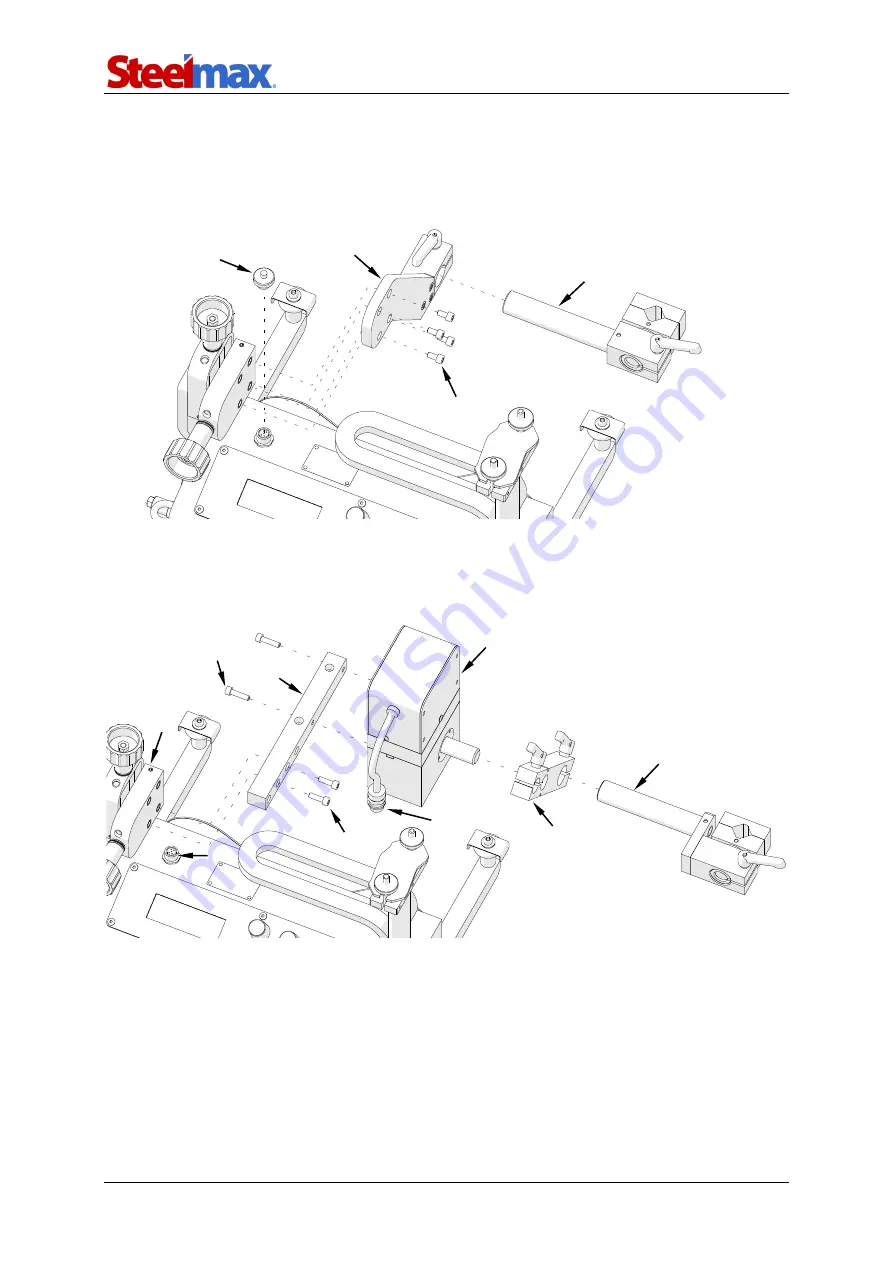
ARC Runner
ARC Runner Operator’s Manual
18
3.8. Using oscillator (accessory)
3.8.1. Installing
Install the oscillator according to the following instructions.
•
Remove the torch holder
1
.
•
Remove
the
torch
holder
plate
2
by unscrewing screws
3
with 4 mm hex wrench.
•
Unscrew the cap
4
.
•
Fix the arm
5
to the oscillator
6
.
•
Fix the oscillator
6
to the bracket
7
with two M5x20 screws
8
.
•
Fix the bracket
7
to the cross slide
10
with two M5x16 screws
9
.
•
Fix the oscillator plug
11
to the oscillation socket
12
.
•
Fix the low torch holder
13
to the oscillator arm
5
.
4
2
3
1
8
7
9
12
10
6
11
5
13
Summary of Contents for ARC Runner
Page 6: ...ARC Runner ARC Runner Operator s Manual 6 1 4 Dimensions 411 mm 16 2 368 mm 14 5 447 mm 17 6 ...
Page 24: ...ARC Runner ARC Runner Operator s Manual 24 ...
Page 37: ...ARC Runner ARC Runner Operator s Manual 37 ...
Page 52: ...ARC Runner ARC Runner Operator s Manual 52 8 115 230 V WIRING DIAGRAM ...
Page 53: ...ARC Runner ARC Runner Operator s Manual 53 9 42 V WIRING DIAGRAM ...