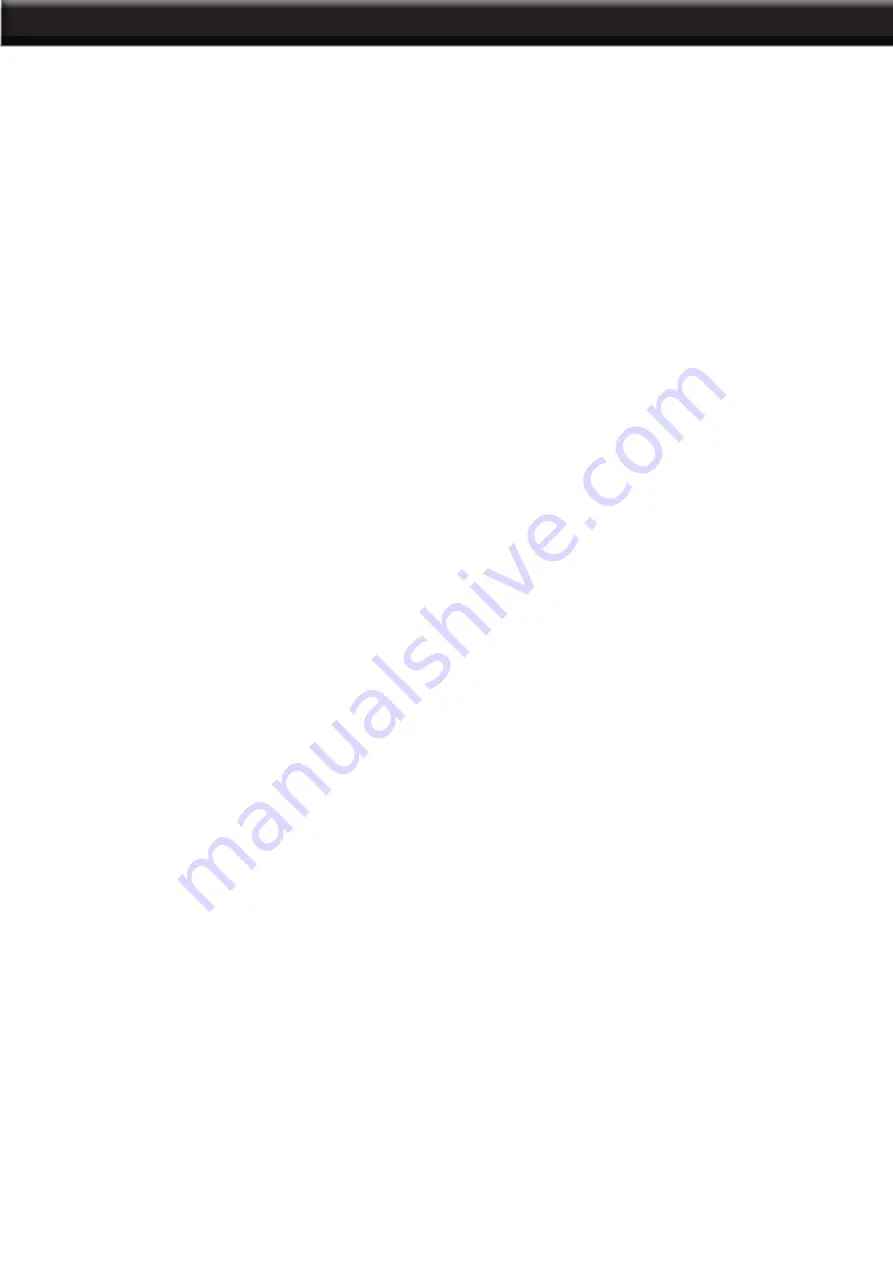
8
The tool is nearly always used to make finished cute, to cut vees and beads and to square shoulders.
It produces the best finish that can be obtained without a chisel. To avoid dulling, it should be used very
little for scraping. For finish cutting, the skew is held with the cutting edge considerably in advance of the
handle, bevel side down. Keeping the skew well over the work, pull it back until the edge begins to cut,
then swing the handle into position to advance the cut. Both the toe and heel of the skew can be used for
taking light cuts. To avoid burning the tip of the tool, do not penetrate the wood too deeply without cutting
clearances.
USING A SKEW
A shoulder can be the side of a square portion left in the work piece, the side of a turned section, or the
end of the work piece. Most shoulders are perpendicular to the work axis but a shoulder can be at any
angle.
CUTTING A SHOULDER
First, mark the position of the shoulder with a pencil held to the revolving work piece. Then make sizing
cut via the parting tool, placing the cut about 1/16” outside the shoulder position. Cut to within 1/8” of the
depth desired for the area outside the shoulder position. Cut to within 1/8” of the depth desired for the area
outside the shoulder. If the shoulder is shallow, the toe of the skew can be used to make a sizing cut. Do
not go in than 1/8” with the skew unless wider vees are cut to provide clearance for the tool.
Use the gouge to remove any waste stock outside of the shoulder. Smooth the section up to within 1/8”
of the shoulder unless it is more than 1” high, it is best done with the 1/2” skew. First, use the toe of the
skew to remove the shavings from the side of the shoulder down to the finished size. Hold the skew so
the bottom edge of the bevel next to the shoulder will be nearly parallel to the side of the shoulder. Make
sure this is with the cutting edge turned away at the top so that only the extreme toe will do the cutting.
If the cutting edge is flat against the shoulder the chisel will run. Start with the handle low and then raise
it to advance the toe into the work. Cut down to finished diameter of the outside area, then clean out the
corner by advancing the heel of the skew into along the surface the outside area. Tilt the cutting edge with
the handle raised up so that only the extreme heel does the cutting if the shoulder is at the end of the work
called “squaring the end”. In this case, reduce the outer portion to a diameter about 1/4” larger than the
tool center diameter, saw off the waste stock later.
Use a pencil mark to indicate edges, then rough it out to within about 1/8” of the desired finish surface
by scraping with the gouge or round nose chisel. If the cove is to wide, sizing cuts can be made to plot
the roughing out. Once it is roughed out, the cove can be finished in two cuts; one from each side to the
bottom center.
CUTTING COVES
At the start of either cut, gouge is held with the handle high and the two sides of the blade held between
the thumb and forefinger of the tool rest handle, just above the bevel. Position the fingers ready to roll the
blade into the cove. Hold the blade so that the bevel is at a 90 degree angle to the work axis, with the point
touching the pencil line and pointed into work axis.
From this start, depress the point slightly to start the cut, then continue to move the point down in an arc
toward the bottom center cove. At the same time, roll the chisel uniformly so that at the end of the cut, it
will be flat at the bottom of the cove. The object is to keep the extreme point of the gouge doing the cutting
from start to finish. Reverse movements to cut the opposite side.
OPERATION AND ADJUSTMENTS
Summary of Contents for 66012
Page 11: ...10 TROUBLESHOOTING ...
Page 13: ...12 PARTS DIAGRAM ...