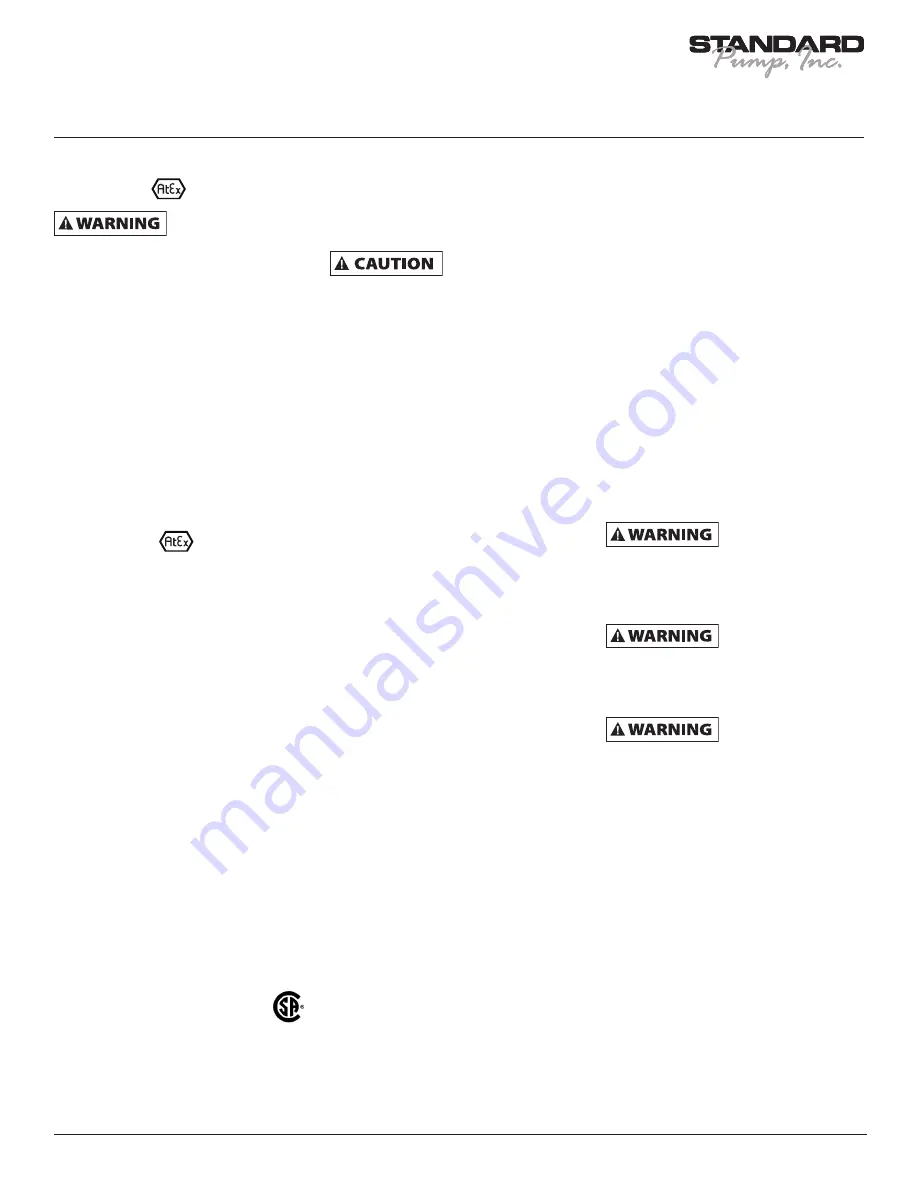
6
Standard Pump Operating Instructions and Parts Manual (
OIPM-IND-0713
)
Industrial Drum Pumps Models:
SP-PP, SP-PHT, SP-CPVC, SP-AL, SP-PVDF & SP-SS
Hazardous Duty
Operation
When pumping
flammable or
combustible products or operating in a
hazardous duty environment, the
SP-8600, SP-8700, SP-8800, SP-8900,
SP-AL or SP-SS Series pump must be
used in conjunction with an explosion
proof motor. Please contact the factory
or an authorized distributor with any
questions regarding this matter.
SP-420 EX & SP-A1 Series
When operating in Hazardous Duty
applications SP-420EX or SP-A1 must
be used in conjunction with an SP-SS,
SP-AL, SP-8600 or SP-8800 Series pump
and properly bonded and grounded. Refer
to the Motor specification chart for motor
information.
Special Conditions for
Safety Use
•
Only for conductive liquids (gases groups IIA
and IIB).
