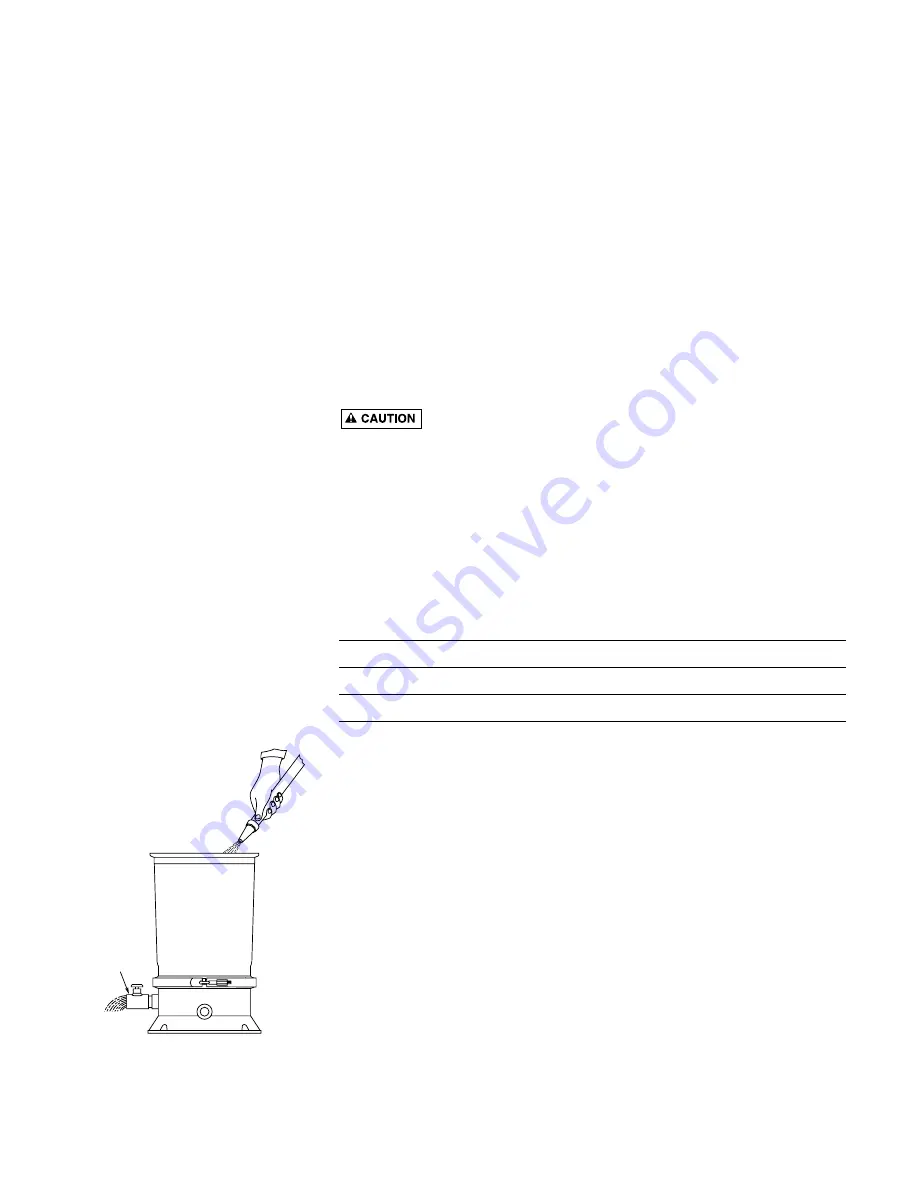
12
FILTER ASSEMBLY
1. Replace plugs or close valves in Tank Drain and Auxiliary Drain ports.
2. Push clean air bleed filter all the way down on tube. If tube has been re-
moved, push it into socket seat in base until it bottoms.
3. Set filter element on base.
NOTICE:
Be sure blue end marked “TOP” is on top and orange end is on
bottom. Do not reverse element.
4. Push filter element into base between two circular ribs until it bottoms.
5. BE SURE “O” Ring sealing area of tank body is clean. Clean “O” Ring and
check for damage. Replace if necessary.
6. Lubricate “O” Ring with approved lubricant (see chart) and place in seat.
NOTICE:
Top and bottom clamps and “O” Rings are not interchangeable;
DO NOT mix them up.
Do not remove or damage safety and instruction labels during
cleaning. Replace any decals which may have been damaged.
7. If bottom clamp was removed, BE SURE bottom of tank body is clean; set
tank body evenly on base and “O” Ring.
8. Install clamp(s) and knob assembly(s); tighten knob(s). To assist sealing,
tap clamp(s) around tank with hammer while tightening knob(s).
9. Clean pump strainer basket.
10. Open system valves as needed.
11. Proceed to “Startup”, Page 9.
STA-RITE APPROVED O-RING LUBRICANTS
Parker Super-O-Lube*
Semi-Permanent Lubrication
Aqua-Lube by Allube**
Semi-Permanent Lubrication
5% or less Mild Soap Solution
Assembly Lubrication
* Parker Seal Group, Lexington, KY
** Allube Div. of Far Best Corp., Los Angeles, CA
FILTER CLEANING PROCEDURE
NOTICE:
Keep track of filter operating pressure. When pressure reaches 5-7
PSI (35-48kPa) above initial operating pressure, clean filter element.
NOTICE:
If filter is used with a spa, soak element (see Step 2, “Special
Cleaning”) at each regular cleaning.
NOTICE:
When sanitizing your pool using PHMB (polyhexamethylene bi-
quanide based) cleaners, use
only
PHMB cleaners to clean the module. When
using PHMB sanitizers, the filter module MUST be cleaned more thoroughly
and frequently than for a pool using chlorine. Follow manufacturer’s instruc-
tions carefully. Use of any other type of cleansers with PHMB pool sanitizers
will void the filter’s warranty.
With hose, wash foreign material from inside of base. Try to avoid washing
debris into outlet port (see Figure 8).
NOTICE:
Be sure inside surface of base is clean.
Tank Drain
Port
815 0394
FIGURE 8