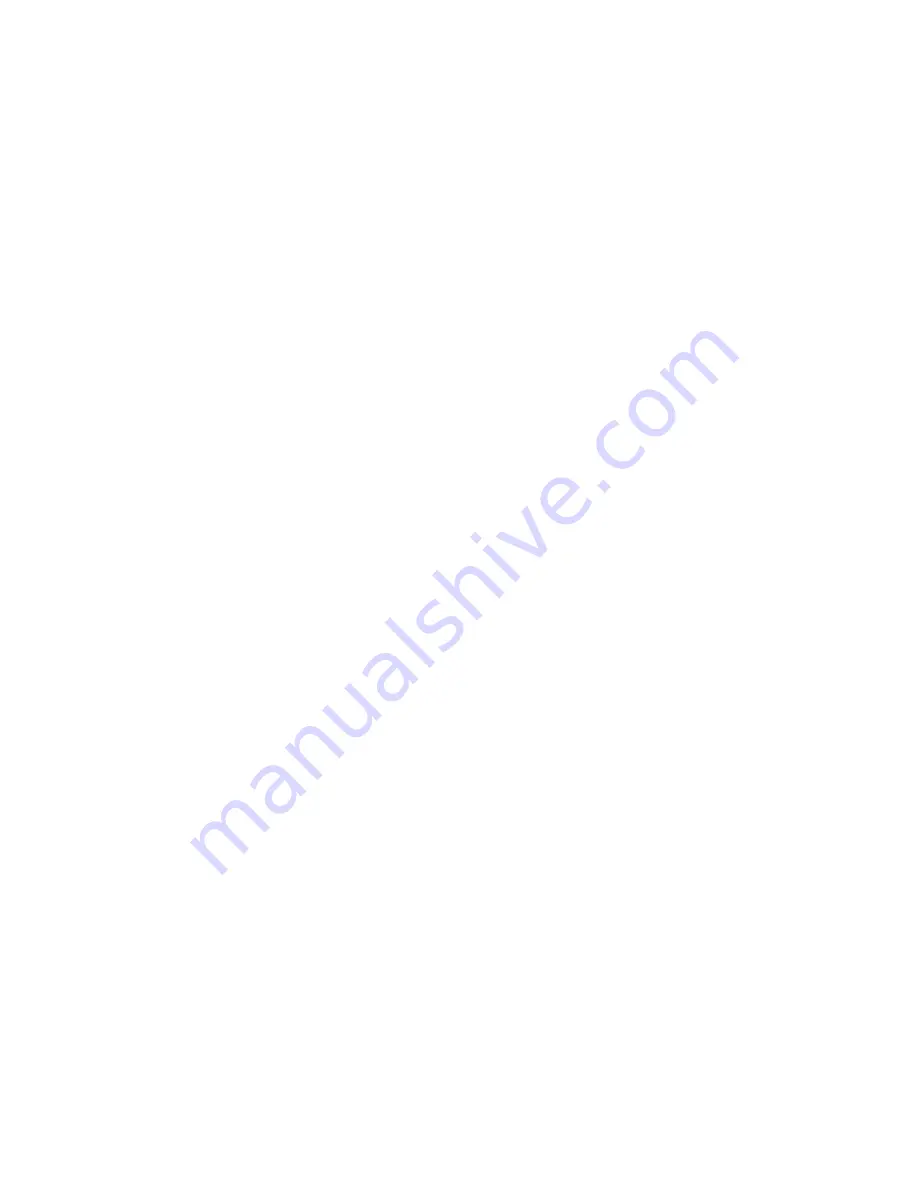
15
VENTING (continued)
VERTICAL TERMINATION
Select location on roof for vent terminal, ensuring
adequate space inside the building/structure for
concentric vent box. Terminal must be at least 6 feet
(1.8m) from any wall or adjoining building. See Figure
7.
