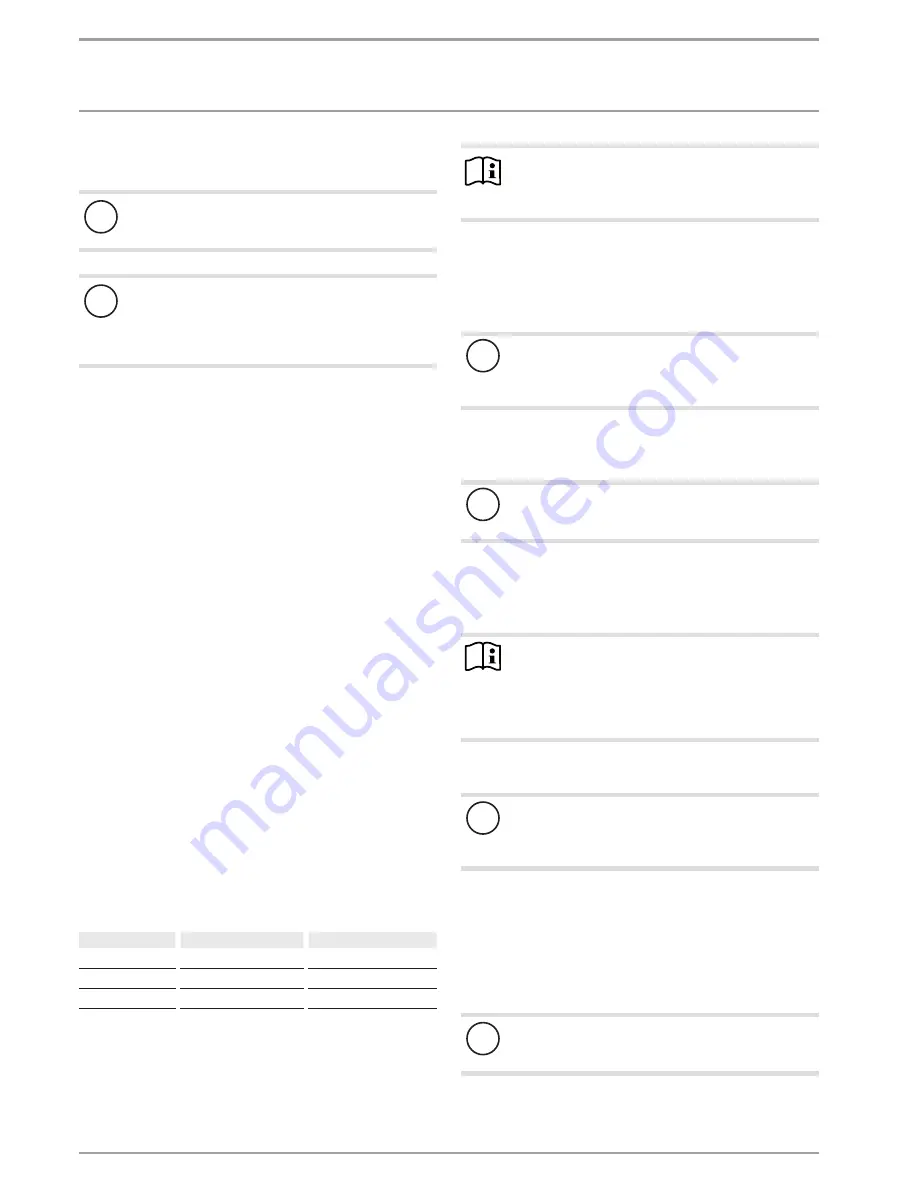
14
| WPF M
WWW.STIEBEL-ELTRON.COM
INSTALLATION
ShuTTING DOWN
11.1 Checks prior to commissioning the heat pump
manager
!
Damage to the appliance and environment
Observe the maximum system temperature in underfloor
heating systems.
!
Damage to the appliance and environment
With an underfloor heating system, never use the heat
pump to dry the screed as this places such a high demand
on the heat source that the frost protection function may
respond.
f
f
Check whether the heating system is charged to the correct
pressure and the quick-action air vent valve is open.
f
f
Check whether the outside temperature sensor is correctly
placed and connected.
f
f
Check whether the power supply is connected correctly.
f
f
Check whether the connecting cable to the heat pump (BUS
cable) is connected correctly.
11.2 Commissioning the heat pump manager
Commission the heat pump manager and make all settings in ac-
cordance with the operating and installation instructions for the
heat pump manager.
11.3 Heating curve adjustment
The efficiency of a heat pump decreases as the flow temperature
rises. The heating curve should therefore be adjusted with care.
Heating curves that are set too high cause the zone valves and
thermostatic valves to close, which may lead to the minimum flow
rate required for the heating circuit not being achieved.
f
f
Observe the WPM operating and installation instructions.
The following steps will help you to adjust the heating curve cor-
rectly:
- Fully open thermostatic or zone valves in a lead room (e.g.
living room and bathroom).
We do not recommend installing thermostatic or zone valves
in the lead room. Control the temperature for these rooms
via remote control.
- At different outside temperatures (e.g. –10 °C and +10 °C),
adjust the heating curve so the required temperature is set in
the lead room.
Standard values to begin with:
Parameter
Underfloor heating system Radiator heating system
Heating curve
0.4
0.8
Control response time 5
15
Comfort temperature 20 °C
20 °C
If the room temperature in spring and autumn is too low (approx.
10 °C outside temperature), the value of parameter COMFORT TEM-
PERATURE must be raised in the heat pump manager menu under
SETTINGS / HEATING / HEATING CIRCUIT.
Note
If no remote control is installed, raising the parameter
“COMFORT TEMPERATURE” leads to a parallel offset of
the heating curve.
Increase the parameter “heating curve” if the room temperature
is not high enough when outside temperatures are low.
If the parameter “heating curve” has been raised, adjust the zone
valve or thermostatic valve in the lead room to the required tem-
perature at high outside temperatures.
!
Material losses
Never reduce the temperature in the entire building by
closing all zone or thermostatic valves, instead use the
setback programs.
When everything has been implemented correctly, the system
can be heated to its maximum operating temperature and vented
once again.
!
Material losses
With underfloor heating systems, observe the maximum
permissible temperature for the system.
11.4 Appliance handover
Explain the appliance function to users and familiarise them with
its operation.
Note
Hand over these operating and installation instructions
to the user for safe-keeping. Carefully observe all infor-
mation in these instructions. They provide information
on safety, operation, installation and maintenance of the
appliance.
11.5 Operation and control
!
Appliance and system damage
Never interrupt the power supply, not even outside the
heating season. The system’s active frost protection is not
guaranteed if the power supply is interrupted.
The system should not be switched off in summer. The heat pump
manager has an automatic summer / winter changeover.
12. Shutting down
If the system is taken out of use, set the heat pump manager to
standby. This way the safety functions that protect the system
remain enabled, e.g. frost protection.
!
Appliance and system damage
If the heat pump and frost protection are completely
switched off, drain the system on the water side.