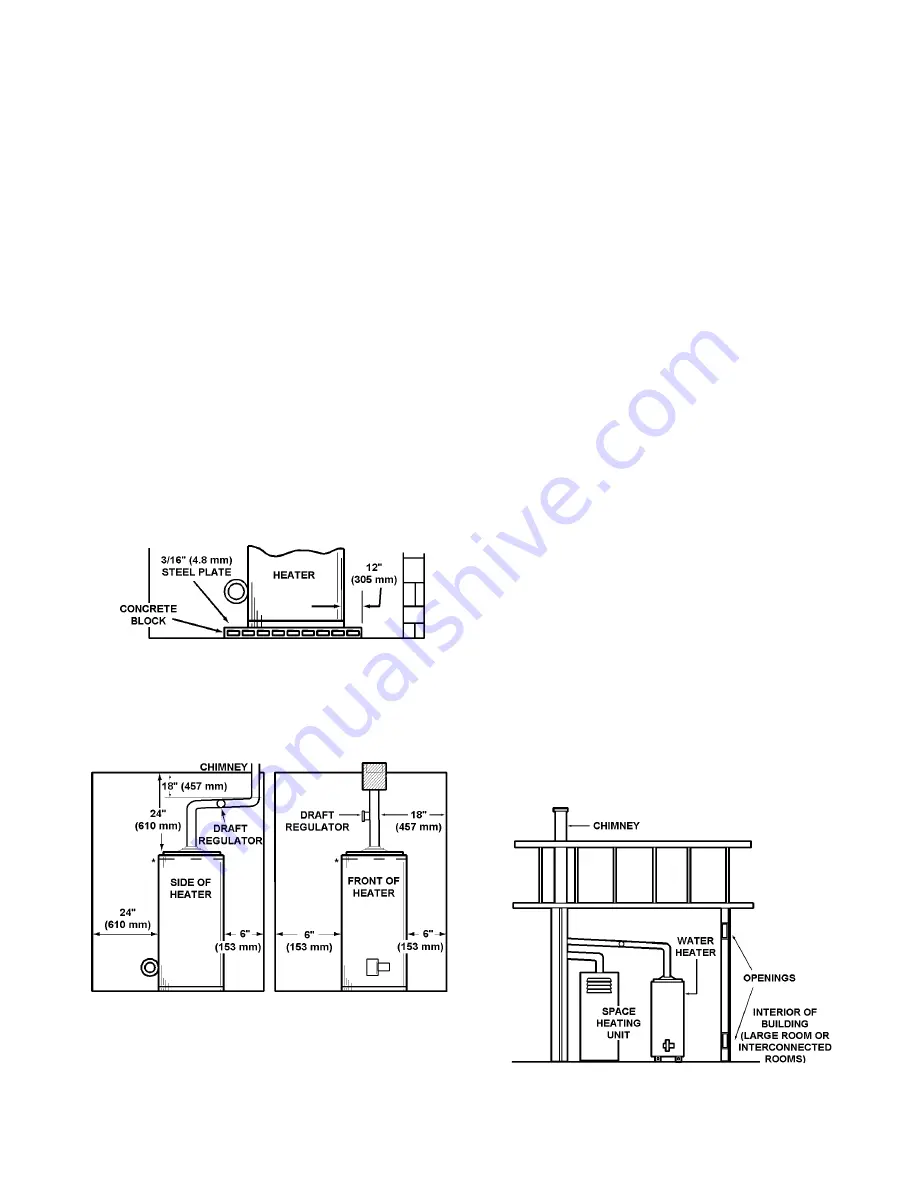
5
•
The discharge opening of the relief valve should always be piped
to an open drain.
•
Choose the point of major hot water usage, fuel supply and chimney.
•
Try to make hot water and oil piping as short as possible.
•
Insulate hot and cold water piping where heat loss and condensation
may be a problem.