Cut a hole through the roof for a 6 inch (152mm)
combustion air pipe. Concentric vent box is to be
suspended from the underside of the roof using
suitable brackets (field supplied). Before mounting box,
cut a length of 6 inch pipe so that dimension A, Figure
6, is equal to the dimension from the top of the box to
the roof surface plus 20 inches or plus maximum
expected snow depth, whichever is greater. Fasten 6
inch pipe to combustion air inlet connection of
concentric vent box and seal joint. Insert pipe through
roof and fasten vent box in place. Flash and/or caulk 6
inch pipe to roof. Install inlet air screen assembly and
fasten to 6 inch pipe with screws. Insert a 5 foot length
of Type B vent pipe through the 4-1/2 inch openings
with the "UP" arrow pointing up. Position the pipe to
extend 12 inches beyond the inlet air screen. Secure
the Type B vent pipe in position by drilling three small
equally spaced holes through the collar of the
concentric vent box and inserting sheet metal screws.
Install deflector disk on Type B vent pipe 2-1/2 inches
above inlet air screen and fasten with screws. Seal joint
between deflector disk and pipe with silicone sealant.
Install vent terminal on top of Type B vent pipe, fasten
with screws and seal joint.
Connect flue pipe and combustion air pipe from
concentric vent box to unit, following instructions on
pages 11 and 12. Joint between Type B vent pipe and
single wall vent pipe must be sealed with high
temperature silicone sealant. (See Figure 6A) Collars
on unit and on concentric vent box are sized so that
crimped ends of combustion air pipes go toward the
unit and crimped ends of flue pipes go away from the
unit.
HORIZONTAL TERMINATION
Select a location on outside wall for vent terminal. In
most applications, the terminal should be on level with
the flue outlet of the unit less a 1/4 inch per foot pitch
for condensate drainage toward the outside of the
building. See Figure 8.
The location of the vent terminal must be in accordance
with the National Fuel Gas Code ANSI Z223.1 in the
U.S. or the Natural Gas Installation Code CAN/CGA-
B149.1 or the Propane Gas Installation Code CAN/
CGA-149.2 in Canada. See Table 3 for minimum
clearances. In Canada, a vent shall not terminate
above a meter/regulator assembly within 3 feet (.9m)
horizontally of the vertical centerline of the regulator
nor within 6 feet (1.8m) of any gas service regulator
vent outlet.
Cut a hole through the wall for a 6 inch (152mm)
combustion air pipe. Install thimble if required by local
codes or type of wall construction. Concentric vent box
may be fastened directly to wall or spaced away from
wall using suitable brackets (field supplied). Cut a
length of 6 inch pipe so that it will protrude 4 inches
(102mm) through the wall when the box is mounted in
position. Fasten pipe to box with sheet metal screws,
using at least three screws per joint. Seal joint with
silicone sealant. Insert pipe through wall and fasten
adapter box in place so that the pipe pitches downward
1/4 inch per foot (21mm/m) toward the outside. Flash
and/or caulk 6 inch pipe on outside wall. Install inlet air
screen assembly and fasten to 6 inch pipe with screws.
Insert a 3 foot length of 4 inch Type B vent pipe
through the 4-1/2 inch openings with the "UP" arrow
pointing toward the outside. Position the pipe to extend
12 inches beyond the inlet air screen. Secure the Type
B vent pipe in position by drilling three small equally
spaced holes through the collar of the concentric vent
box and inserting sheet metal screws. Install deflector
disk on Type B vent pipe 2-1/2 inches (63.5mm) from
inlet air screen and fasten with screws. Install vent
terminal on end of Type B vent pipe, fasten with screws
and seal joint.
Connect flue pipe and combustion air pipe from
concentric vent box to unit, following instructions on
pages 11 and 12. Joint between Type B vent pipe and
single wall vent pipe must be sealed with high
temperature silicone sealant. (See Figure 6A) Collars
on unit and on concentric vent box are sized so that
crimped ends of combustion air pipes go toward the
unit and crimped ends of flue pipes go away from the
unit.
Summary of Contents for Separated Combustion Tubular Gas Fired Unit Heater
Page 13: ...13 Figure 7 Vertical Intake Vent Installation Figure 6A Concentric Vent Installation...
Page 27: ......
Page 28: ......