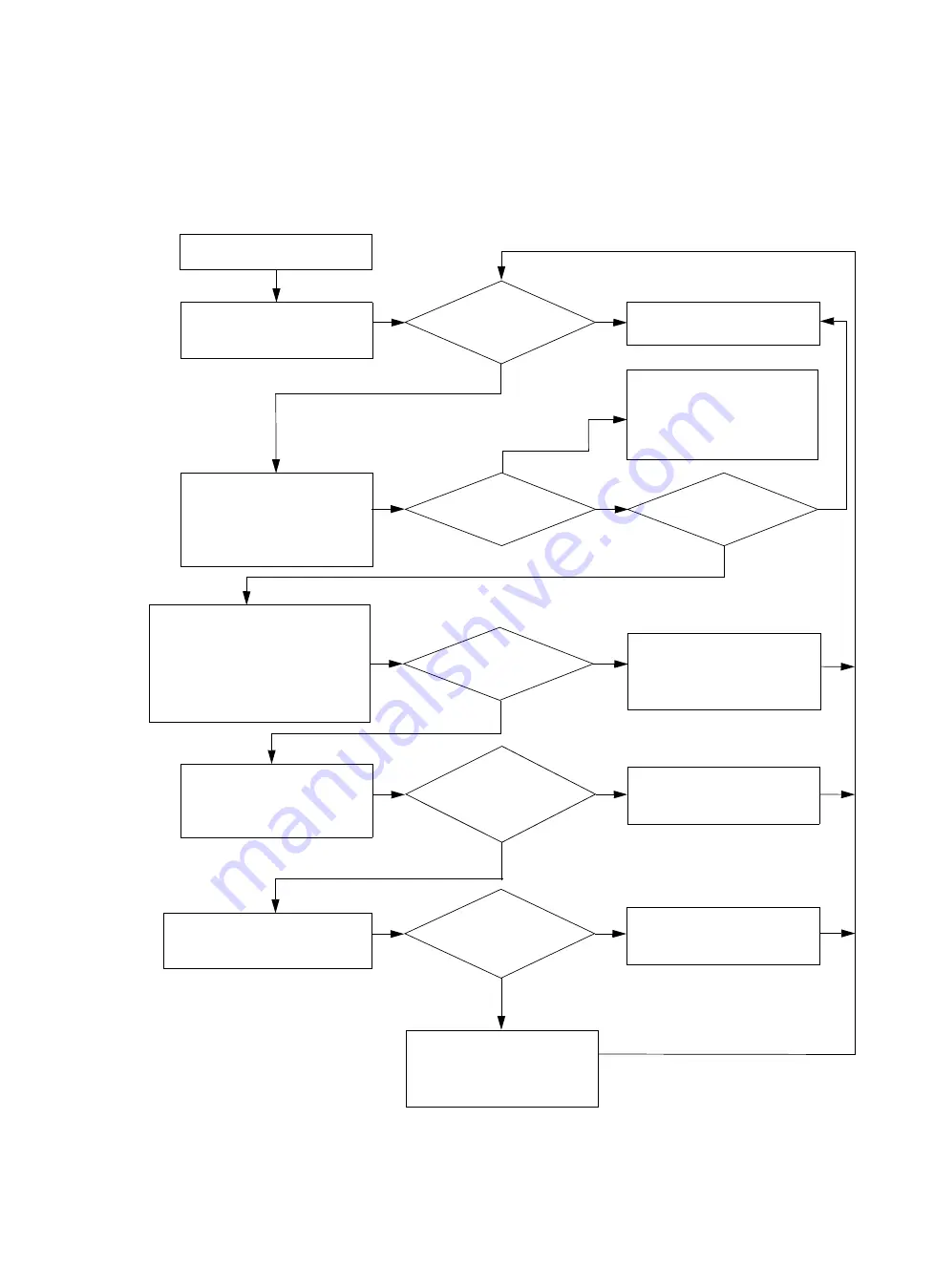
65
FS 240 C, FS 260 C, FS 360 C, FS 410 C, FS 460 C-M
7.5
Troubleshooting, M-Tronic
7.5.1
Engine does not start
Can engine
be started?
no
– Move choke lever to
position
}
Troubleshooting completed
– Check ignition (spark
plug, spark plug boot,
ignition spark),
Ignition spark
present?
– Mechanically check start
detection system; is the
switchgear (microswitch)
actuated by the cam of the
choke lever?
– Clicking noise,
– Examine switch gear,
clean or replace if
necessary,
– Check start detection and
wiring harness electrically,
yes
Mechanically
OK?
Are target values
attained?,
– Look for a fault in the fuel
path, check engine for
leaks,
– Replace switchgear,
no
yes
no
no
Engine does not start
Is it possible to start
the engine?
yes
no
– Check solenoid valve,
Are target values
attained?
– Replace switchgear and/
or carburetor,
yes
yes
no
– Test ignition system
according to flow chart
"Ignition system
troubleshooting",
yes