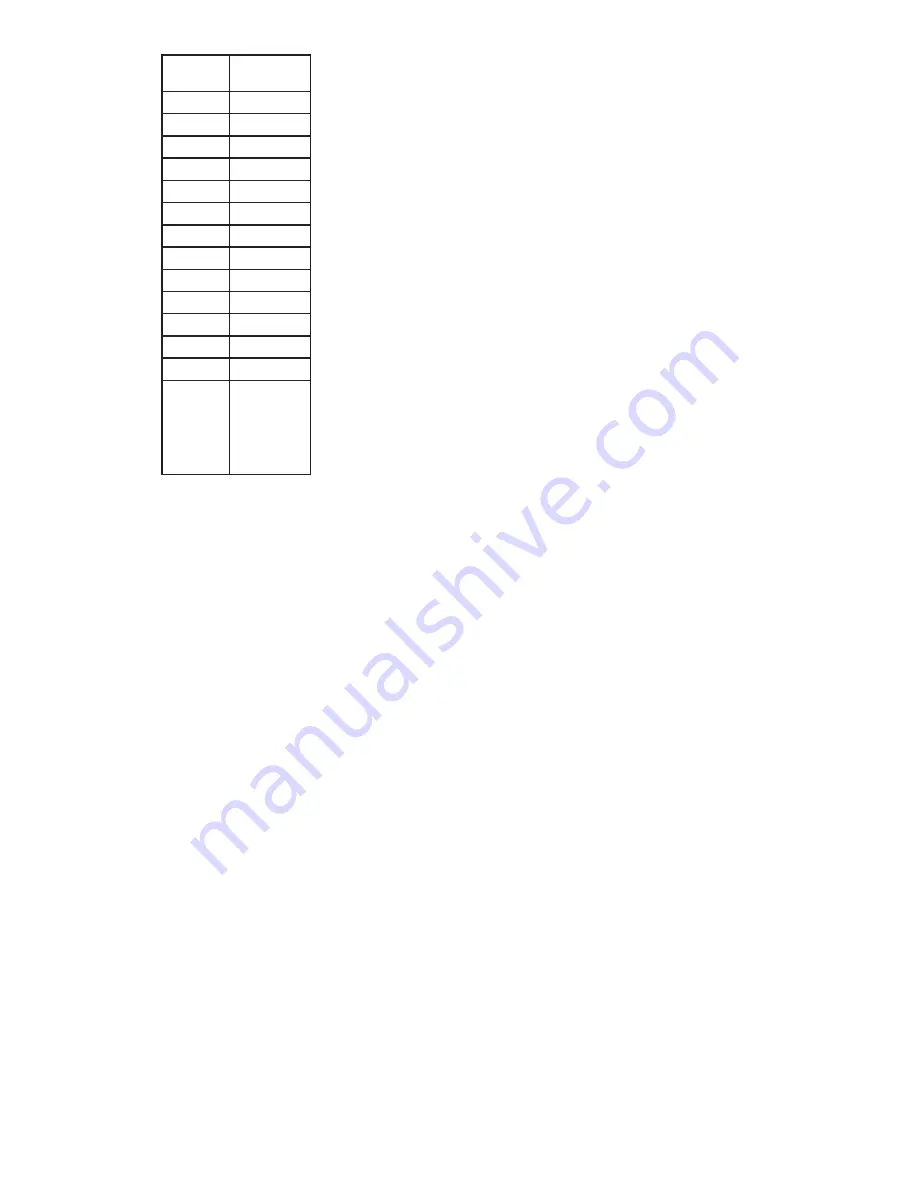
6
Model
Peak Drain
Rate
scfm
gph
350
4.0
450
5.1
600
6.8
800
9.1
1025
11.6
1300
14.7
1500
17.0
1800
20.4
2100
23.8
2400
27.2
3250
36.8
3700
41.9
4425
5000
6100
7500
8500
10000
Consult
Factory
TABLE 2
EXPECTED WATER FLOW FROM SEPARATOR
4.5 Electrical Connections
WARNING — These procedures require entering
gaining access to the dryer’s electrical enclosure(s).
All electrical work must be performed by a qualified
electrical technician.
Connect the proper power supply to the dryer according
to the electrical drawings in the back of this manual. Be
sure to follow all applicable electrical codes.
NOTE:
A disconnect switch is not provided as standard
equipment and therefore, must be supplied by the
customer.
Dry contacts (voltage free) are provided in the low tension
electrical enclosure for a remote alarm. The contact
ratings are shown on the electrical drawing.
Connections to voltage-free common alarm contacts with
a minimum 5-amp rating can be made at terminals TB4-1
through 3.
• Terminal TB4-3 is the common alarm connection.
• Terminal TB4-1 is the N.O.. (normally open) contact
connection.
• Terminal TB4-2 is the N.C. (normally closed) contact
connection.
• The alarm relay coil is energized when power is sup-
plied to the controller input terminals and there are
no alarms.
• The coil is de-energized when power is removed or
when an alarm condition exists.
• The common alarm is designed to activate on:
a) either a dryer fault condition or a service reminder,
or b) a dryer fault condition. This is user selectable.
• For the common alarm to activate on either a dryer
fault condition or a service reminder, the jumper at
JP6 is removed. This is the default configuration.
• To have the common alarm activate on a dryer fault
condition only, the jumper at JP6 is installed.
4.5.1 RS-232 Connections
RS-232 connections can be made at the 3-pin connector
labeled J3 and located at the upper left-handed corner
of the control board. A cable for this connection can be
purchased through your distributor.
4.6 Initial Desiccant Charge
Heat of Compression Air dryers use activated alumina as
the desiccant in the dryer towers.
All desiccant shipped loose must be added to the
dryer towers before the dryer is put into service.
Refer to TABLE 3, DESICCANT REQUIREMENTS for
desiccant type and quantity per tower.
To Add Desiccant
WARNING — The following procedure provides in-
structions for adding the initial desiccant to the tow-
ers. If replacing desiccant, refer to the Maintenance
section of this manual.
1. Verify pressure gauges of both towers indicate 0 psig.
If not, depressurize the towers according to the shut-
down instructions in the Operation section of this
manual.
2. Remove the pipe plug or fill port flange cover (where
applicable) from the desiccant fill port at the top of
each tower. Refer to the General Arrangement draw-
ings in the back of the manual for the fill port location.
CAUTION – Pouring desiccant creates a fine dust;
safety goggles, gloves and a dust mask should be
worn by personnel installing desiccant. Refer to the
Material Safety Data Sheet that accompanies desic-
cant shipped loose for more complete information.
CAUTION – Do not tamp the desiccant in the towers.
Tamping damages desiccant and causes dusting.
3. Refer to Table 3 for desiccant
quantity per tower.
When using Table 3 you will find the desiccant quanti-
ties listed in layers. Each layer will vary in depth due
to the type, quantity and purpose of the desiccant.
Layer 1 must be installed first at the bottom of the
tower followed by layer number 2 etc., until the com-
plete charge of desiccant has been installed.