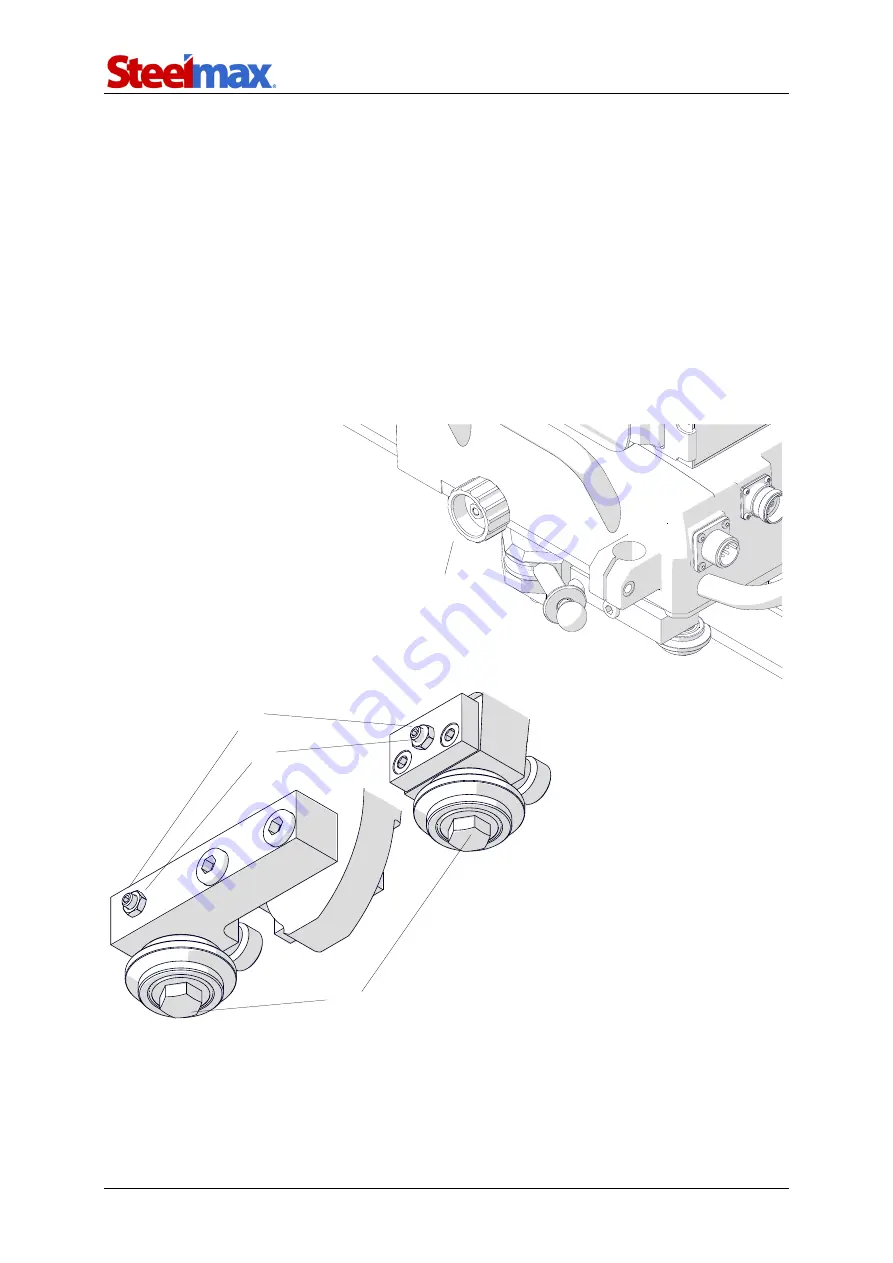
Rail Runner Gen III
Rail Runner Gen III Operator’s Manual
25
3.8. Adjusting the pressure of rollers
If the resistance during the travel is too little or too much, loosen the knob (
1
,
Fig. 13). At the opposite side of the carriage, use the 13 mm and 8 mm flat wrenches
to loosen the bolts (
2
) and nuts (
3
). Next, use the 2.5 mm hex wrench to adjust the
screws (
4
), and then tighten the bolts (
2
).
Move the carriage along the track. If the resistance is still incorrect, repeat the
above steps.
If the carriage moves smoothly, use the 2.5 mm hex wrench to prevent rotation of
each screw (
4
). Then, use the 8 mm flat wrench to tighten the nuts (
3
).
Fig. 13.
Adjusting the pressure of rollers
2
3
4
1