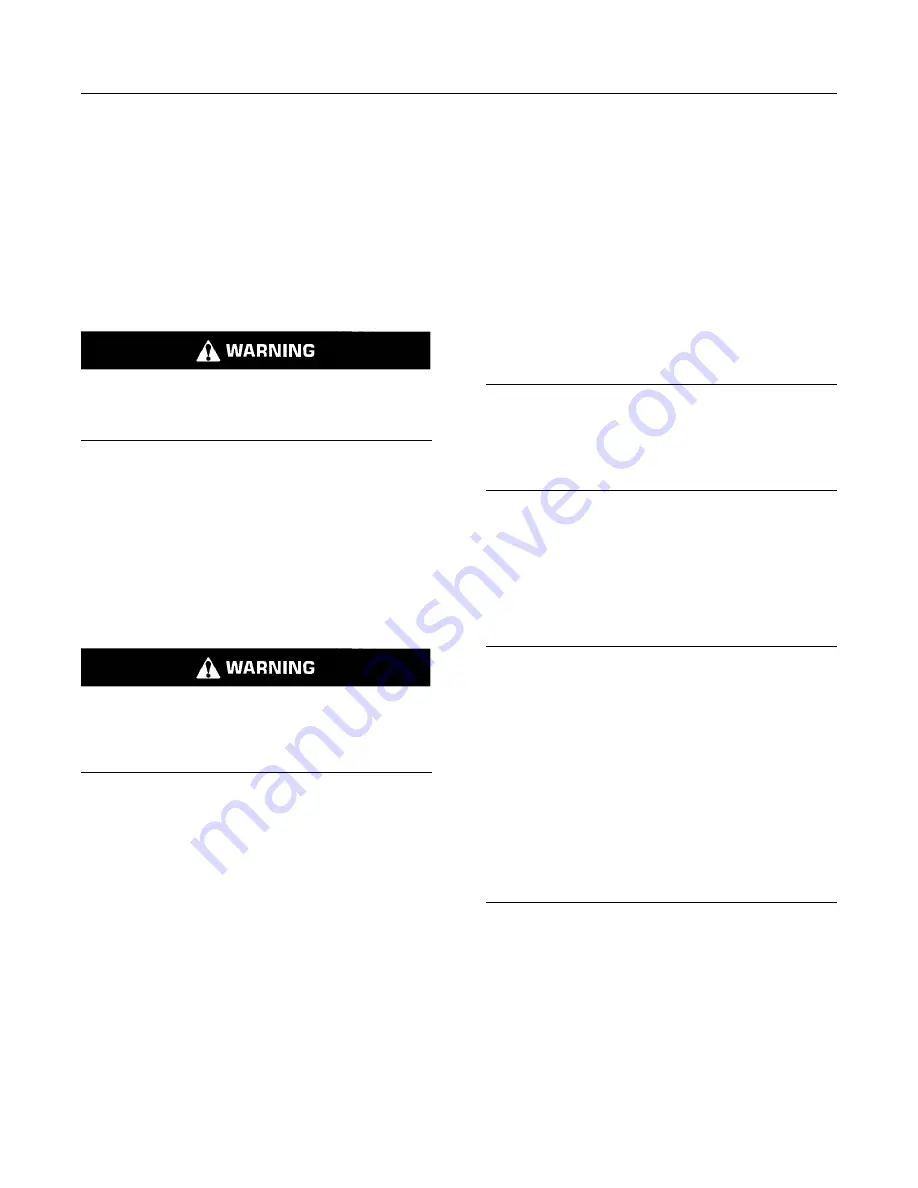
Maintenance
Recommendations
i02909163
System Pressure Release
SMCS Code:
1250; 1300; 1350; 5050
Coolant System
Pressurized system: Hot coolant can cause seri-
ous burn. To open cap, stop engine, wait until ra-
diator is cool. Then loosen cap slowly to relieve
the pressure.
To relieve the pressure from the coolant system, turn
off the engine. Allow the cooling system pressure cap
to cool. Remove the cooling system pressure cap
slowly in order to relieve pressure.
Fuel System
To relieve the pressure from the fuel system, turn off
the engine.
High Pressure Fuel Lines (If Equipped)
Contact with high pressure fuel may cause fluid
penetration and burn hazards. High pressure fuel
spray may cause a fire hazard. Failure to follow
these inspection, maintenance and service in-
structions may cause personal injury or death.
The high pressure fuel lines are the fuel lines that are
between the high pressure fuel pump and the high
pressure fuel manifold and the fuel lines that are
between the fuel manifold and cylinder head. These
fuel lines are different from fuel lines on other fuel
systems.
This is because of the following differences:
• The high pressure fuel lines are constantly
charged with high pressure.
• The internal pressures of the high pressure fuel
lines are higher than other types of fuel system.
Before any service or repair is performed on the
engine fuel lines, perform the following tasks:
1.
Stop the engine.
2.
Wait for ten minutes.
Do not loosen the high pressure fuel lines in order to
remove air pressure from the fuel system.
