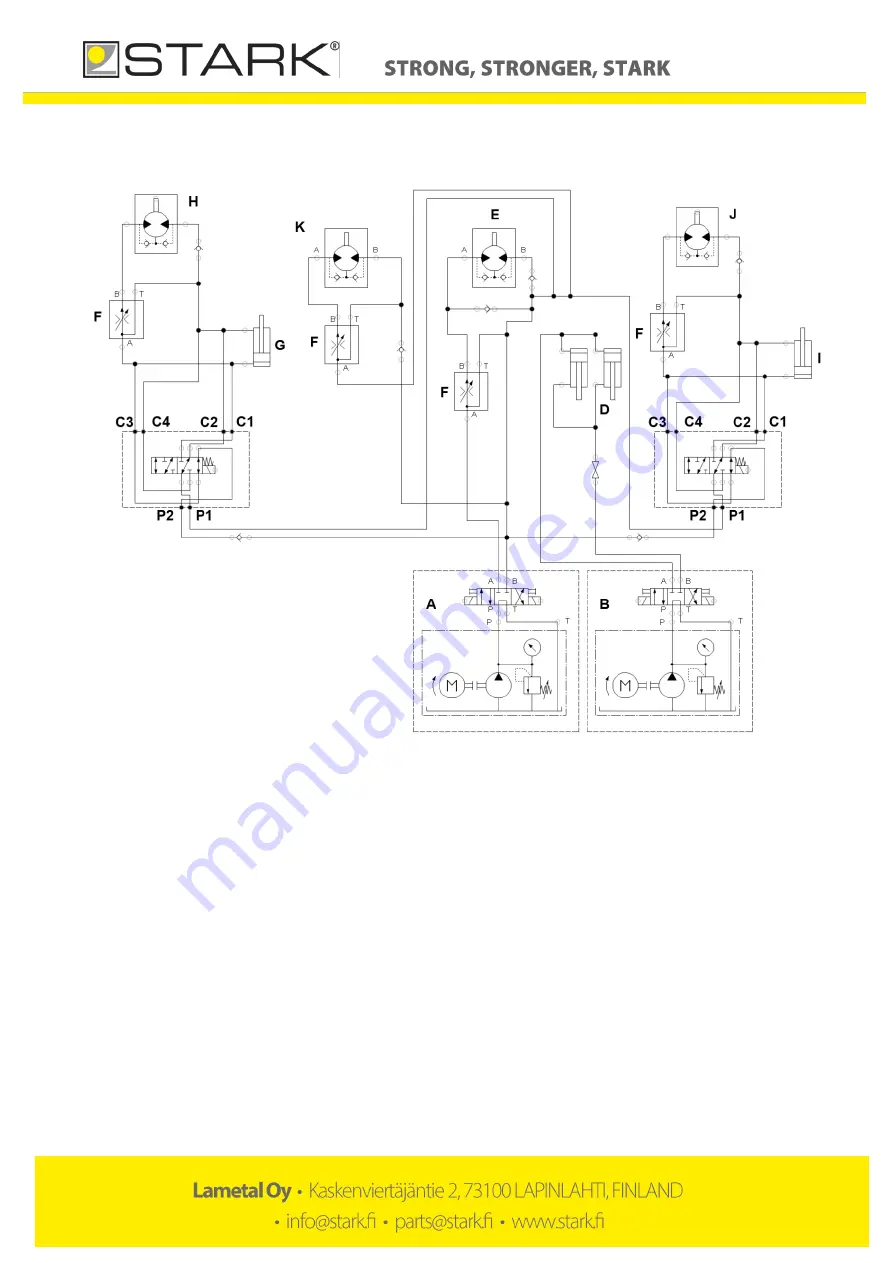
Sivu 22 / 23
9.7.
4-hose hydraulics with two side brushes and high-pressure
washer
Figure 7. 4-hose hydraulics with two side brushes
A
–
Base machine control block
B
–
Base machine control block 2
C
–
Brush frame lift cylinders
D
–
Brush roller motor
E
–
Flow control valve
G
–
Left side brush, brush lift cylinder
H
–
Left side brush, brush rotation motor
I
–
Right side brush, brush lift cylinder
J
–
Right side brush, brush rotation motor
K
–
High pressure pump