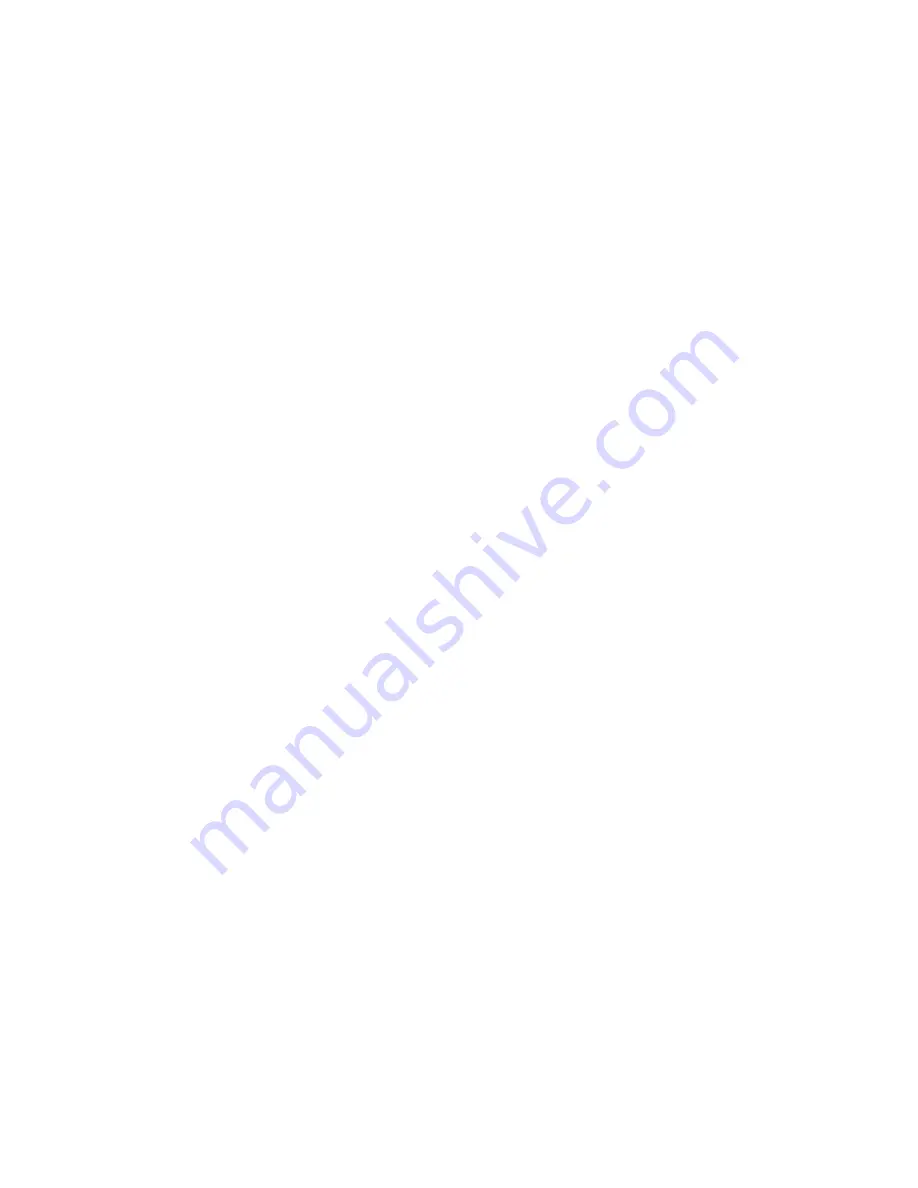
23
6.6 Start-up
6.6.1 Controller Settings
Set or verify settings on Controller. Detailed operational
points are presented in section 6.5
WARNING - Enclosure may have live electric parts.
De-energize dryer before opening enclosure.
6.6.2 Initial Pressurization
SLOWLY
pressurize dryer to full line pressure. (If the
dryer was installed with inlet and outlet isolation valves,
the inlet isolation valve should be slowly opened while
the outlet isolation valve remains closed.)
