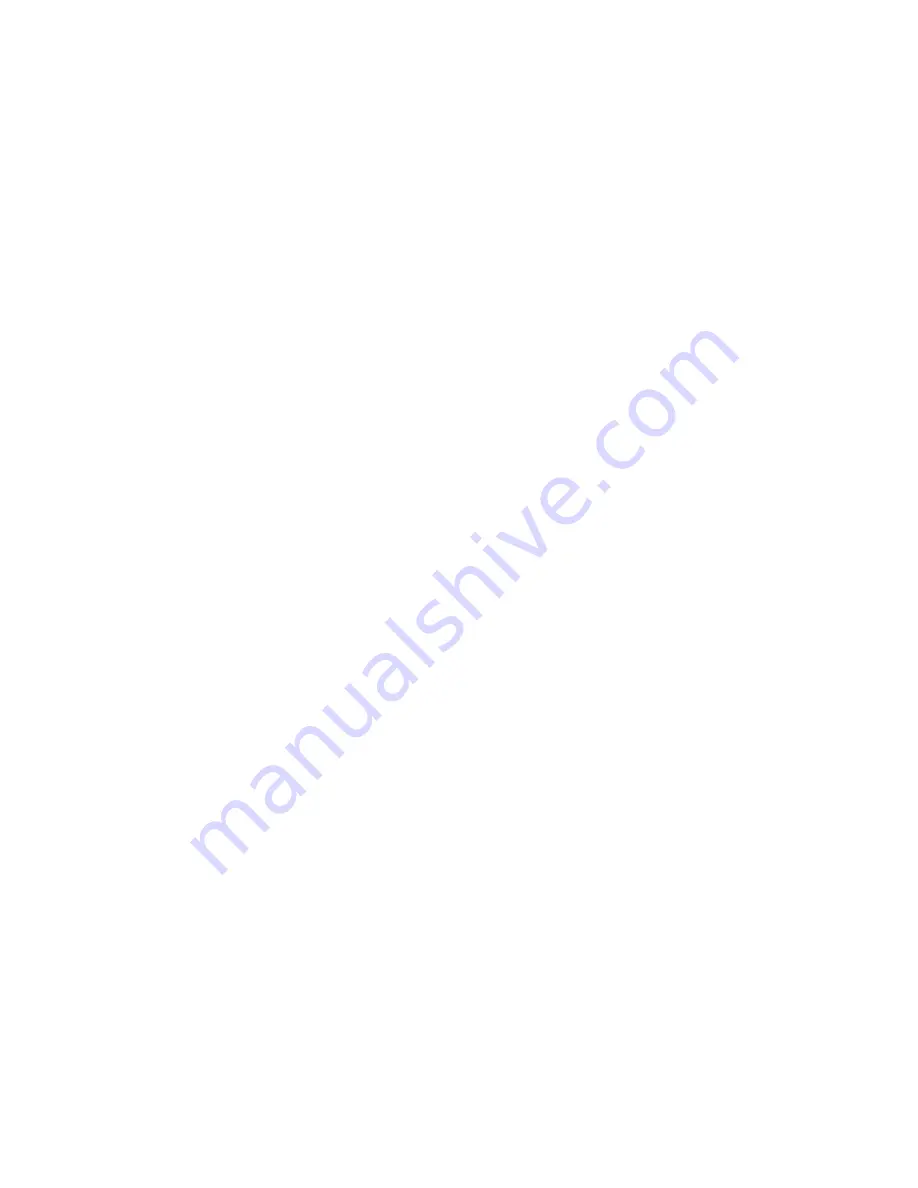
3.2 RF
C N
RF i
amp
•
•
Waveguide type WG17 or WG75 may be used. The RF output is UBR120, with
four tapped holes 6-32 UNC requiring four bolts (6-32 UNF-2B, maximum internal thread
d with sufficient bolts for this flange.
sufficient
rain or subjected to condensation,
ll attempts should be made to prevent moisture ingress into the waveguide system. It is
guide joints are made using flanges fitted with ‘O’ rings to prevent
iven is only general. Any
3.3.1
....................................................................................... 1600W
r cooling system and is equipped with two thermal
continuously
fan will rotate
at th s
llector.
When th
change
red
d
cooling
ecessary. When normal
irflow is confirmed, the amplifier can be placed back into the transmit state.
he amplifier is automatically placed in the off state if the over-temperature condition exists for more
than 4 minutes. The mains supply should be removed and the amplifier isolated before a full
O NECTIONS
nput and output connections are made via waveguide connectors on opposite ends of the
lifier.
C-Band.
Waveguide type WG14 should be used. The RF output is CPR 137F, with eight
tapped holes 10-32 UNF-2B (maximum internal thread depth 8mm). The amplifier is
provided with sufficient bolts for this flange.
X-Band.
Waveguide type WG15 should be used. The RF output is CPR 112G, with eight
tapped holes 8-32 UNC-2B requiring eight bolts. The amplifier is provided with sufficient
bolts for this flange.
•
Ku-Band.
depth 8mm). The amplifier is provide
•
DBS-Band.
Waveguide type WG18 should be used. The amplifier is provided with sufficient
bolts for this flange, (4 off 6-32 UNC-2B).
•
Tri-Band.
Waveguide type WRD580 should be used. The amplifier is provided with
bolts for this flange, (4 off 6-32 UNC-2B).
RF input signals applied must be within the frequency range specified for the particular amplifier type
(see figure 1and 2). The maximum RF input drive level should not 10dBm for pre-amplifier
option C and -10dBm for pre-amplifier options A, D or Z.
f the amplifier is to be used in applications where it is exposed to
I
a
recommended that all external wave
moisture ingress.
3.3 COOLING
CONSIDERATIONS
Temperature affects the life and reliability of high power electronic devices. As the temperature of the
device increases, generally reliability and life expectancy decrease; TWTAs are no exception. Please
follow the cooling considerations for your amplifier to ensure many trouble free years of use.
Engineers at e2v technologies have many years of experience working with customers to integrate
equipment successfully and to ensure that long and reliable product lives are achieved. The
information contained within this section has been gained from both field experience and theoretical
cooling system design knowledge. As most installations differ, the advice g
specific aspects of installation design can be discussed further by contacting (by telephone, fax or e-
mail) the Stellar Product Support Team at e2v technologies.
Some Cooling Facts and Figures
Minimum air flow................................................................................................112 litre/sec 240 ft
3
/min
Minimum
duct area .........................................................................................................250 cm
2
(39 in
2
)
Typical internal power dissipation (no RF drive):
C-
or X-band.......................................
Ku-
or DBS band ....................................................................................................................... 1500W
Tri-band
................................................................................................................................... 1800W
The amplifier utilises an efficient, integral, forced-ai
sensors to protect it in the event of an over-temperature condition. The cooling fan has a
variable speed of rotation so that, when the amplifier is operating normally, the cooling
e lowest speed consistent with adequate cooling of the TWT co
e temperature of either thermal sensor exceeds preset levels, the amplifier will automatically
state from transmit to fault. In the fault state, the dissipation within the amplifier is greatly
uce and if the airflow is normal, the amplifier will rapidly cool. At this stage, the installation
system should be visually inspected for blockages and cleaned as n
a
T
© e2v technologies (uk) limited 2010
DAS768892AA
Version
1,
page
11