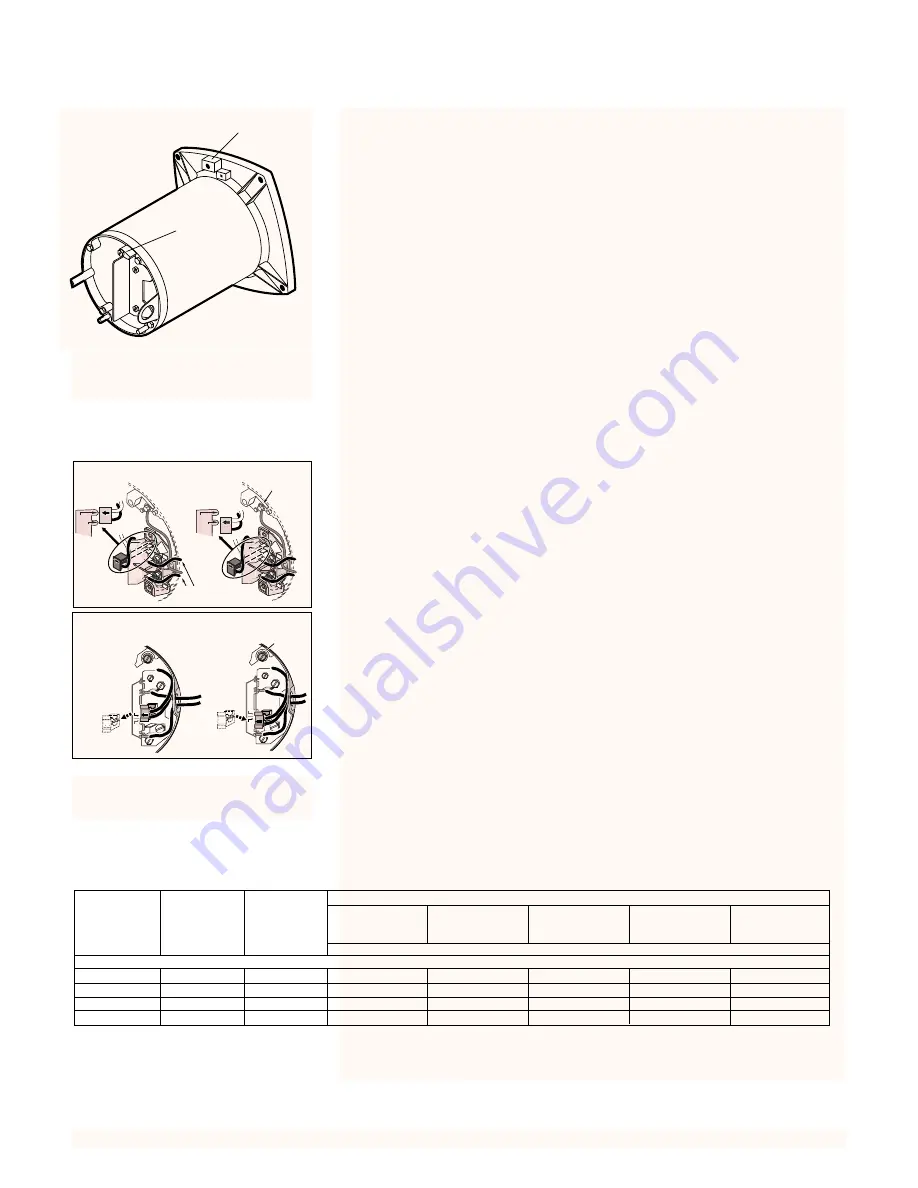
Pull plug
straight
out from
terminal
board.
1.
1.
2.
2.
Plug in again
with arrow
on plug
pointing to
'115 Volts'.
A
L1
2
3
0
V
o
lt
s
1
1
5
V
o
lt
s
A
L1
2
3
0
V
o
lt
s
1
1
5
V
o
lt
s
Ground
Screw
3962 0401 A
115 V
230 V
230 Volt to 115 Volt Conversion.
Move plug to change voltage.
Ground
Screw
23
0V
11
5V
23
0V
11
5V
A
A
L2
L2
L1
L1
23
0V
11
5V
A
A
L2
L2
L1
L1
23
0V
11
5V
Power Supply
Wires
230 Volt to 115 Volt Conversion.
Move plug to change voltage.
Figure 3 – Wiring hook-up
diagram.
6
Grounding/Bonding
Install, ground, bond and wire motor according to local or National Electrical
Code requirements.
Permanently ground motor. Use green ground terminal provided under motor
canopy or access plate (See Figure 2); use size and type wire required by
code. Connect motor ground terminal to electrical service ground.
Ground wire must be a copper conductor. It should be the same size as the
current-carrying wires to the motor, but not smaller than No. 12 AWG.
Bond motor to pool structure. Use a solid copper conductor, size No. 8 AWG
(8.4 sq. mm) or larger. Run wire from external bonding lug (see Figure 2) to
reinforcing rod or mesh.
Connect a No. 8 AWG (8.4 sq. mm) solid copper bonding wire to the pressure
wire connector provided on the motor housing and to all metal parts of the
swimming pool, spa, or hot tub and to all electrical equipment, metal piping
or conduit within 5 feet (1.5 m) of the inside walls of swimming pool, spa, or
hot tub.
Wiring
Pump must be permanently connected to circuit. See Table I, for correct wire
and circuit breaker sizes for the pump alone. If other lights or appliances are
also on the same circuit, be sure to add their amp loads to pump amp load
before figuring wire and circuit breaker sizes. (If unsure how to do this or if
this is confusing, consult a licensed electrician.) Use the load circuit breaker
as the master on-off switch.
Install a Ground Fault Circuit Interrupter (GFCI) in circuit; it will sense a short-
circuit to ground and disconnect power before it becomes dangerous to pool
users. For size of GFCI required and test procedures for GFCI, see manufac-
turer’s instruction.
In case of power outage, check GFCI for tripping (which will prevent normal
pump operation). Reset if necessary.
BONDING
LUG
GREEN
GROUND
SCREW
510 0993
Figure 2 – Typical ground screw and
bonding lug locations.
TABLE I – RECOMMENDED FUSING AND WIRING DATA - 60 CYCLE MOTORS
DIAMETER IN FEET FROM MOTOR TO METER
BRANCH
0’
101’
201’
301’
401’
MOTOR
MAX. LOAD
FUSE*
TO
TO
TO
TO
TO
HP
AMPERES
RATING
100’
200’
300’
400’
500’
AMPS
WIRE SIZE
SINGLE PHASE - 115/230 VOLT
1/2
9.9/5.0
15/15
14/14
10/14
10/14
6/14
6/12
3/4
13.4/6.7
20/15
12/14
10/14
8/14
6/12
6/12
1
15.3/7.6
20/15
12/14
8/14
6/14
6/12
4/10
1-1/2
19.2/9.6
25/15
10/14
8/14
6/12
4/10
4/10
*A Fusetron is recommended instead of a fuse in any motor circuit.