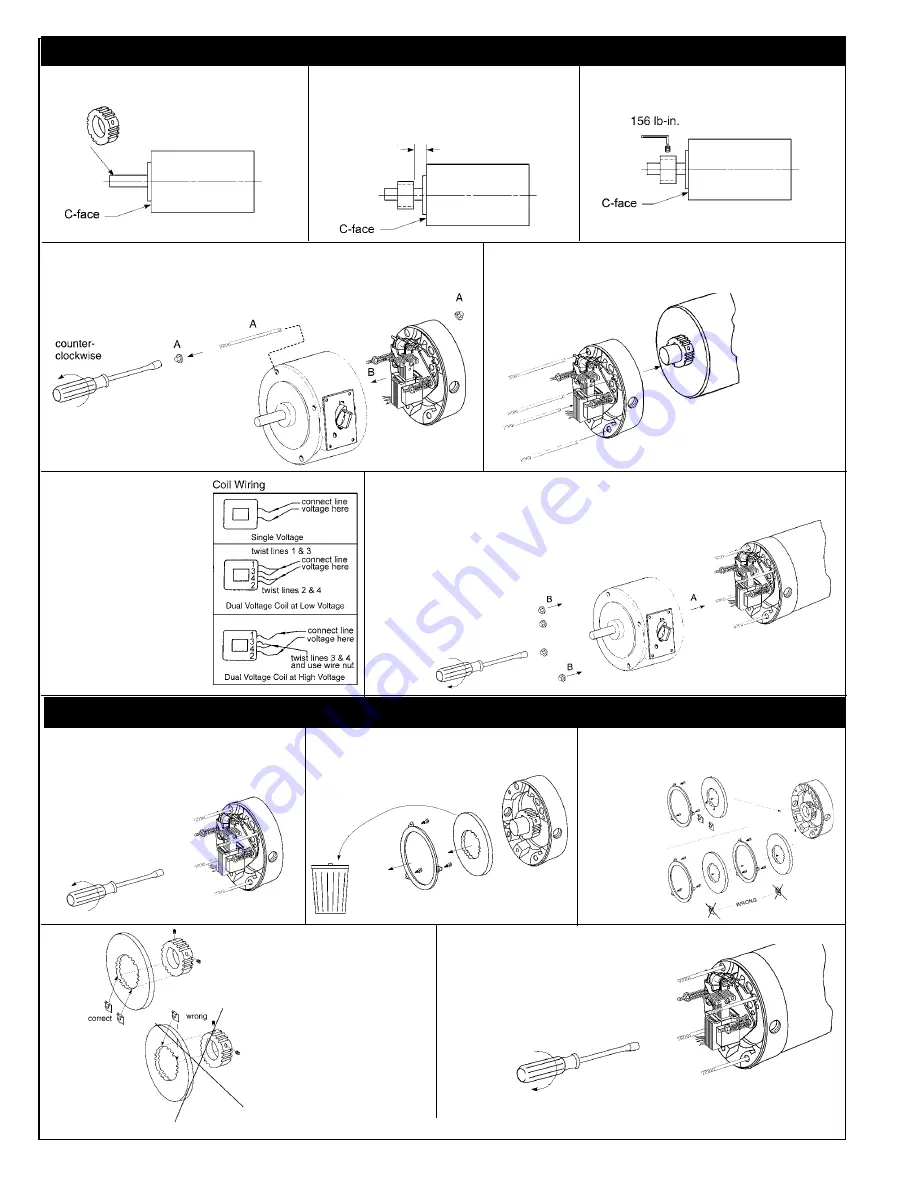
Position hub to X as shown:
X=.32” (8.1mm) for 1 & 2 disc (1.5 - 15 lb-ft)
X=.19” (4.8mm) for 3 disc (20 & 25 lb-ft)
Place hub on motor shaft.
Tighten set screws to motor shaft.
Connect coil lead-
wires to power
supply. Refer to
nameplate for volt-
age rating.*
Caution
:
Keep wiring away
from pinch points
and moving compo-
nents.
1
2
6
3
X
BRAKE MOUNTING (Manual Adjust) 1-056-700
* Stabilizer clips
are for use on
single disc units
only. Position
clips opposite
set screw holes.
Remove support plate screws and
lift support from brake
Reposition support plate on endplate and
tighten mounting screws to 55 lb-in.
Install new friction disc(s) and
stationary disc(s) as shown.
Remove and discard old friction disc.
4
2
1
3
clockwise
For brakes
with vertical
sprngs see
Figure 5A
or 5C.
FRICTION DISC REPLACEMENT SERIES 1-056-700
2
Note
: Friction discs can wear to 1/2 their original thicknes, or .093”
A. Remove housing nuts and slide tie bolt out of brake.
B. Remove housing from endplate.
4
* For vertical assembly
of 20 & 25 lb-ft brakes
refer to page 3.
Slide endplate over hub noting position of stabilizer clips, if
used. (Refer to Friction Disc Replacement view 3 and
3A). Mount
brake
endplate to
motor C-face
using the
four tie bolts.
Finger
tighten.
5
A. Slide housing and shaft assembly onto mounting studs, rotating
shaft until keyway is aligned. Be sure housing is assembled with
access windows in same position as shown in Figure 1, page 1.
B. Mount and secure brake/motor assembly to
C-face mounting register of reducer.
Using four 3/8 - 16 nuts and
lockwashers, tighten to 30-35 ft-lb.
clockwise
7
counter-clockwise
5