•
The flashpoint for the flammable media
shall be 50°C higher than the maximum
temperature T4 (135°C).
•
The SP-AL versions may not be used in an
area where rusty particles or rusty iron is
present.
•
The tube shall regular be inspected for
damage and corrosions. If there is any
damage or corrosions the equipment and the
tube shall be taken out of service.
•
The grounding clamp and wire on the pump
shall be connected to the liquid container
before and after pump start.
•
The pumps must not be exposed to pumping
hard solid particles which can create sparks.
•
Demands for inspections, maintenance and
repair according to the instructions.
•
The pump is only for hand held operation and
may not be running dry.
•
The SP-AL version may only be used with
the PTFE impeller parts no. 2706 and
4608HH.
Drum Pump Installation
SP-410EX
•
Install the Pump and Static Protection Kit as
described in Figure 2 on page 7.
•
Connect Ground Wire assembly to earth
ground using supplied clamp.
•
Connect Ground Wire between drum and
earth ground.
•
Connect Ground Wire between receiving
container and earth ground (or use bonding
wire to connect to drum).
Check electrical
continuity of all
components before pumping. All should
be one (1) ohm or less.
Operation and Safety
Guidelines
•
Use only metallic pump tubes with
explosion proof motors to transfer
flammable or combustible liquids.
•
Area for use must comply with NFPA 30
guidelines for safe storage and use of
flammable and combustible liquids.
•
All containers and other equipment must be
metal and grounded.
•
Follow NGPA 77 guidelines for control of
static electricity.
•
Avoid splashing. Splash filling can create
static electricity and is extremely hazardous.
•
Fluid velocity must be 3 feet/second (0.91
meters/second) maximum 7 GPM in 1"
hose (26.5 LPM in 25 mm hose).
Use Of Air Motors In
Hazardous Atmospheres
SP-A1 Series & SP-A2 Series
At the present time, there are no known
standards governing the operation of air
motors in hazardous atmospheres. However,
there are several points regarding the safety
of air motors.
First of all, an air motor is not a source of
electric sparks. However, it is possible that
an article which is not part of the air motor
(e.g., wrenches, hammers, etc.) could create
a spark by sharply impacting a cast iron or
aluminum case or the steel shaft of the air
motor. (Note that electric motor enclosures
for both class I and II hazardous locations
can be made of “...iron, steel, copper, bronze,
or aluminum..." (UL 674, Electric Motors and
Generators – Hazardous Locations, June 23,
1989; paragraph 4.2, page 6).Second, an air
motor housing is not designed to contain an
internal explosion as is an explosion-proof
electric motor. The only possible internal
source of ignition in an air motor is a contact
between the station housing components
and the rotating elements that might create
a spark. The likelihood of this occurring is
reduced by the fact that the contact must
be made at precisely the same time as a
flammable or explosive gas is introduced
into the air motor in a sufficient quantity to
achieve a flammable or explosive mixture
while overcoming the positive pressure of
the driving gas. In other words, although
highly improbable, an internal explosion in an
air motor is possible. Finally, an air motor is
designed to be operated by compressed air,
the expansion of which in normal operation
creates a cooling effect. As a result, the
temperature of the air motor will not exceed
the height of the temperatures of the
surrounding atmosphere or the air delivered
to the inlet.
We do not guarantee the safety of every
application, but to ensure the safe operation
of an air motor in your application, always
follow the product direction and consult
with a qualified engineer. (Source: Gast
Manufacturing, Air Motors Handbook, page
2) Note: This statement is only applicable in
North America.
When using an SP-A1
or SP-A2 Series motor,
Standard Pump recommends the use of a
Filter Lubricator Regulator (FLR) in order
to ensure a moisture free supply of air to
the motor.
SP-A1 and SP-A2
Series motors must be
lubricated daily to ensure proper
functionality
Grounding Procedures
Transferring of
flammables or use in
hazardous duty. Bonding is an electrical
connection between a primary metal vessel
and a metal receiving vessel. See schematic.
Grounding is an electrical connection
between a metal vessel, pump, motor and a
constant ground; i.e. a metal rod driven into
the earth.
Bonding and grounding are required when
pumping flammable materials or in hazardous
duty environments. Failure to bond and
ground properly can cause a discharge of
static electricity resulting in fire, injury or
death. Follow NFPA 77 and 30 procedures
at all times. If in doubt, do not start pump!
Be sure bonding and grounding wires are
secure before starting operation. (Ground
and bond wires must have less than one ohm
resistance for safe usage. Check continuity
before starting). Always check with a safety
engineer when any question arises and
periodically check safety procedures with a
safety engineer (see Figure 2, page 7).