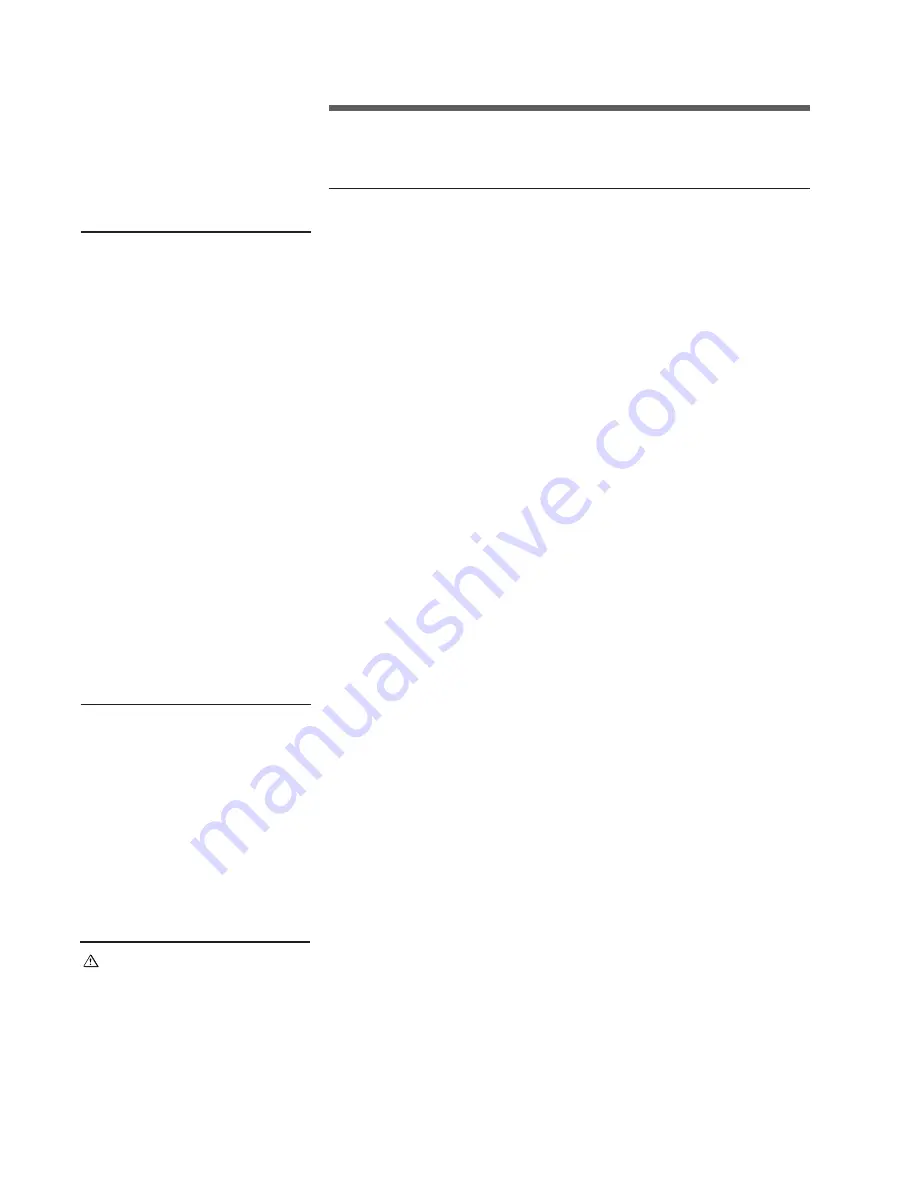
6
Installation
These installation instructions are intended to help you prepare
before your fluid cooler arrives. If discrepancies exist between these
instructions and those shipped with the fluid cooler, the instructions
shipped with the fluid cooler will govern.
1. Prior to placement of the fluid cooler, confirm that the supporting platform
is level, and that the anchor bolt holes are correctly located in accordance
with Marley drawings. If your installation uses vibration isolators to dampen
vibration, they must be mounted below the supporting steel. See support
drawings for further information.
2. Place the fluid cooler on your prepared supports, aligning anchor bolt
holes with those in your supporting steel. Make sure that the orientation
agrees with your intended piping arrangement. Attach to supporting steel
with bolts and flat washers (by others) — see support drawing for size,
location and quantity. Position flat washers between the bolt head and
the fluid cooler basin flange.
3. Attach makeup water supply piping to appropriately-sized float valve
connection. Attach the drain and overflow piping according to drawings
shipped with your fluid cooler.
Fasteners and components provided by others that are to be at-
tached to the fluid cooler must be compatible with the fluid cooler
materials — i.e. fasteners in a stainless steel cold water basin must
be stainless steel.
4. Attach the process fluid supply and return piping to the fluid cooler coil
connections. Protect adjacent areas from excessive heat and sparks or
damage may occur. Wrapping a large wet rag around piping near braze
joints is one method for limiting the conduction of heat through the piping.
Except for the horizontal components of piping, do not support your
piping from the fluid cooler inlet / outlet connections — support it
externally. Normally, one of the following connection arrangements
is provided:
Copper Soldered Connection:
The piping connections are copper pipe
stubs for field soldering/brazing.
Note
Note
Caution
installation