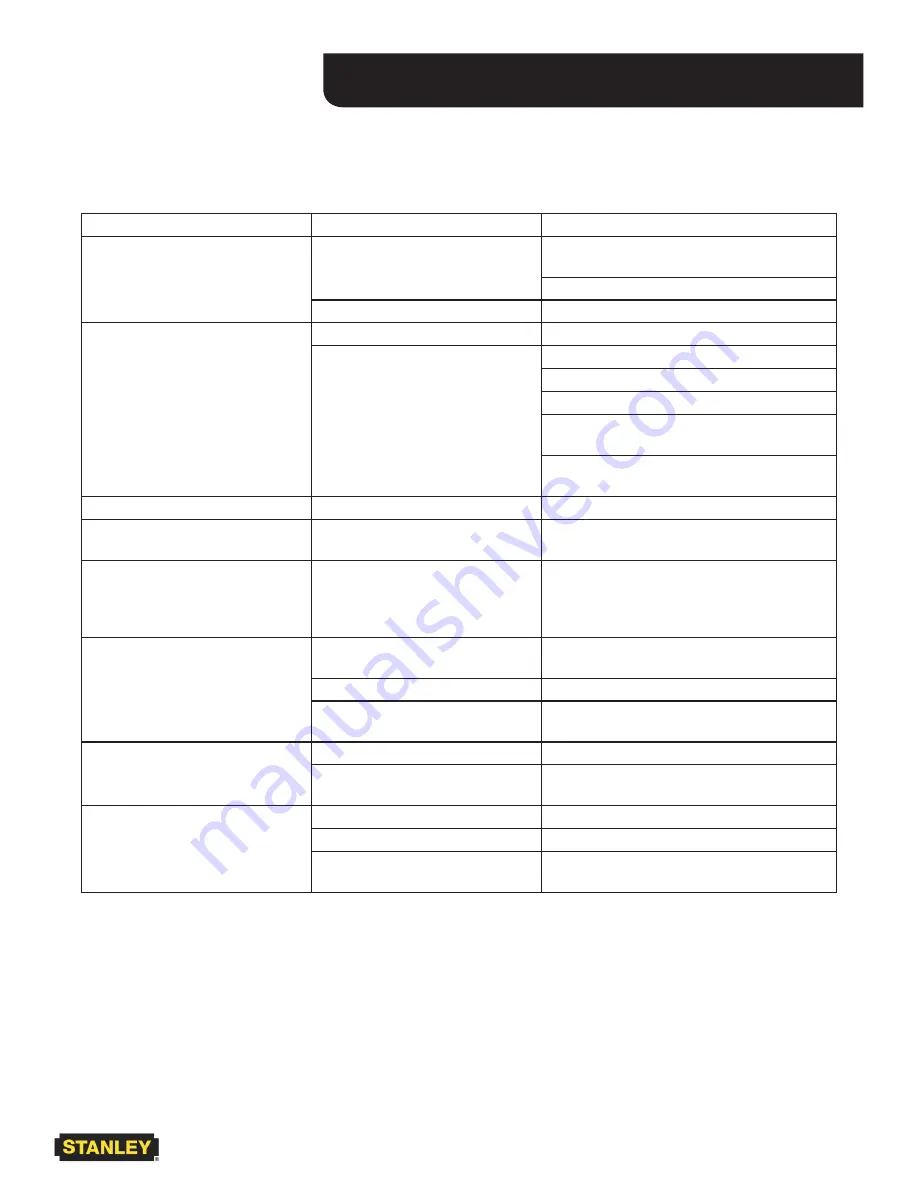
DL07 User Manual ◄ 13
TROUBLESHOOTING
If symptoms of poor performance develop, the following chart can be used as a guide to correct the problem. When
diagnosing faults in operation of the wrench, always check that the hydraulic power source is supplying the correct
hydraulic flow and pressure to the tool as listed in the following table. Use a flow meter known to be accurate. Check
the flow with the hydraulic fluid temperature at least 80 °F/27 °C.
PROBLEM
CAUSE
SOLUTION
Tool will not start.
Power not being supplied.
Check to make certain that both hoses are
connected.
Turn hydraulic circuit control valve ON.
Defective quick disconnects.
Check each quick disconnect.
Low drilling torque.
Relief valve set too low.
Set relief valve at 2100 psi/145 bar.
Fluid restriction in hose or valve.
Excess flow and pressure loss.
Locate and remove restriction.
Use correct fluid.
Fluid not warmed up. Preheat system.
Hoses too long for hose ID. Use shorter
hose.
Hose ID too small for hose length. Use
larger ID hose.
Low tool speed.
Fluid flow rate is too low.
Check circuit flow rate.
High tool speed.
Fluid flow rate is excessive.
Check circuit flow rate. Add proper flow
control valve or reduce the pump RPM.
Oil leaks around gear housing.
Hydraulic pressure and return
hoses reversed.
Correct hose connections. Pressure should
be to the handle port away from the trigger,
return is near the trigger, then replace the
main shaft oil seal.
Oil gets hot, power unit working
hard.
Open-center tool on a closed-
center circuit or vice-versa.
Use tools to match circuit.
Circuit relief set too low.
Adjust relief valve to 2100 psi/145 bar.
Too much oil going through tool.
Adjust flow for 12 gpm/45 lpm maximum or
less.
Oil leaks at reversing spool.
Damaged O-rings.
Replace as required.
Wrong hydraulic fluid. Circuit too
hot.
Refer to Operation section for correct fluid/
circuit specifications.
Oil leak at motor cap face.
Fasteners loose.
Refer to Service Manual.
Face O-ring worn or missing.
Replace as required.
Motor cap/main housing dam-
aged.
Replace as required.