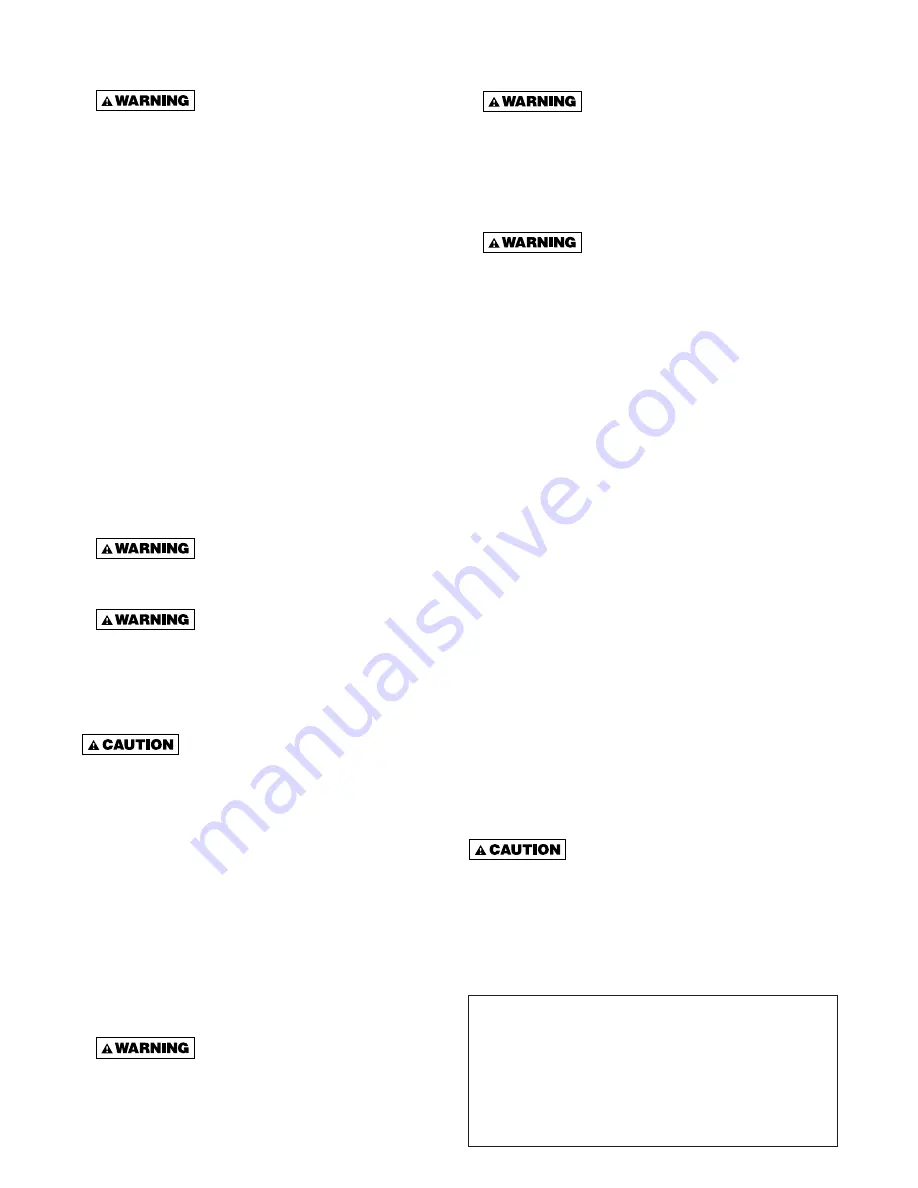
3
GENERAL SAFETY INFORMATION
Failure to comply with the general
safety information may result in extensive
property damage, severe personal injury, or
death.
Installation must be made in accordance with local
codes, or in absence of local codes, with the latest
edition of ANSI Standard Z223.1 (N.F.P.A. No. 54)
National Fuel Gas Code.
