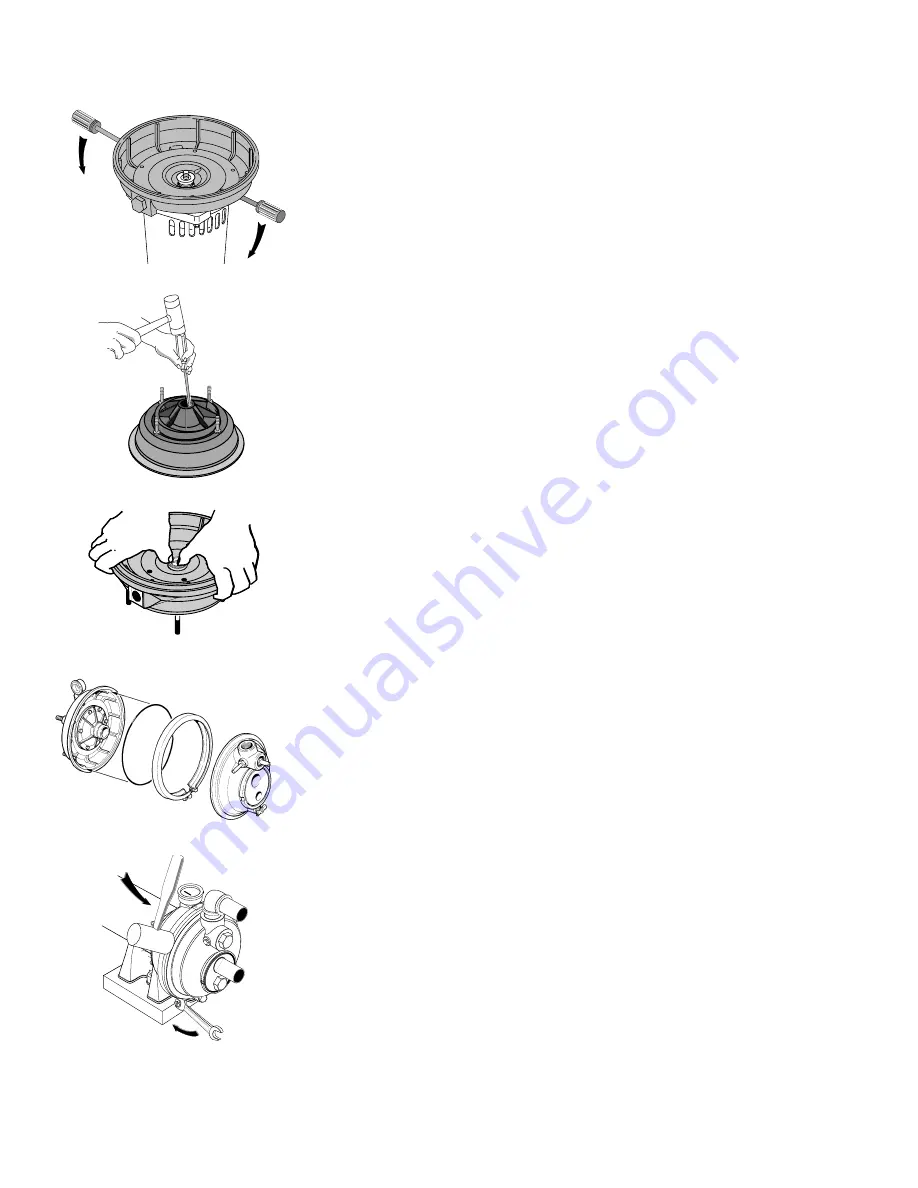
Installing New Seal/Pump Reassembly:
1. Clean seal cavity in seal plate.
2. Wet outer edge of O-Ring on ceramic seat with liquid soap. Be sparing!
3. Put cardboard washer over seal face. With thumb pressure, press ceram-
ic seal half firmly and squarely into seal cavity in seal plate (see Fig. 9).
Polished face of ceramic seat is up. If seal will not seat correctly,
remove, placing seal
face up
on bench. Reclean cavity. Seal should now
seat correctly.
4. If seal does not seat correctly after recleaning cavity, place a cardboard
washer over polished seal face and
carefully
press into place using
piece of standard 3/4” pipe as a press.
NOTICE:
Be sure you do not scratch seal face.
5. Dispose of cardboard washer and recheck seal face to be sure it is free
of dirt, foreign particles, scratches and grease.
6. Inspect shaft to be sure it is free of nicks and scratches.
7. Reassemble pump body half to motor flange.
BE SURE
it is right side up.
8. Apply liquid soap sparingly (one drop is sufficient) to inside diameter of
rotating seal member.
9. Slide rotating seal member (carbon face first) onto shaft until rubber
drive ring hits shaft shoulder.
NOTICE:
Be sure not to nick or scratch carbon face of seal when pass-
ing it over threaded shaft end or shaft shoulder. The carbon surface must
remain clean or short seal life will result.
10. Hold motor shaft with 7/16” open end wrench on shaft flats and screw
impeller onto shaft. Tightening impeller will automatically locate seal in
correct position.
11. Remount diffuser on pump body half with five screws.
Pump Reassembly:
1. Clean O-Ring and O-Ring groove.
2. Put O-Ring in groove on face of seal plate; put pump halves together
(see Figure 10).
3.
BE SURE
inside of clamp is clean. Place clamp on pump halves; snug up.
Alternately tighten screw and tap clamp with mallet to seat O-Ring (see
Figure 11).
4. Replace base mounting bolts.
5. Replace drain plug.
6. Prime pump according to instructions. See “Operation”, Page 7.
7. Check for leaks.
9
FIGURE 7
FIGURE 8
FIGURE 9
479 0194
477 0194
FIGURE 10
FIGURE 11
P
609 0395