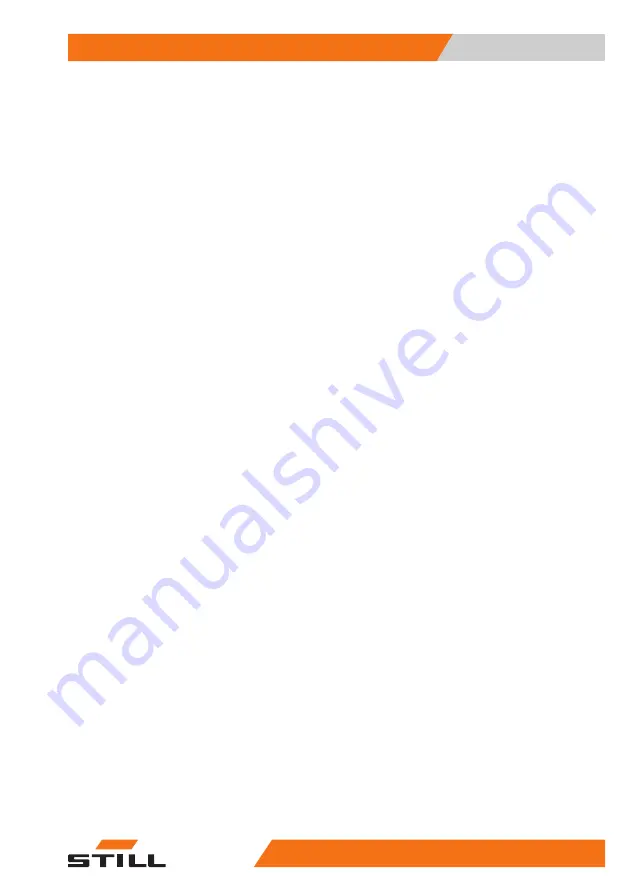
N
UMBERS
AND
S
YMBOLS
4T MAST SPECIFICATIONS. . . . . . . . . . 155
5T MAST SPECIFICATIONS. . . . . . . . . . 156
A
Address of manufacturer and contact details. I
Adjusting the position of steering wheel. . 70
Adjustment of the driver’s seat. . . . . . . . . 67
After washing. . . . . . . . . . . . . . . . . . . . . . 109
B
Battery
Disposal. . . . . . . . . . . . . . . . . . . . . . . . 25
Battery acid. . . . . . . . . . . . . . . . . . . . . . . . 24
Before lifting a load. . . . . . . . . . . . . . . . . . 88
Belt Tension. . . . . . . . . . . . . . . . . . . . . . . 139
C
Capacity plate. . . . . . . . . . . . . . . . . . . . . . 87
CE labelling. . . . . . . . . . . . . . . . . . . . . . . . . 6
Change brake system liquid. . . . . . . . . . 145
Change the air filter. . . . . . . . . . . . . . . . . 138
Change the LP Gas tank. . . . . . . . . . . . . . 59
Changing direction of travel. . . . . . . . . . . . 78
Changing the engine oil. . . . . . . . . . . . . . 130
Changing the hydraulic transmission crude
oil filter. . . . . . . . . . . . . . . . . . . . . . . . . . 140
Changing the oil of the hydraulic transmis-
sion. . . . . . . . . . . . . . . . . . . . . . . . . . . . 142
Changing the suction filter and return fil-
ter. . . . . . . . . . . . . . . . . . . . . . . . . . . . . 146
Checking the cap on the high-pressure re-
lief valve on the outside of the LPG sys-
tem. . . . . . . . . . . . . . . . . . . . . . . . . . . . . 48
Checking the coolant level. . . . . . . . . . . . . 54
Checking the drive axle gearbox oil. . 58, 143
Checking the hydraulic oil level. . . . . 58, 146
Check the belt tension. . . . . . . . . . . . . . . 139
Check the condition and operation of chain. 53
Check the engine oil level. . . . . . . . . . . . . 56
Check the wheel nuts for correct condition. 52
Cleaning the electrical system. . . . . . . . . 107
Cleaning the radiator, checking for leaks. 137
Cleaning the truck. . . . . . . . . . . . . . . . . . 105
Clean the air filter. . . . . . . . . . . . . . . . . . . 137
Climbing on/off the forklift. . . . . . . . . . . . . 67
Closing the bonnet. . . . . . . . . . . . . . . . . . 127
Competent person. . . . . . . . . . . . . . . . . . . 10
Consumables
Disposal. . . . . . . . . . . . . . . . . . . . . . . . 24
Safety information for handling battery
acid. . . . . . . . . . . . . . . . . . . . . . . . . . 24
Safety information for handling oils. . . 22
Safety information for hydraulic fluid. . 23
D
Daily checks before use. . . . . . . . . . . . . . . 48
Danger area. . . . . . . . . . . . . . . . . . . . . . . . 88
Definition of terms used for responsible
