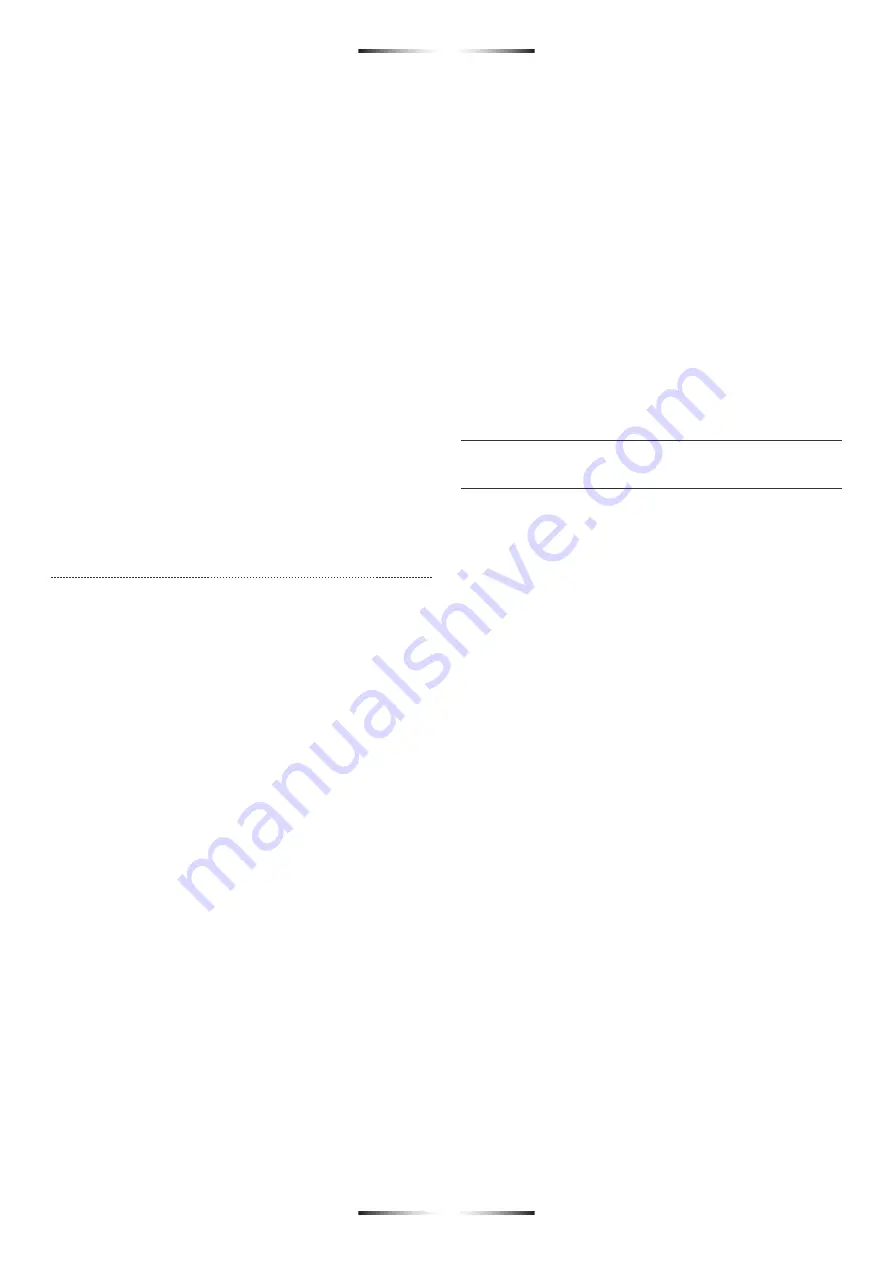
32
32
ENGLISH
Adjust current intensity in accordance with the needs of the kind
of material and the joint to be made, making first a test on a test
piece. Refer to specialized literature or regulated professional
training for further information in respect hereof.
The torch shall receive inert gas supply (usually pure argon)
proceeding from a cylinder, through a pressure reducing system
capable of suitably regulating eh necessary gas flow volume. All
equipments need a TIG torch (not included, STAYER references
38.71 and 38.73) with direct connection to the flow meter and
gas control by the flow valve in the TIG torch itself.
