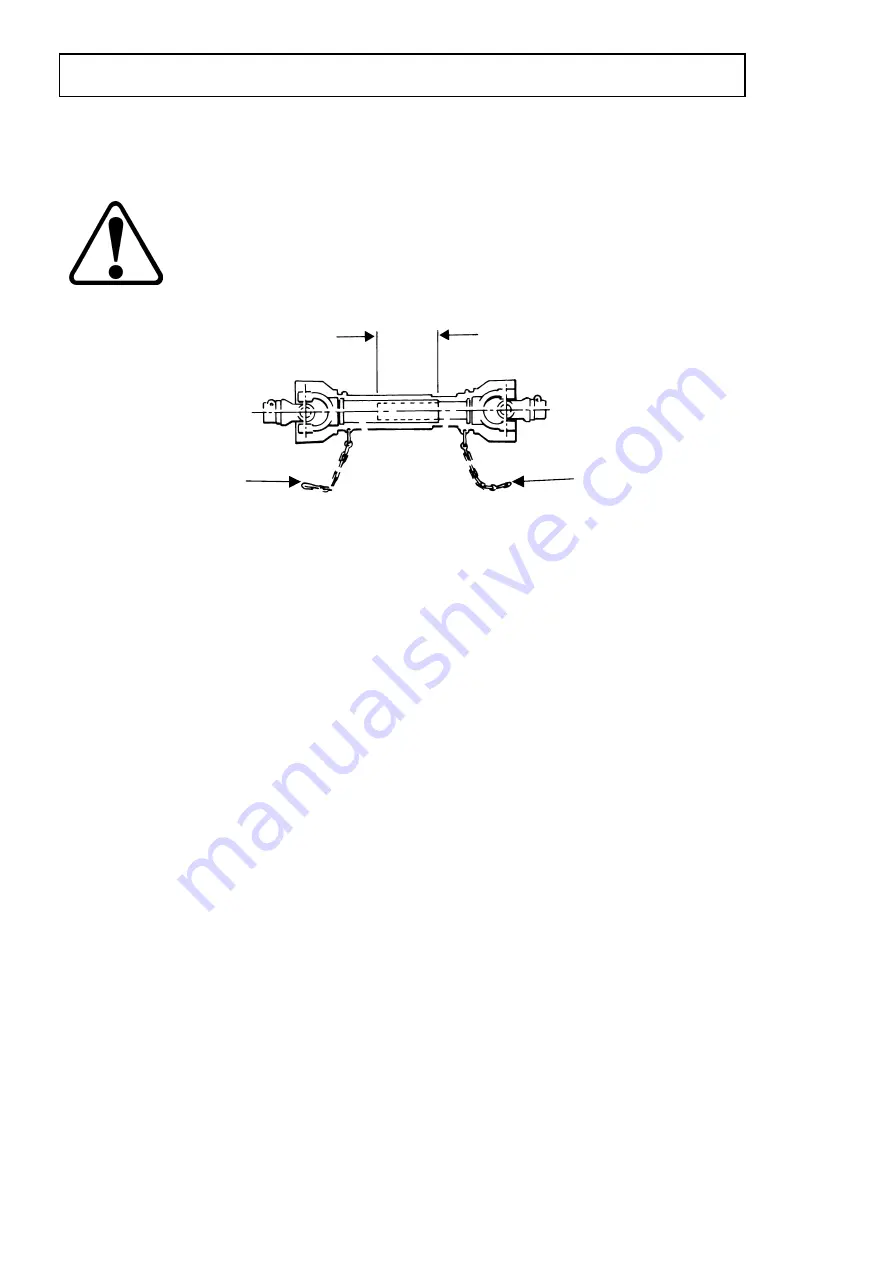
minimum1/2 overlap
PTO Shaft
The machine is designed to operate with the tractors 540 rpm, 6 spline, 1 3/8” PTO
output shaft.
PTO speeds greater than 540 rpm will cause damage to the system
and if exceeded may invalidate the warranty.
Fit the two halves of the PTO shaft onto their respective drive shafts on the machine
and tractor. Check the shaft length by turning the tractor fully in both directions with
the machine in its working position while attached to the tractor’s pick-up hitch.
Ensure the sliding tubes, when fully extended, have an overlap at least half the
closed length (see figure 3). Ensure that the ends of the sliding tubes when at the
shortest point are not in contact with other parts of the PTO shaft. If necessary,
shorten both tubes and guards equally to achieve end clearance at the minimum
length position.
Make sure that the drive shaft is fitted correctly and that the lock pins are engaged.
All the parts of the PTO shaft, especially the guards, must be kept in good order.
Check regularly that the guard is undamaged and fully protects the whole of the
shaft, and that both the guard and the shaft will telescope freely.
If it is possible to engage the inner and outer parts of a drive in more than two
positions circumferentially then make sure that the universal joint yokes are correctly
aligned.
Check that when in the continuous working position, the drive shaft is not at an angle
of more than 20° from the PTO centre line. The angle between the drive shaft and
the input and output shafts should be equal.
Ensure that the safety chains (item 1, fig 3) used to prevent the guards from turning,
are fixed to the tractor and implement in such a way that they will not be stretched
when the drive shaft is at maximum articulation. When disconnected from the tractor,
position the PTO shaft on the drawbar PTO rest as shown in figure 1.
1.9
INSTALLATION
1
1
Fig 3
Summary of Contents for Unistar 2400
Page 2: ......
Page 4: ......
Page 10: ...1 5 SAFETY PRECAUTIONS ...
Page 11: ...SAFETY PRECAUTIONS 1 6 ...