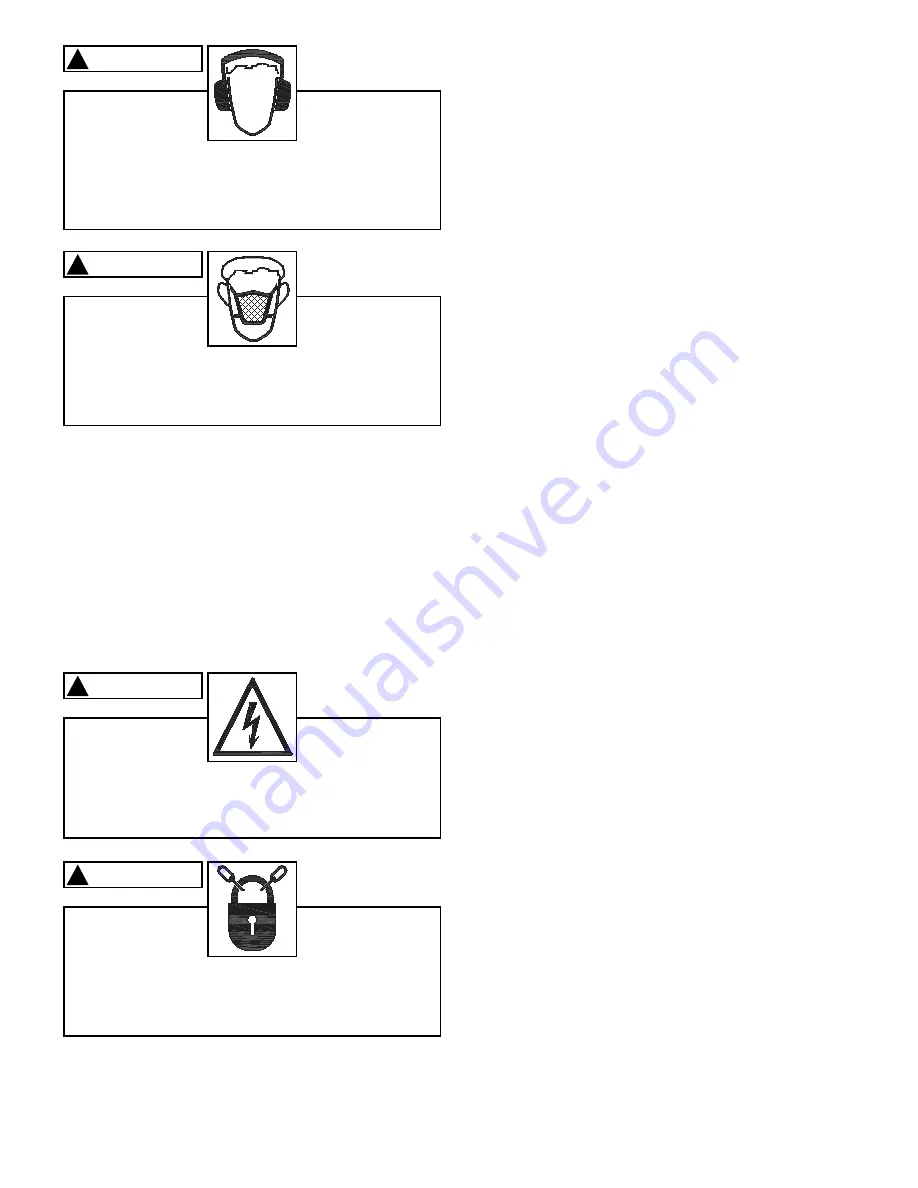
11
4.
ALWAYS
wear a NIOSH/OSHA approved dust
mask to prevent inhaling dangerous dust or air-
borne particles.
8.
AVOID
a dangerous working environment.
DO
NOT
use electrical tools in a damp environment
or expose them to rain or moisture.
9.
CHILDPROOF THE WORKSHOP AREA
by
removing switch keys, unplugging tools from the
electrical receptacles, and using padlocks.
3.
ALWAYS
wear hearing protection. Plain cotton is
not an acceptable protective device. Hearing
equipment should comply with ANSI S3.19
Standards.
WARNING
!
WARNING
!
WARNING
!
WARNING
!
11.
DO NOT FORCE
the machine to perform an opera-
tion for which it was not designed. It will do a safer
and higher quality job by only performing operations
for which the machine was intended.
12.
DO NOT
stand on a machine. Serious injury could
result if it tips over or you accidentally contact any
moving part.
13.
DO NOT
store anything above or near the machine.
14.
DO NOT
operate any machine or tool if under the
influence of drugs, alcohol, or medication.
15.
EACH AND EVERY
time, check for damaged parts
prior to using any machine. Carefully check all
guards to see that they operate properly, are not
damaged, and perform their intended functions.
Check for alignment, binding or breakage of all
moving parts. Any guard or other part that is dam-
aged should be immediately repaired or replaced.
16. Ground all machines. If any machine is supplied
with a 3-prong plug, it must be plugged into a 3-
contact electrical receptacle. The third prong is
used to ground the tool and provide protection
against accidental electric shock.
DO NOT
remove
the third prong.
17. Keep visitors and children away from any machine.
DO NOT
permit people to be in the immediate work
area, especially when the machine is operating.
18.
KEEP
protective guards in place and in working
order.
19.
MAINTAIN
your balance.
DO NOT
extend yourself
over the tool. Wear oil resistant rubber soled shoes.
Keep floor clear of debris, grease, and wax.
20.
MAINTAIN
all machines with care.
ALWAYS KEEP
machine clean and in good working order.
KEEP
all
blades and tool bits sharp.
21.
NEVER
leave a machine running, unattended. Turn
the power switch to the OFF position.
DO NOT
leave the machine until it has come to a complete
stop.
22.
REMOVE ALL MAINTENANCE TOOLS
from the
immediate area prior to turning the machine ON.
23.
SECURE
all work. When it is possible, use clamps
or jigs to secure the workpiece. This is safer than
attempting to hold the workpiece with your hands.
24.
STAY ALERT
, watch what you are doing, and use
common sense when operating any machine.
DO
NOT
operate any machine tool while tired or under
the influence of drugs, alcohol, or medication. A
moment of inattention while operating power tools
may result in serious personal injury.
5.
ALWAYS
keep the work area clean, well lit, and
organized.
DO NOT
work in an area that has slip-
pery floor surfaces from debris, grease, and wax.
6.
ALWAYS
unplug the machine from the electrical
receptacle before making adjustments, changing
parts or performing any maintenance.
7.
AVOID ACCIDENTAL STARTING
. Make sure that
the power switch is in the “OFF” position before
plugging in the power cord to the electrical
receptacle.
10.
DO NOT
use electrical tools in the presence of
flammable liquids or gasses.
Summary of Contents for 35600
Page 35: ...35 u NOTES u...
Page 36: ...36 PARTS...
Page 38: ...38...
Page 41: ...41...
Page 42: ...42 u NOTES u...
Page 44: ......