Once the arc has started, proceed to carry out welding
according to the needs thereof. As a general orientation, you
have to advance reversely to electrode welding so that, instead
of drawing backwards, you apply pushing frontwards as if you
were helping the gas flow impinge on the weld puddle. Incline
the torch in such a way, that it impinges in a position near (70o
to 80o) to the vertical with respect to the centered horizontal and
with respect to the weld puddle.
Slowly deposit the filler material of the rod bringing it closer
successively to the puddle of melt material.
To finish, simply stop pushing the switch of the torch, separate
the torch very slightly until the torch becomes interrupted and
close the manual gas valve. Finally, close the general flow valve
of the inert gas cylinder.
4.5.3 Specific instructions MIG/MAG wire welding
The welding torch must maintain a correct position to allow the
gas to conveniently shield the melting bed. Hold the torch with
both hands and ensure having a fixed support point for more
stability of the bead.
An inclination with respect to the vertical of 10o is recommended.
The free length of the wire shall be comprised between 8 and 20
mm, so that the melting bed may be observed and adherence of
projection to the gas nozzle may be avoided. Avoid working in air
currents that snatch technical gas from the welt bead.
Possible problems and solutions MIG/MAG welding
WELD BEAD NARROW AND WITH INTERRUPTIONS
a) Wire advance speed excessive.
b) Little gas discharge (start with 5-7 l/min and, if necessary,
open the tap of the pressure gauge more.
WELD BEAD VERY HIGH
A) Wire advance speed very low.
b) Low welding current.
UNSTABLE ARC, POROSITY OF THE WELD
a) Torch very distant from the piece.
b) Piece with grease, oil, dirty, rust.
c) Insufficient gas flow; check the contents of the gas bottle and
the gas regulator.
WIRE MELTS UP TO THE CONTACT TIP AND REMAINS
HOOLED THERETO
a) Very low wire speed
b) Torch too close to the piece
c) Momentary interruption of the welding circuit that may be
caused by:
1. Contact tip oxidized.
2. Difficulties in the wire advancing mechanism.
3. Contact tip with diameter differing from that of the wire.
4. Faulty connection of the torch.
5. Little pressure in the wire advance.
6. Wire bobbin tangled or wrongly connected, thereby braking or
complicating normal advance of the wire.
WELD LACKING PENETRATION
a) Torch advance speed too high.
b) Low welding current.
c) Wire speed to low.
ARC DOES NOT FLARE UP
A) Check connection of the machine, of the grounding clamp and
of the torch.
MACHINE DOES NOT WORK WHEN THE TORCH SWITCH
IS CONNECTED
a) Intervention of the thermostat.
b) Check operation of the TORCH SWITCH.
MACHINE DOES NOT WORK, THE LUMINOUS SWITCH
DOES NOT LIGHT UP
a) Verify connection to electric mains.
b) Verify circuit breaker switch or the fuse of the electric mains.
5. SERVICING AND MAINTENANCE
ISTRUCTIONS
Torches – specific instructions:
- Clean projections adhered in the torch outlet to avoid short-
circuit and gas turbulences. Use a steel brush.
- Avoid adherences of projections using a specific, silicone-free
spray.
- Review setting of dragging and braking rollers of the reel
periodically.
- Control wear and tear of the calibrated contact nozzle and
replace it when necessary to avoid loss of contact of the wire
with the nozzle.
Do not use torch as a hammer to remove weld rests or align
sheets.
REPAIR SERVICE
The technical service will advise you on questions you might have
regarding repair and maintenance of your product, as well as on
spare parts. You may obtain exploded drawings and information
on spare parts on the internet under: [email protected]
Our team of technical advisors will be happy to guide you
regarding the acquisition, application and setting of products and
accessories.
GUARANTEE
Guarantee card
Among the documents that are part of the electric tool, you will
find the guarantee card. You will have to fill in the guarantee
card completely, apply copy of the sales slip or invoice thereto,
and give it to your retailer in exchange for the corresponding
acknowledgement of receipt.
REMARK: If this card were missing, immediately ask you
retailer for it.
The guarantee is limited to manufacturing or machining
failures, and ceases when the parts have been disassembled,
manipulated or repaired out of works.