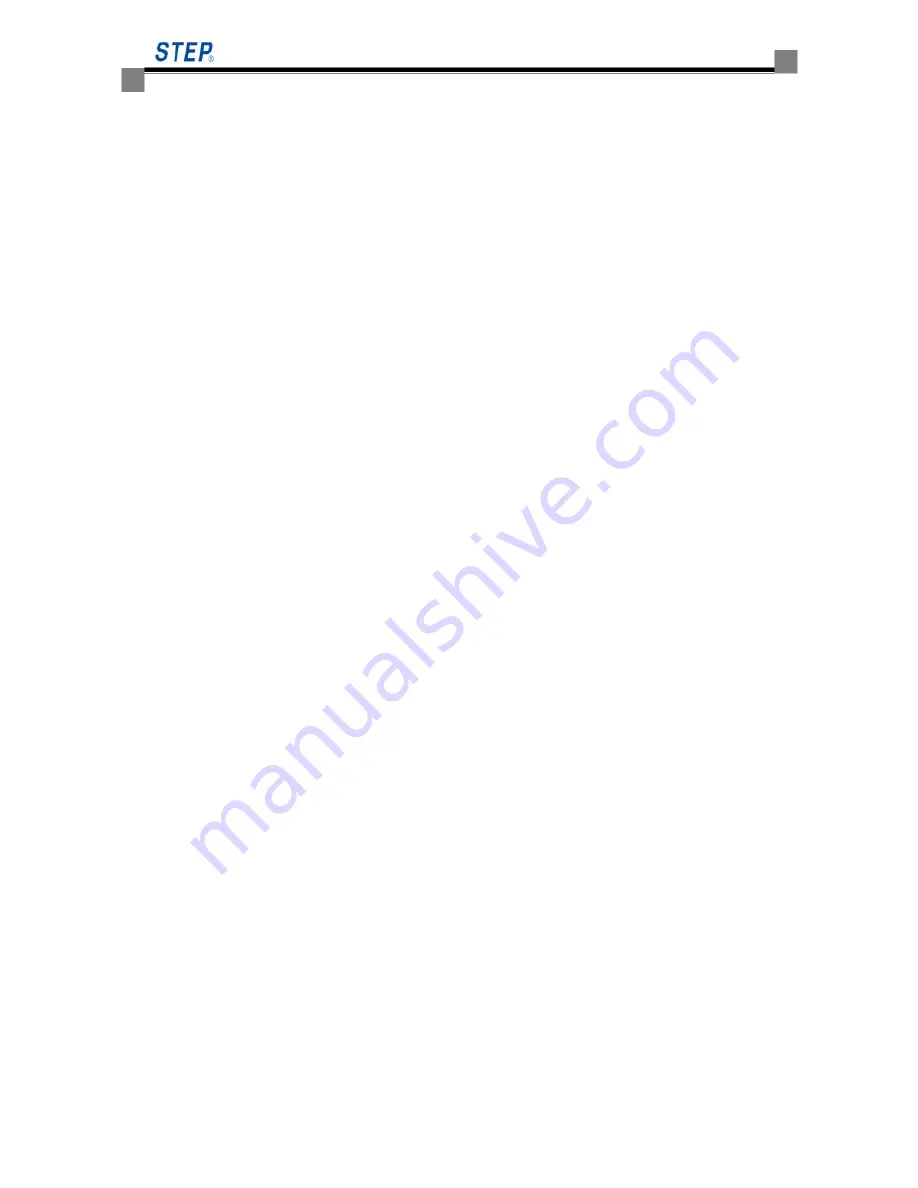
I
Using Instructions for Series AS500 Inverter for Water Pump
AS500 Universal Vector Inverter with high performance
Product Instruction
Publication state: standard
Product version: V1.00
All Copyright reserved by Shanghai Sigriner STEP
Electric Co.
,
Ltd.
The information in this document is subject to change
without prior notice. No part of this document may in
any form or by any means (electronic, mechanical,
micro-coping, photocopying, recording or otherwise) be
reproduced, stored in a retrial system or transmitted
without prior written permission from Shanghai Sigriner
STEP Electric Co., Ltd.