persons. . . . . . . . . . . . . . . . . . . . . . . . . . 10
Description of use and climatic conditions. . 5
Dimensions. . . . . . . . . . . . . . . . . . . . . . . 150
Direction selection lever. . . . . . . . . . . . . . . 74
Display unit. . . . . . . . . . . . . . . . . . . . . . . . 35
Disposal
Battery. . . . . . . . . . . . . . . . . . . . . . . . . 25
Components. . . . . . . . . . . . . . . . . . . . . 25
Driver rights, duties and rules of behaviour. 11
Drivers. . . . . . . . . . . . . . . . . . . . . . . . . . . . 10
Driving. . . . . . . . . . . . . . . . . . . . . . . . . . . . 75
Ascending gradients. . . . . . . . . . . . . . . 97
Descending gradients. . . . . . . . . . . . . . 97
Driving brake pedal and inching pedal. . . . 79
Driving on lifts. . . . . . . . . . . . . . . . . . . . . . 98
Driving on loading bridges. . . . . . . . . . . . . 99
E
EC declaration of conformity in accordance
with Machinery Directive. . . . . . . . . . . . . . 8
Electric schematic diagram for Doosan
P34 engine—with ISO3691 function. . . 166
EMC – Electromagnetic compatibility. . . . . 7
Emissions. . . . . . . . . . . . . . . . . . . . . . . . . 27
Engine coolant - Specifications. . . . . . . . . 64
Engine plate. . . . . . . . . . . . . . . . . . . . . . . . 38
F
Fastening the seat belt. . . . . . . . . . . . . . . 68
Fill up the hydraulic oil. . . . . . . . . . . . . . . 145
Fire extinguisher. . . . . . . . . . . . . . . . . . . . 13
Forklift towing. . . . . . . . . . . . . . . . . . . . . . 103
Forward. . . . . . . . . . . . . . . . . . . . . . . . . . . 77
Fuel. . . . . . . . . . . . . . . . . . . . . . . . . . . . . . 64
Index
157
60118011601 EN - 09/2020
Summary of Contents for RCG40
Page 1: ...LPG forklift truck RCG40 RCG50 Original instructions 4234 4236 60118011601 EN 09 2020 ...
Page 2: ......
Page 4: ......
Page 10: ......
Page 11: ...1 Introduction ...
Page 19: ...2 Safety ...
Page 41: ...3 Information about the truck ...
Page 52: ...Information about the truck 3 Location of the decals 42 60118011601 EN 09 2020 ...
Page 53: ...4 Use and Operation ...
Page 123: ...5 Maintenance ...
Page 159: ...6 Technical datasheet ...
Page 160: ...Dimensions Technical datasheet 6 Dimensions 150 60118011601 EN 09 2020 ...
Page 170: ......
Page 171: ......
Page 172: ...STILL GmbH 60118011601 EN 09 2020 ...
Page 173: ...LPG forklift truck RCG40 RCG50 Original instructions 4234 4236 60118011601 EN 09 2020 ...
Page 174: ......
Page 175: ...7 Diagrams ...
Page 177: ...Hydraulic diagram Diagrams 7 Hydraulic diagram 167 60118011601 EN 09 2020 ...
Page 178: ...Diagrams 7 Hydraulic diagram 168 60118011601 EN 09 2020 ...
Page 179: ......
Page 180: ...STILL GmbH 60118011601 EN 09 2020 ...