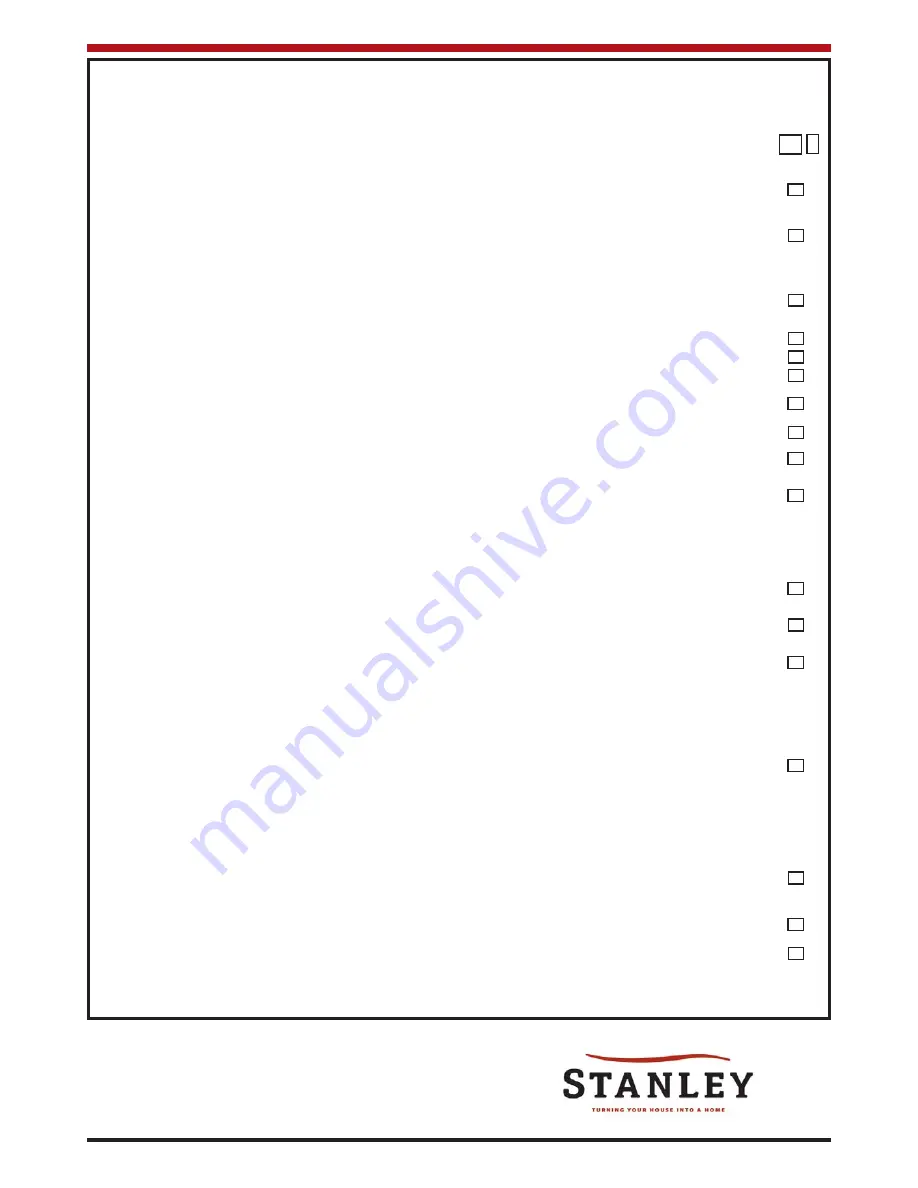
Rev: 004 DP 070129
INSTALLATION CHECK LIST
Flue System
1.
The flue height should not be less than 3 metres and no more than 11 metres.
2.
If connecting to an existing chimney, the appliance should be connected to a 125mm (5”)
diameter continuous, rigid or flexible flue pipe that terminates in excess of 0.6 metres from
the nearest point on the roof measured vertically, and in excess of 2.3 metres measured
horizontally.
3.
If using an external flue, the appliance should be connected to a 125mm (5”) diameter rigid
insulated flue pipe that terminates in excess of 0.6 metres from the nearest point on the
roof measured vertically and in excess of 2.3 metres measured horizontally.
4.
Any horizontal flue sections should not exceed 300mm (12”).
5.
The chimney serving this appliance should not serve any other appliance.
6.
A suitable flue terminal should be fitted at the flue termination point.
7.
If using an internal flue or chimney, closure-clamping plates should be used to seal the top
& bottom of the chimney.
8.
Access should be provided to the chimney serving the appliance to allow for cleaning.
9.
If the flue passes through a combustible wall, a twin wall insulated connector must be used
and come flush to the external surface of the wall.
10. The flue should be capable of producing a continuous draught of between 0.06” w.g. during
normal operation.
Location
1.
Clearance to combustible materials must be adhered to as described in the Clearance to
Combustibles section.
2.
The stove should be installed as to allow adequate air circulation around the stove and to
allow access for installation & servicing.
3.
The stove must be installed on a non-combustible insulated floor protector that covers the
area of 1007mm x 470mm around and under the stove.
Ventilation & Combustion Air Requirements
1.
The room in which the appliance is located should have an air vent of adequate size to
support correct combustion, including all other air using devices fitted in the same or
adjacent rooms. (see Ventilation & Combustion Air Requirement Section for specific details).
Gas Supply
1.
A 8mm rigid gas supply pipe must be used to connect directly from the gas meter to the stove.
In the event of a number of appliances using the same supply pipe, the pipe size may need
to be increased.
2.
A shut off valve must be used to connect the gas supply as close as possible to the stove and
should be accessible at all times.
3.
A soundness test must be conducted to check all joints for gas tightness.
Tick
√
15
Manufactured by
Waterford Stanley Ltd.,
Unit 210, IDA Industrial Estate, Cork Road,
Waterford, Ireland.
Tel: (051) 302300 Fax (051) 302315
Summary of Contents for MAEVE
Page 11: ...A B Medium 1007 470 A 225mm B 150mm A 50mm B 150mm 10 DIAGRAMS Fig 7 Fig 8 Fig 9 ...
Page 12: ...11 Fig 10 Fig 11 Fig 12 Fig 13 Fig 15 Fig 14 COAL LAYOUT ...
Page 13: ...12 Fig 16 Fig 17 Fig 18 ...
Page 14: ...13 Fig 19 Fig 21 Fig 20 ...