During initial start-up, check the entire system for leaks.
If necessary, de-pressurize the dryer and correct any
leaks.
6.6.2.1 Energy Management Sensor (if installed)
Open and adjust the sample exhaust valve until a very
slight, continuous gas bleed is felt exhausting out of the
sample cell.
6.6.2.2 Dew Point Sensor (if installed)
Ensure that the supply air valve is open (one turn).
Open and adjust the sample exhaust valve until a very
slight, continuous gas bleed is felt exhausting out of the
sample cell.
6.6.3 Energizing the Dryer
Energize the dryer controls.
NOTE:
The switching failure alarm may be activated if the
unit is energized before it is pressurized. To deactivate
alarm, allow dryer to cycle to next step and press the
reset button.
6.6.4 Bringing the Dryer Online
Establish a normal flow through the dryer. Slowly open
the outlet isolation valve if present. Close any dryer by-
pass valves.
6.7 Operational Check Points
6.7.1 Power to unit
Check periodically that there is power to the unit
(indicating lights illuminated).
6.7.2 Alarms
Periodically check for flashing red alarm LED.
6.7.3 Tower Status LEDs
Illuminated LEDs indicate which tower is on-line drying
or off-line regenerating.
6.7.4 Tower Pressure Gauges
Periodically check tower pressure gauges to verify
that the pressure gauge of the online tower reads line
pressure and the pressure gauge of the off-line tower
reads below 2 psig (0.14 kgf/ cm
2
).
NOTE:
Read the off-line tower pressure gauge when the
tower is purging (air exhausting from muffler).
6.7.5 Check Mufflers For Back pressure
(models 300 through 750)
Excessive back pressure may result due to the
accumulation of desiccant fines (dust) in the muffler
cartridges. This sometimes occurs after start-up due to
dusting of the desiccant during tower filling and dryer
transport. If the tower pressure gauge of the off-stream
tower rises above 1 psig, the muffler elements should
be replaced.
6.7.6 Process Valves
Determine if air control valves are operating and
sequencing correctly.
6.7.6.1 Valves – Models 300 through 600
Inlet switching valves are normally open, pneumatically
piston-actuated, Y-angle poppet valves. A yellow indicator
can be seen through a clear window at the top of the ac-
tuator housing when the valve is in the open position.
Purge exhaust valves are normally closed, pneumati-
cally piston-actuated, Y-angle poppet valves. A yellow
indicator can be seen through a clear window at the top
of the actuator housing when the valve is in the open
position.
12 volt DC, normally-closed, 3-way pilot solenoid valves
are wired to the controller and are used to direct pilot
air to the actuators of the inlet switching and purge/
repressurization valves.
Dryers are equipped with a single safety relief valve that
has been sized to provide overpressure protection due
to a fire for both desiccant towers.
6.7.6.2 Valves – Models 750 through 3200
Inlet switching valves are resilient seated butterfly valves
with double acting pneumatic rack and pinion actuators.
A yellow arrow indicator located on the top of the actuator
output shaft points to valve position indicator icons. Pilot
air is directed to actuator ports to open both inlet valves
upon loss of power.
(Model 750 only)
Purge exhaust valves are normally
closed, pneumatically piston-actuated, Y-angle poppet
valves. A yellow indicator can be seen through a clear
window at the top of the actuator housing when the valve
is in the open position.
(Models 900 through 3200)
Purge exhaust valves are
resilient seated butterfly valves with spring return, fail
closed, pneumatic rack and pinion actuators. A yel-
low arrow indicator located on the top of the actuator
output shaft points to valve position indicator icons.
Pilot air is directed to actuator ports to close both purge/
repressurization valves upon loss of power.
12 volt DC, single solenoid, 4-way pilot valves are wired
to the controller and are used to direct pilot air to the ac-
tuators of the inlet switching and purge/repressurization
valves.
Summary of Contents for HPD Series
Page 46: ......