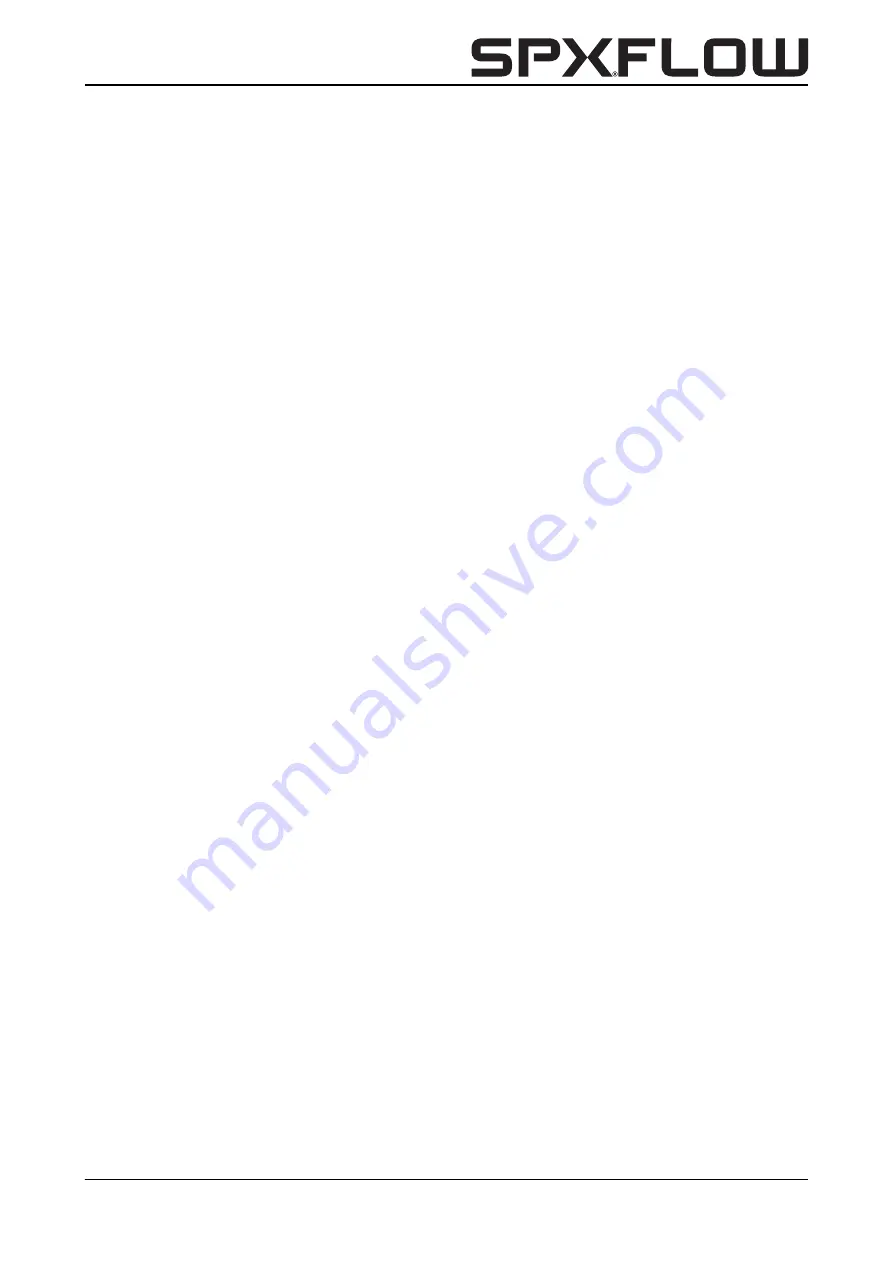
CRL/EN (1810) 2.2
General
13
CombiProLine
2 General
2.1
Pump description
The CombiProLine represents a range of vertical "heavy duty" centrifugal pumps. The
design of this range of pumps is based on the guidelines for: "Centrifugal Pumps for
Petroleum, Petrochemical and Natural Gas Industries" from the "American Petroleum
Institute" otherwise known as the API Standard 610 (identical to ISO 13709). The
CombiProLine range therefore meets the high requirements which have been set by the
refineries and the petrochemical industry.
The API 610 contains important technical guidelines in order to guarantee optimum
reliability. This pump amply complies with these requirements. This has been
demonstrated through extensive research and can be supported on the basis of
advanced methods of calculation.
2.2
Applications
• In general, this pump can be used for thin, clean or slightly polluted liquids. These
liquids should not affect the pump materials.
• The maximum allowed system pressure and temperature and the maximum speed
depend on the pump type and the pump construction.
• Further details about the application possibilities of your specific pump are mentioned
in the order confirmation and/or in the data sheet enclosed with the delivery.
• Do not use the pump for purposes other than those for which it is delivered without
prior consultation with your supplier.
Using a pump in a system or under system conditions (liquid, working
pressure, temperature, etc.) for which it has not been designed may hazard
the user!
Summary of Contents for Johnson Pump CombiProLine OH3
Page 2: ......
Page 4: ...2 EC EN 1712 6 0 ...
Page 6: ...4 INT EN 1512 1 2 ...
Page 10: ...8 CRL EN 1810 2 2 ...
Page 20: ...18 General CRL EN 1810 2 2 ...
Page 40: ...38 Dimensions CRL EN 1810 2 2 ...
Page 52: ...50 Parts CRL EN 1810 2 2 ...
Page 66: ...64 ORDFORM 1512 3 3 EN ...