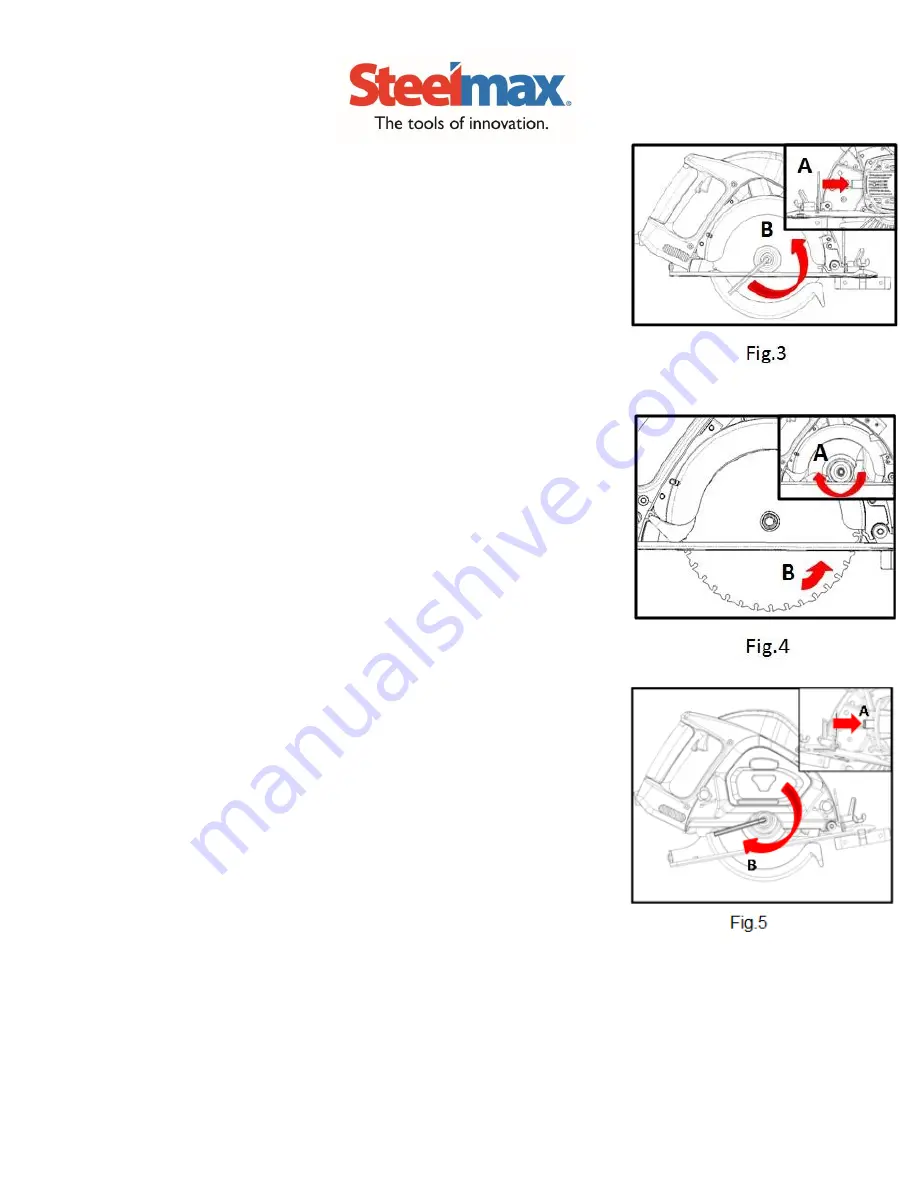
SM-S-7 XP Operator’s Manual
- 12 -
2017 Version 1.10
3.
Hold down the shaft lock lever (A) to secure the motor shaft. Use
the Allen wrench to loosen the shaft screw (B) (counter-clockwise)
and remove the shaft screw and flange. Fig.3
4.
Open the blade guard (A) and remove old blade. Align new blade with
inner flange and install the new blade and check for proper blade
orientation (B). Fig.4
5.
Install the outer flange on the blade spindle. Use the
the shaft lock lever (A) to secure the motor shaft while tightening the
shaft screw (B). Fig.5
Assemble chip shield assembly with blade housing and re-tighten lock
bolts ((B)
,
Fig.1
Be sure to repalce Allen wrench for future use.