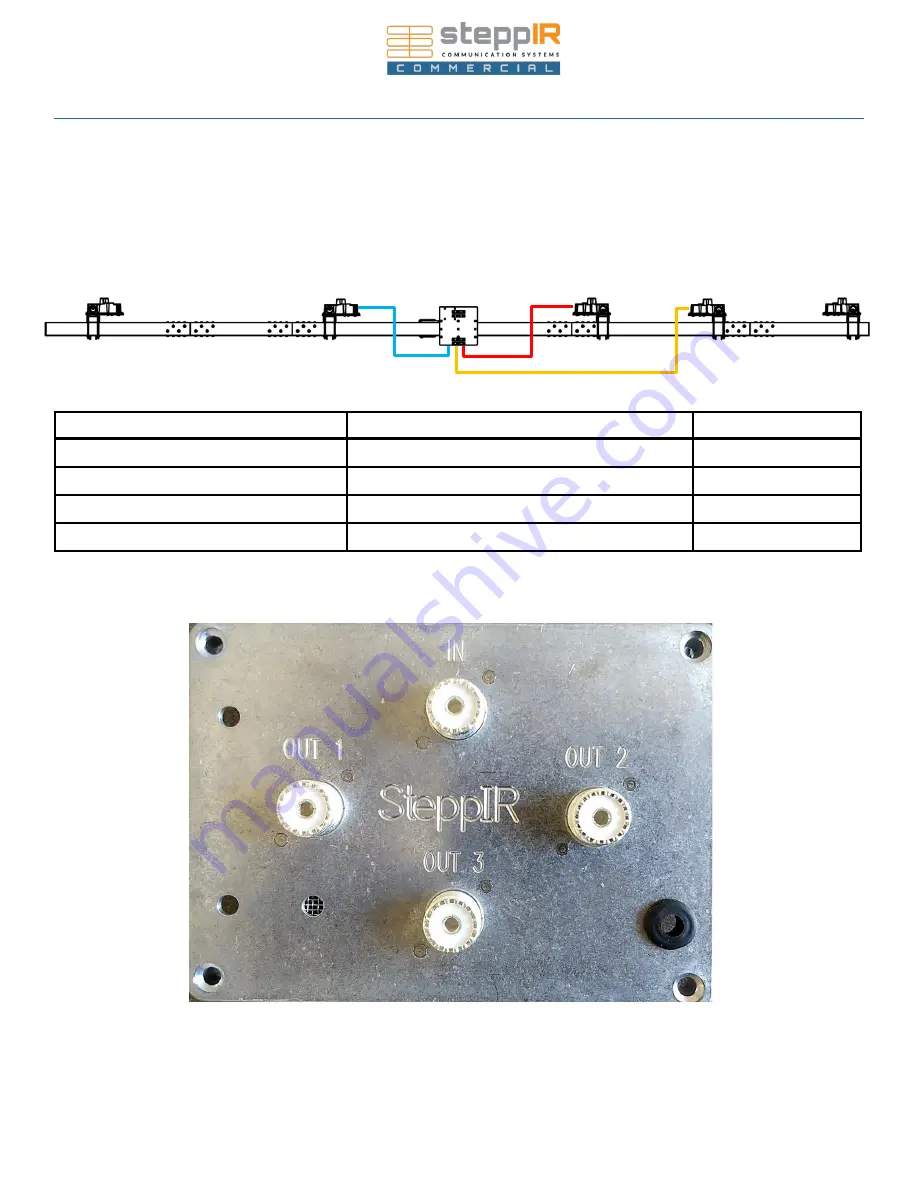
COAX JUMPER CONNECTIONS
Tech Support:
consumer.steppir.com/support | 425.453.1910 | [email protected]
39
•
Use the provided coax jumpers and connect the EHU coax ports to the coax antenna switch as shown.
•
Apply dielectric grease to the center conductors of all coax connections.
•
Tighten the coax connectors with pliers.
•
Use provided coax seal or silicone tape (not provided) to seal the coax connections (both at the EHUs and at the
coax switch box).
D2
D1
DVR
OUT 1
COAX SWITCH SO239 CONNECTOR
COAX PURPOSE
JUMPER LENGTH
IN
FEEDLINE FROM SHACK
N/A
OUT 1
COAX JUMPER TO DRIVEN EHU
11 FT 6 IN
OUT 2
COAX JUMPER TO DIRECTOR 1 EHU
4 FT
OUT 3
COAX JUMPER TO DIRECTOR 2 EHU
8 FT
COAX ANTENNA SWITCH
OUT 2
OUT 3