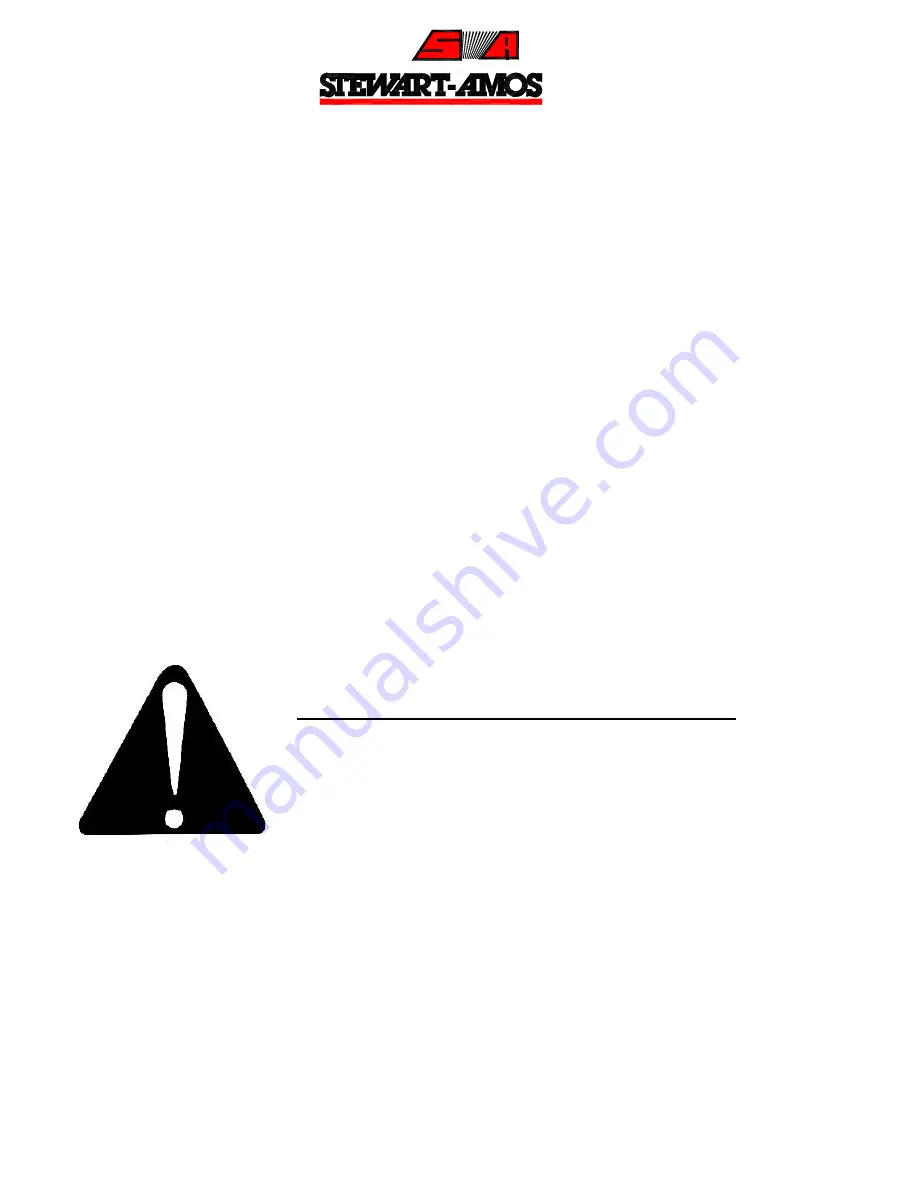
Sweeper Co.
16
Last Update July 2013
Equipment Lockout
It is strongly recommended that a commonly known Equipment Lockout procedure be enforced
at your work environment. This is a series of precautions designed to protect any personnel that
is inspecting, cleaning, or repairing the equipment. The Lockout Procedure should include the
following.
1. Apply Parking Brake.
2. Place hopper, hopper door in secure positions so that they can not accidentally fall. If
required, install additional blocking devices such as hopper safety pins.
3. Turn off Auxiliary Engine.
4. With auxiliary engine off, turn key to run position and work hydraulic functions to relieve
any residual pressure in the hydraulic system.
