocking arm down-
ward travel is limited by a stationery cam. On the
face of the cam there is an overrun setting indicator
plate numbered 3 thru 8 and an adjustment knob
(Fig. 7).
D. The overrun setting is indicated by a pointed pin.
E. To adjust overrun, loosen the allenhead screw
(located within the center of the adjustment knob)
with the 5/32" allen wrench provided. Rotate the
adjustment knob counterclockwise to a higher
number for higher overrun, or clockwise to a lower
number for lower overrun. Each number multiplied by
10 represents the overrun percentage (ie: #4 = 40%
overrun).
SECTION 4
MAINTENANCE INSTRUCTIONS
Figure 7
Overrun Adjustment
F. Tighten the allen screw, then place the wrench back
in its clip. Replace the electrical box cover and
screws, plug the mix pump into its grounded 115V
receptacle and turn the mix pump power switch to the
ON position.
4.2 PREVENTATIVE MAINTENANCE
To assure trouble free operation and consistent over-run
when using the U3 mix pump, we must follow mix hose
repositioning and replacement procedures. The following
is the preventative maintenance schedule:
A. MIX PUMP HOSE REPOSITION (every one or two
weeks.)
NOTE
Mix pump hose must be repositioned every 1 - 2
weeks. Failure to comply will result in reduced mix
pump liquid capacity, dispense stoppage, popping,
and possible mix pump hose leakage.
1. Run cleaning solution through pump.
2. Turn pump off and if connected to freezer, relieve any
pressure by opening the spigot.
3. Grasp the pick-up hose end of the mix pump hose
with one hand and turn the pump on. Pull down on the
pick-up hose end until 12 to 14 inches of tubing has
reversed fed through the pump, then turn the pump
off.
4. Loosen small clamp at the pick-up hose adapter and
disconnect mix pump hose.
5. Cut 7-1/2 inches off the end of the mix pump hose.
The height of the pump can be used to measure. See
Figure 8.
OVERRUN
ADJUSTMENT