All of the ANSI and NFPA
Standards referred to in these installation instructions
are those that were applicable at the time the design of
this appliance was certified. The ANSI Standards
are available from CSA Information Services,1-800-463-
6727. The NFPA Standards are available from the
National Fire Protection Association, Batterymarch Park,
Quincy, MA 02269.
If installed in Canada, the installation must conform with
local building codes, or in the absence of local building
codes, with CGA-B149.1 "Installation Codes for Natural
Gas Burning Appliances and Equipment" or CGA-B149.2
"Installation Codes for Propane Gas Burning Appliances
and Equipment." These unit heaters have been designed
and certified to comply with CGA 2.6.
Do not alter the unit heater in any
way or damage to the unit and/or severe personal
injury or death may occur!
Disconnect all power and gas
supplies before installing or servicing the heater.
If the power disconnect is out of sight, lock it in
the open position and tag it to prevent unexpected
application of power. Failure to do so could result
in fatal electric shock, or severe personal injury.
Ensure that all power sources conform
to the requirements of the unit heater, or damage to
the unit will result!
Follow installation instructions CAREFULLY to avoid
creating unsafe conditions. All wiring should be done
and checked by a qualified electrician, using copper wire
only. All gas connections should be made and leak-
tested by a suitably qualified individual, per instructions
in this manual. Also follow procedures listed on "Gas
Equipment Start-Up Sheet" located in this manual.
Use only the fuel for which the heater is designed (see
rating plate). Using LP gas in a heater that requires
natural gas, or vice versa, will create risk of gas leaks,
carbon monoxide poisoning, and explosion.
This product must be installed by
a licensed plumber or gas fitter when installed
within the Commonwealth of Massachusetts.
Do not attempt to convert the
heater for use with a fuel other than the one
intended. Such conversion is dangerous, as it
will create the risks previously listed.
Make certain that the power source conforms to the
electrical requirements of the heater.
Do not depend upon a thermostat
or other switch as sole means of disconnecting
power when installing or servicing heater. Always
disconnect power at main circuit breaker as
described above. Failure to do so could result in
fatal electric shock.
Special attention must be given to any grounding
information pertaining to this heater. To prevent the risk
of electrocution, the heater must be securely and
adequately grounded. This should be accomplished by
connecting a ground conductor between the service panel
and the heater. To ensure a proper ground, the grounding
means must be tested by a qualified electrician.
Do not insert fingers or foreign objects into heater or its
air moving device. Do not block or tamper with the heater
in any manner while in operation, or just after it has been
turned off, as some parts maybe hot enough to cause
injury.
This heater is intended for general heating applications
ONLY. It must NOT be used in potentially dangerous
locations such as flammable, explosive, chemical-laden,
or wet atmospheres.
Do not attach ductwork to this product or use it as a
makeup air heater. Such usage voids the warranty and
will create unsafe operation.
In cases in which property damage may result from
malfunction of the heater, a back-up system or
temperature sensitive alarm should be used.
The open end of piping systems being
purged shall not discharge into areas where there
are sources of ignition or into confined spaces
UNLESS precautions are taken as follows: (1) by
ventilation of the space, (2) control of the purging
rate, (3) elimination of all hazardous conditions. All
precautions must be taken to perform this operation
in a safe manner!
Unless otherwise specified, the following conversions
may be used for calculating SI unit measurements:
1 foot = 0.305 m
1 inch = 25.4 mm
1 gallon = 3.785 L
1 pound = 0.453 kg
1 psig = 6.894 kPa
1 cubic foot = 0.028m
3
1000 BTU/cu. ft. = 37.5 MJ/m
3
1000 BTU per hour = 0.293 kW
1 inch water column = 0.249 kPa
liter/second = CFM x 0.472
meters/second = FPM ÷ 196.8
Summary of Contents for Separated Combustion Tubular Gas Fired Unit Heater
Page 13: ...13 Figure 7 Vertical Intake Vent Installation Figure 6A Concentric Vent Installation...
Page 27: ......
Page 28: ......