5. Remove keys from ignition.
6. Store keys in pocket or in a safe controlled area.
7. Place an "OUT OF SERVICE" sign on the steering wheel using a non-reusable fastener.
8. Place an "OUT OF SERVICE" sign on the front window.
9. Disconnect negative terminal from battery.
Hopper Port Restrictors
To control the decent of the hopper under all conditions port restrictors are used in the hopper lift
cylinders. These port restrictors are sized to give a controlled decent of the hopper even if a
hydraulic hose would rupture with a full hopper at the top of its travel. The hopper would come
back to the at rest position with minimal damage to the equipment.
DANGER: Do not remove or modify any port restrictors
Summary of Contents for Starfire S-5
Page 2: ...Sweeper Co 2 Last Update July 2013 ...
Page 13: ...Sweeper Co 13 Last Update July 2013 ...
Page 14: ...Sweeper Co 14 Last Update July 2013 Safety ...
Page 26: ...Sweeper Co 26 WARRANTY ...
Page 31: ...Sweeper Co 31 ...
Page 32: ...Sweeper Co 32 General Specifications ...
Page 36: ...Sweeper Co 36 Controls ...
Page 38: ...Sweeper Co 38 Figure 2 Engine Control Box ...
Page 42: ...Sweeper Co 42 Figure 3 Sweeper Control Box to SN 5002 and up ...
Page 43: ...Sweeper Co 43 ...
Page 44: ...Sweeper Co 44 Operation ...
Page 49: ...Sweeper Co 49 ...
Page 59: ...Sweeper Co 59 Figure 6 Gutter Broom Assembly ...
Page 60: ...Sweeper Co 60 Figure 7 Correct Broom Pattern ...
Page 63: ...Sweeper Co 63 Refer to Figure 9 Elevator Chain Adjustment ...
Page 64: ...Sweeper Co 64 REPAIR AND MAINTENANCE ...
Page 69: ...Sweeper Co 69 Figure 13 Elevator ...
Page 75: ...Sweeper Co 75 Electrical Activation Sequences at Valve Connectors ...
Page 76: ...Sweeper Co 76 Lubrication and Maintenance Check List ...
Page 82: ...Sweeper Co 82 ...
Page 83: ......
Page 84: ......
Page 85: ......
Page 86: ......
Page 87: ......
Page 88: ......
Page 89: ......
Page 90: ......
Page 91: ......
Page 92: ......
Page 93: ......
Page 94: ......
Page 95: ......
Page 96: ......
Page 97: ......
Page 98: ......
Page 99: ......
Page 100: ......
Page 101: ......
Page 102: ......
Page 103: ......
Page 104: ......
Page 105: ......
Page 106: ......
Page 107: ......
Page 108: ......
Page 109: ......
Page 110: ......
Page 111: ......
Page 112: ......
Page 113: ......
Page 114: ......
Page 115: ......
Page 116: ......
Page 117: ......
Page 118: ......
Page 119: ......
Page 120: ......
Page 121: ......
Page 122: ......
Page 123: ......
Page 124: ...Sweeper Co ...
Page 125: ......
Page 126: ......
Page 127: ......
Page 128: ......
Page 129: ......
Page 130: ...HYD ENGINE IGNITION ...
Page 132: ......
Page 133: ...H GB EXTEND H GB RETRACT RH SWEEP H SWEEP H SWEEP REV H GB H GB ...
Page 135: ......
Page 136: ......
Page 137: ......
Page 138: ...PT 43201 8 UNIT ...
Page 139: ...PT 43205 4 UNIT PT 43207 4 UNIT ...
Page 140: ...PT 43209 2 UNIT PT 43211 4 UNIT ...
Page 141: ...PT 43213 1 UNIT PT 43215 4 UNIT ...
Page 142: ...PT 43217 2 UNIT PT 43219 1 UNIT ...
Page 143: ...PT 43221 1 UNIT PT 43223 4 UNIT PT 43225 1 UNIT ...
Page 144: ...PT 43227 2 UNIT PT 43229 7 UNIT ...
Page 145: ...PT 43231 2 UNIT PT 43233 2 UNIT PT 43235 1 UNIT PT 43237 1 UNIT ...
Page 146: ...PT 43239 1 UNIT PT 43243 3 UNIT PT 43258 1 UNIT ...
Page 147: ...PT 43259 2 UNIT PT 43256 1 UNIT ...