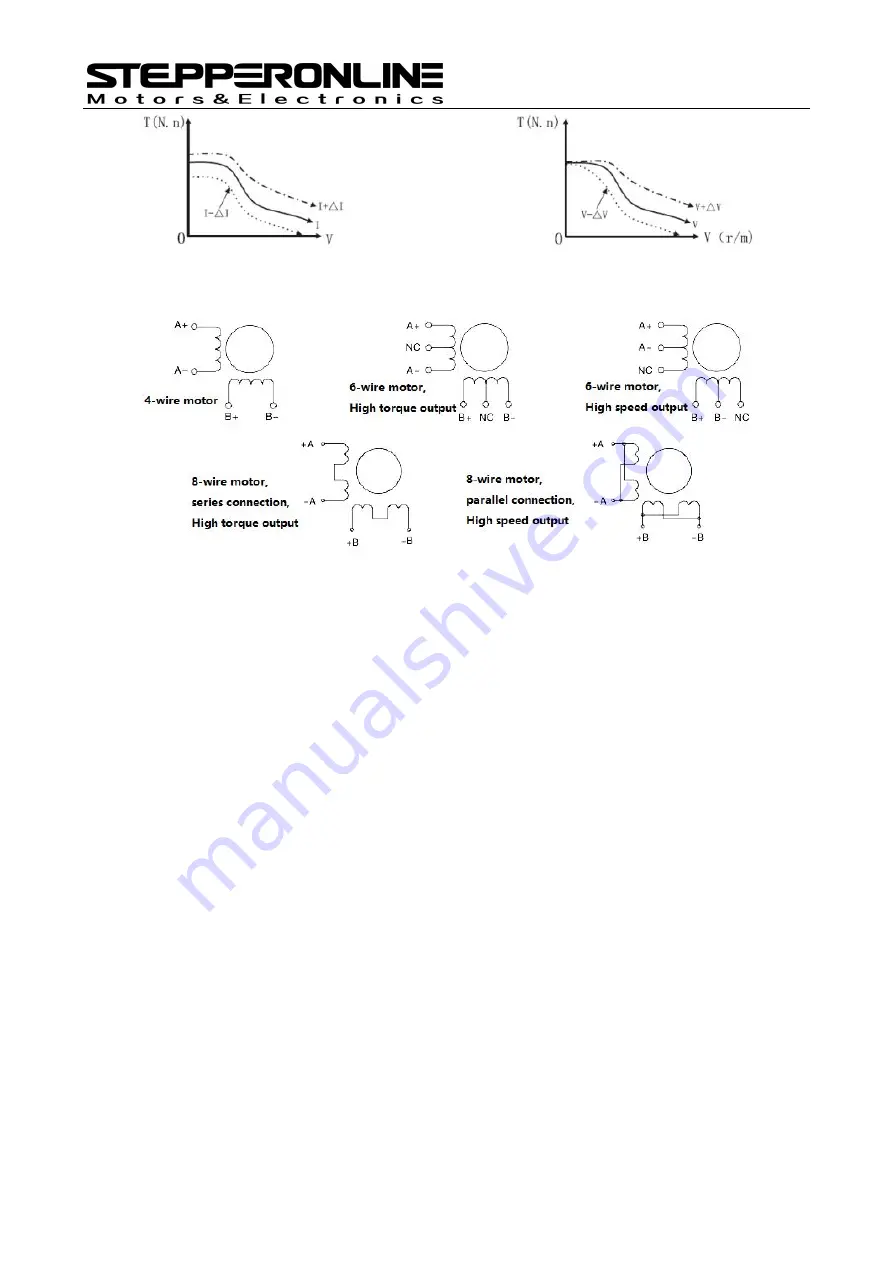
Digital Microstep Driver DM556N
10
Figure 6: Torque frequency curve diagram
6.2 Motor connection
Figure 7: Motor connection diagram
6.3 Input voltage and output current selection
The DM556N driver can drive all two-phase and four-phase hybrid stepper motors. In order to
obtain the best driving effect, it is necessary to select a reasonable supply voltage and set current.
The voltage of the power determines the high-speed performance of the motor, and the current
determines the torque of the motor.
(1). Supply voltage setting
In general, the higher the supply voltage, the greater the torque at high-speeds, and the greater the
loss of speed at high speeds. On the other hand, if the voltage is too high, the motor will generate
more heat and may even damage the driver. At high voltages, the vibration of the motor at low
speeds will be greater.
(2). Output current setting
For the same motor, the larger the current setting value, the larger the motor output torque, but the
heat generated by the motor and the driver is more serious when the current is large. The calorific
value is not only related to the current setting value, but also to the motor motion form and the
motor dwell time. The following setting method uses the rated current value of the stepper motor
as a reference, but the optimum value in practical applications should be adjusted based on this
value. If the temperature is very low (<40
℃
), the current setting value can be increased to increase
the motor output power (torque and high-speed performance).
a. 4-wire motor and high-speed mode of 6-wire motor: output current is set equal to or slightly less
than the rated current of the motor;
b. High torque mode of 6-wire motor: output current is set to 70% of rated current;
c. Series connection of 8-wire motor: because the resistance increases in series, the output current
should be set to 70% of the rated current of the motor;