CLEARANCES
The heater has minimum clearances to combustible material, on a non-
combustible floor of: 6 inches (152 mm) from the sides and rear, 24 inches
(610 mm) from the front, and 18 inches (457 mm) from the vent connector.
These clearances are, as shown in fig. 3A to prevent possible fire hazard
conditions.
At least 24" (610 mm) of top clearances are recommended for vertical
vent installation.
Allow sufficient room at rear of heater for servicing of T&P relief valve.
At least 24" (610 mm) should be provided at the front of the unit for
proper servicing.
Units which are to be installed on combustible flooring must be supported
by a full layer of hollow concrete blocks, fig. 3, from 8" (203 mm) to 12"
(305 mm) thick and extending 12" (305 mm) minimum beyond the heater
in all directions. The concrete blocks must provide an unbroken concrete
surface under the heater, with the hollows running continuous and
horizontally. A 3/16" (4.8 mm) steel plate must cover the concrete blocks,
see fig. 3.
PROPER INSTALLATION ON COMBUSTIBLE FLOORING
FIGURE 3
NOTE:
If electrical conduits run under the floor of the proposed heater
location, insulate the floor as recommended above.
PROPER INSTALLATION CLEARANCES FOR TWO DIFFERENT
VENTING SYSTEMS
FIGURE 3A
*
HOT WATER OUTLET LOCATION AT FRONT OF HEATER
•
FACTORY FURNISHED HEATER MANIFOLD KITS (OPTIONAL)
ARE DESIGNED FOR 10" (254 mm) SPACING BETWEEN SIDES
OF ADJACENT UNITS.
COMBUSTION AND VENTILATION AIR
GENERAL
The water heater area should have sufficient air for satisfactory combustion
of oil, and proper venting and of safe ambient temperature.
When a heater is installed in an area where exhaust or ventilating fans
may create unsatisfactory combustion or venting, approved provisions
must be made to overcome the problem, see NFPA Standard No. 31,
Chapter 1.
CHEMICAL VAPOR CORROSION
Water heater corrosion and component failure can be caused by the
heating and breakdown of airborne chemical vapors. Spray can
propellants, cleaning solvents, refrigerator and air conditioning refrigerants,
swimming pool chemicals, calcium and sodium chlorides, waxes, and
process chemicals are typical compounds which are potentially corrosive.
These materials are corrosive at very low concentration levels with little
or no odor to reveal their presence.
Products of this sort should not be stored near the heater. Also, air which
is brought in contact with the water heater should not contain any of
these chemicals. If necessary, uncontaminated air should be obtained
from remote or outside sources.
UNCONFINED SPACES (Building Construction)
NOTE: An unconfined space is defined as a space whose volume is not
less than 50 ft
3
per 1000 BTUH (4.83m
3
per kW) of total input of
all fuel burningappliances installed in that space. The unconfined
space may be thought of as extending to all areas which cannot
be separated by a door or door(s). All other spaces not fitting this
description, should be thought of as confined space.
1. In unconfined spaces in buildings of conventional frame, brick or stone
construction, infiltration will normally supply an adequate amount of
air for combustion and ventilation.
2. If the unconfined space is within a building of tight construction, eg.
weather stripping, heavy insulation, caulking, vapor barrier, ect., air
infiltration may be insufficient to support proper combustion and
ventilation, air shall be obtained from outdoors or from spaces freely
communicating with the outdoors.
•
Follow the instructions under Part 2 of Confined Spaces (Room
Construction)
CONFINED SPACES (Room Construction)
1. All air from inside building (conventionally constructed buildings only):
The confined space shall be provided with the two permanent openings,
one within 12" (305 mm) of the ceiling and one within 12" (305 mm) of
the floor, fig. 4.
REQUIRED AERATION FOR APPLIANCE INSTALLATION
IN A CONFINED SPACE WITHIN A CONVENTIONALLY
CONSTRUCTED BUILDING
FIGURE 4