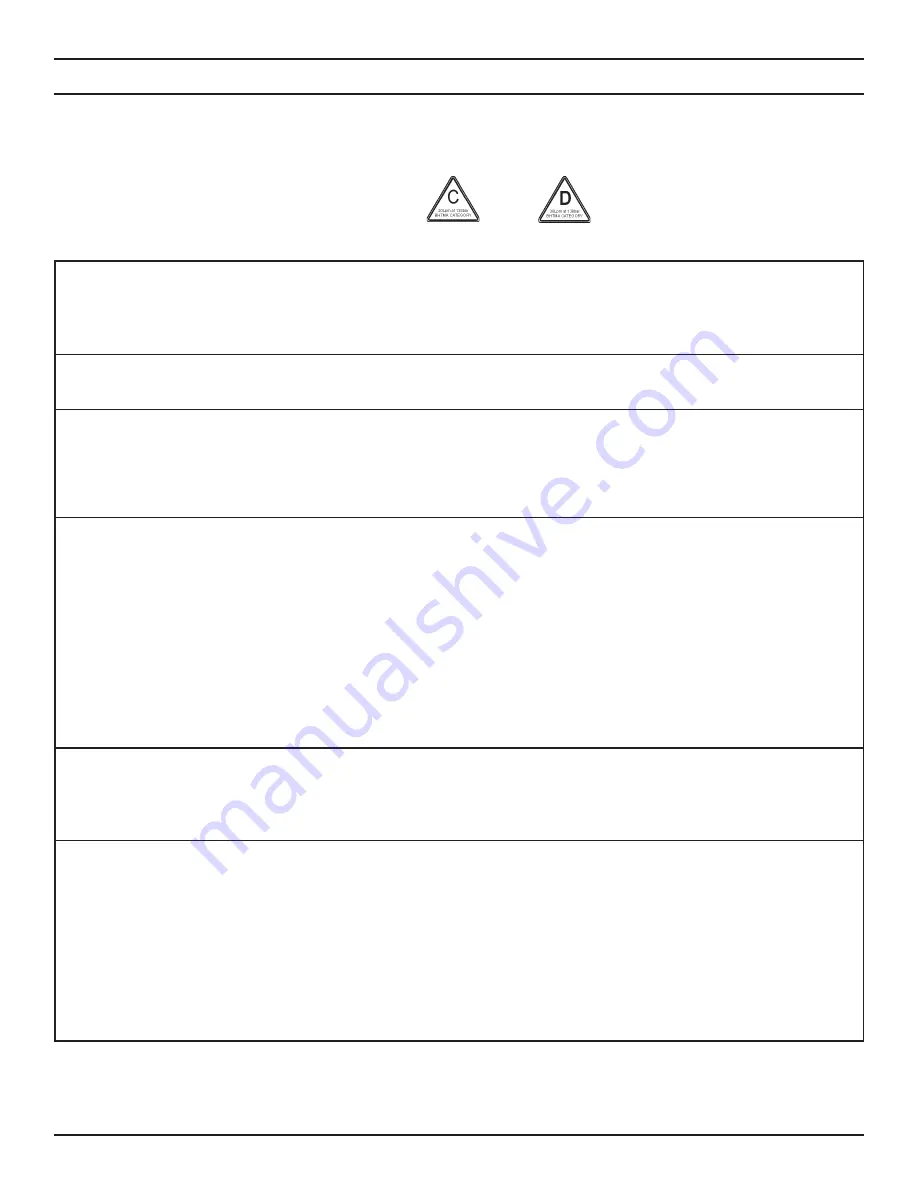
9
HTMA REQUIREMENTS
FLOW RATE
TOOL OPERATING PRESSURE
(at the power supply outlet)
SYSTEM RELIEF VALVE SETTING
(at the power supply outlet)
MAXIMUM BACK PRESSURE
(at tool end of the return hose)
Measured at a max. fl uid viscosity of:
(at min. operating temperature)
TEMPERATURE
Suffi cient heat rejection capacity
to limit max. fl uid temperature to:
(at max. expected ambient temperature)
Min. cooling capacity
at a temperature difference of
between ambient and fl uid temps
NOTE:
Do not operate the tool at oil temperatures above 140° F (60° C). Operation at higher temperatures can cause operator
discomfort at the tool.
FILTER
Min. full-fl ow fi ltration
Sized for fl ow of at least:
(For cold temp. startup and max. dirt-holding capacity)
HYDRAULIC FLUID
Petroleum based
(premium grade, anti-wear, non-conductive)
VISCOSITY
(at min. and max. operating temps)
NOTE:
When choosing hydraulic fl uid, the expected oil temperature extremes that will be experienced in service determine the
most suitable temperature viscosity characteristics. Hydraulic fl uids with a viscosity index over 140 will meet the require-
ments over a wide range of operating temperatures.
*SSU = Saybolt Seconds Universal
4-6 gpm
7-9 gpm
11-13 gpm
9-10.5 gpm
(15-23 lpm)
(26-34 lpm)
(42-49 lpm)
(34-40 lpm)
2000 psi
2000 psi
2000 psi
2000 psi
(138 bar)
(138 bar)
(138 bar)
(138 bar)
2100-2250 psi 2100-2250 psi 2100-2250 psi 2200-2300 psi
(145-155 bar) (145-155 bar) (145-155 bar) (152-159 bar)
250 psi
250 psi
250 psi
250 psi
(17 bar)
(17 bar)
(17 bar)
(17 bar)
400 ssu*
400 ssu*
400 ssu*
400 ssu*
(82 centistokes) (82 centistokes) (82 centistokes) (82 centistokes)
140° F
140° F
140° F
140° F
(60° C)
(60° C)
(60° C)
(60° C)
3 hp
5 hp
7 hp
6 hp
(2.24 kW)
(3.73 kW)
(4.47 kW)
(5.22 kW)
40° F
40° F
40° F
40° F
(22° C)
(22° C)
(22° C)
(22° C)
25 microns
25 microns
25 microns
25 microns
30 gpm
30 gpm
30 gpm
30 gpm
(114 lpm)
(114 lpm)
(114 lpm)
(114 lpm)
100-400 ssu*
100-400 ssu*
100-400 ssu*
100-400 ssu*
(20-82 centistokes)
TOOL CATEGORY
HYDRAULIC SYSTEM
REQUIREMENTS TYPE I TYPEII TYPEIII TYPE RR
NOTE:
These are general hydraulic system requirements. See tool Specifi cation page for tool specifi c requirements.