Engine Oil
To relieve pressure from the lubricating system, turn
off the engine.
i05909227
Welding on Engines with
Electronic Controls
SMCS Code:
1000
NOTICE
Because the strength of the frame may decrease,
some manufacturers do not recommend welding onto
a chassis frame or rail. Consult the OEM of the equip-
ment or your Cat dealer regarding welding on a chas-
sis frame or rail.
Proper welding procedures are necessary in order to
avoid damage to the engine ECM, sensors, and
associated components. When possible, remove the
component from the unit and then weld the
component. If removal of the component is not
possible, the correct procedure must be followed.
When welding on a unit that is equipped with a Cat
Electronic Engine, the following is considered to be
the safest procedure:
NOTICE
Do not ground the welder to electrical components
such as the ECM or sensors. Improper grounding
can cause damage to the drive train, the bearings,
hydraulic components, electrical components, and
other components.
Do not ground the welder across the centerline of the
package. Improper grounding could cause damage
to the bearings, the crankshaft, the rotor shaft, and
other components.
Clamp the ground cable from the welder to the com-
ponent that will be welded. Place the clamp as close
as possible to the weld. This will help reduce the pos-
sibility of damage.
Note:
Perform the welding in areas that are free from
explosive hazards.
1.
Stop the engine. Turn the switched power to the
OFF position.
2.
Disconnect the negative battery cable from the
battery. If a battery disconnect switch is provided,
open the switch.
SEBU8312-03
51
Summary of Contents for TANVAC HDV3000
Page 2: ...1300 998 784 STGGLOBAL NET OPERATORS MANUAL TANVAC HDV3000 Sec on 1 ...
Page 11: ...8 4 COMPONENT IDENTIFICATION Engine Control Panel Control Panel ...
Page 14: ...11 Water System Water pump Switch Water Pump ...
Page 15: ...12 Water Strainer Hose Reel ...
Page 16: ...13 Water Tank Drain Valve Lever Vacuum System Dump valve Suction Valve ...
Page 17: ...14 Blower Vacuum ...
Page 19: ...16 Primary Shutoff Assembly Collection Tank Interior Bag House Lid ...
Page 20: ...17 Bag House Drain Valve Tools Water Gun ...
Page 34: ...31 20 3000lt ELECTRIC CONTROL BOX CIRCUIT DIAGRAM 1 ...
Page 35: ...32 21 3000lt ELECTRIC CONTROL BOX CIRCUIT DIAGRAM 2 ...
Page 36: ...33 22 3000lt VACUUM UNIT BOTTOM RAIL ASSEMBLE ...
Page 37: ...1300 998 784 STGGLOBAL NET OPERATORS MANUAL Cat 2 2 Opera on Manual Sec on 2 ...
Page 137: ... Table 32 contd 100 SEBU8312 03 Reference Information Section Maintenance Log ...
Page 141: ......
Page 144: ...1300 998 784 STGGLOBAL NET OPERATORS MANUAL Comet Manual Sec on 3 ...
Page 161: ...1300 998 784 STGGLOBAL NET OPERATORS MANUAL Sutorbilt R Series Sec on 4 ...
Page 200: ...SB 7 632 Page 39 SECTION 8 PARTS LIST ...
Page 202: ...SB 7 632 Page 41 ...
Page 204: ...SB 7 632 Page 43 301GAE810 A Ref Drawing ...
Page 206: ...SB 7 632 Page 45 ...
Page 208: ...SB 7 632 Page 47 ...
Page 210: ...SB 7 632 Page 49 303GAE810 A Ref Drawing ...
Page 212: ...SB 7 632 Page 51 ...
Page 214: ...SB 7 632 Page 53 ...
Page 216: ...SB 7 632 Page 55 300GAE810 A Ref Drawing ...
Page 218: ...SB 7 632 Page 57 ...
Page 220: ...SB 7 632 Page 59 ...
Page 222: ...SB 7 632 Page 61 302GAA810 A Ref Drawing ...
Page 224: ...SB 7 623 Page 63 ...
Page 226: ...1300 998 784 STGGLOBAL NET OPERATORS MANUAL Sutorbilt P Series Sec on 5 ...
Page 245: ...SB 7 622 Page 12 1 PIPE STEEL 2 SCH 80 2 MED CARBON STEEL 1 2 FIGURE 9 GEAR DRIVER SK2150 ...
Page 258: ...SB 7 622 Page 25 SECTION 8 PARTS LIST 300GAF810 B Ref Drawing ...
Page 260: ...SB 7 622 Page 27 300GAG810 A Ref Drawing ...
Page 262: ...SB 7 622 Page 29 300GAH810 A Ref Drawing ...
Page 265: ......
Page 266: ...1300 998 784 STGGLOBAL NET OPERATORS MANUAL Lofa Manual Sec on 6 ...
Page 294: ...1300 998 784 STGGLOBAL NET OPERATORS MANUAL Excava on Hydro SWMS Sec on 7 ...
Page 314: ...1300 998 784 STGGLOBAL NET OPERATORS MANUAL Pressure Cleaner Water SWMS Sec on 8 ...