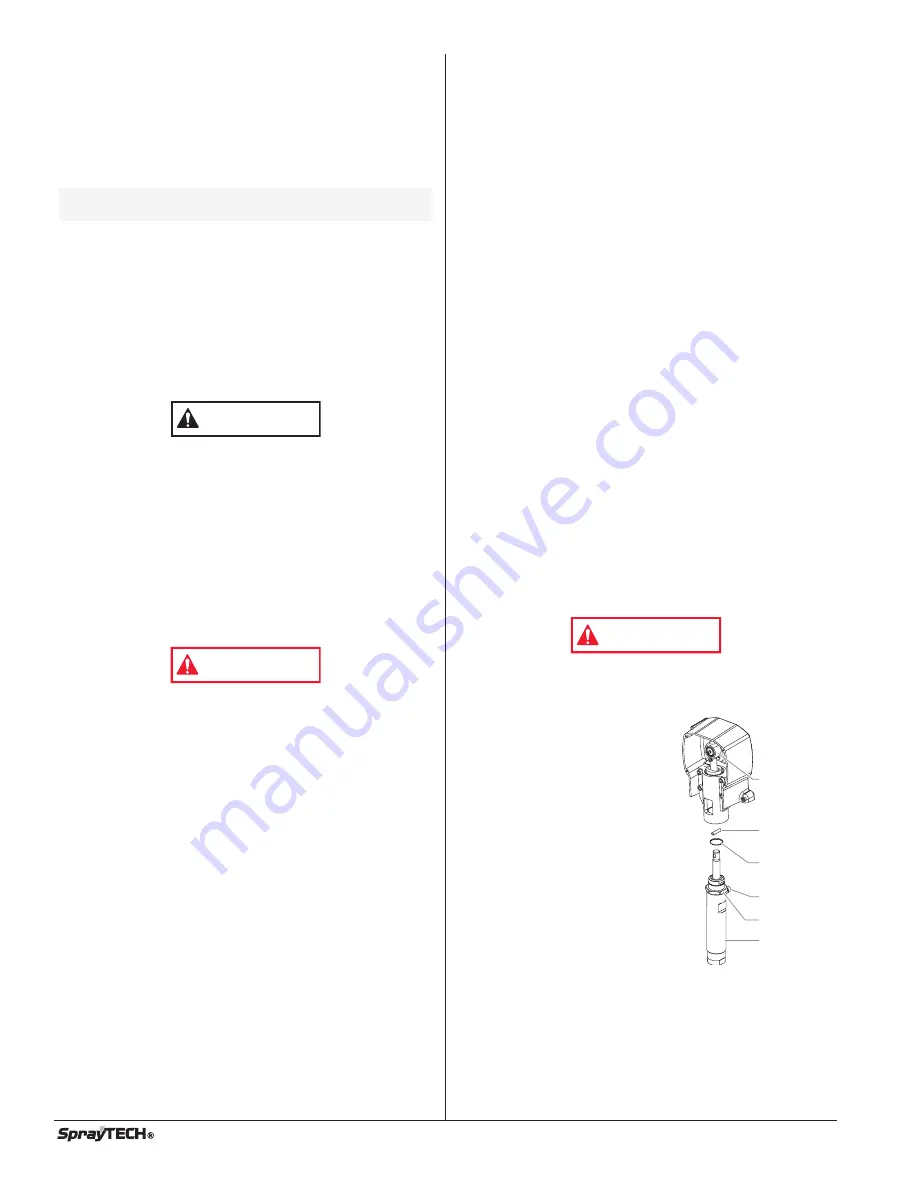
5. Line up the four holes around the outside of the clutch
field with the four set screw holes in the gear housing.
The clutch field wires should be at approximately the 1 or
2 o’clock position.
6. Route the two clutch field wires through the grommet and
into the EPC housing.
7. Carefully slide the clutch field into its bore in the gear
housing until it “bottoms out” within the housing. Do not
pinch the clutch field wires during installation.
8. Thread one of the set screws into its hole. Using an 1/8”
hex wrench, rotate the screw slowly until it contacts the
clutch field.
Do not tighten the set screw
. The tip of the
set screw should mate with the drill point hole in the field.
Check the clutch field for rotation. If it rotates within its
bore, the set screw is not seated within the drill point.
9. When the set screw is properly seated, install the remaining
three set screws.
Do not tighten the set screws.
10. Using a crossing pattern, tighten each of the setscrews
until they are snug. Once all four set screws are snug,
use a crossing pattern to tighten and torque the set
screws to 60–70 in./lbs.
It is very important to evenly snug, tighten, and torque the
clutch field set screws in a crossing pattern. This ensures
the clutch field will stay centered in the gear housing.
11. Line up the three screw holes and dowel pin hole on the
clutch rotor with the screw holes and dowel pin on the drive
shaft assembly hub. Place the clutch rotor onto the hub.
12. Using a 3/16” hex wrench, thread the three socket screws
and lock washers through the clutch rotor and into the
drive shaft assembly hub. Evenly snug, tighten, and
torque the socket screws to 75–85 in/lbs.
13. Make sure the friction surface of the clutch rotor is clean
and free from oil or grease.
14. Follow steps 17–20 in the “Replacing the Gears” procedure
to mate the pump housing with the gear housing.
Electrostatic discharge (ESD) potential could cause
damage to electronic pressure control. Use SprayTECH
ESD wrist strap P/N 0507958 or equivalent when working
on electronic pressure control.
15. Locate the two clutch field wires in the EPC housing.
Gently pull the wires fully into the EPC housing so that
there is no slack in the gear housing. Connect the wires
to their proper terminals on the EPC board (refer to the
labels created earlier in this procedure or the electrical
schematic in the Parts List section of this manual).
16. Carefully place the EPC assembly over the EPC housing
taking care not to pinch any wires.
17. Install the four screws that secure the EPC assembly to
the EPC housing. Tighten securely.
Mating the Gear Housing and the Clutch Housing
1. Place the gear housing assembly onto the cart in front of
the clutch housing. Line up the dowel pins in the gear
housing with their corresponding holes in the clutch
housing. Slide the gear housing assembly onto the clutch
housing until there is no gap between the housings.
2. Thread the four hex screws and lock washers through the
clutch housing and into the gear housing.
3. Using a 1/2” wrench, snug and tighten the hex screws in a
crossing pattern. Torque to 140–155 in./lbs.
4. Using a 9/16” socket, thread the two hex screws that secure
the gear housing to the cart through the underside of the
cart and into the gear housing. Torque to 100–120 in./lbs.
5. Connect the wire from the EPC housing to its mating
connector on the engine wire harness.
WARNING
CAUTION
NOTE: Apply blue Loctite to the four clutch field set
screws prior to installation.
14
© SprayTECH. All rights reserved.
6. Make sure that there is a white
PTFE
o-ring on the end of
the transducer that gets inserted into the filter housing.
Insert the transducer into the filter housing port.
7. Hold the transducer tube with a pliers to prevent it from
rotating, and turn the transducer nut clockwise with a 3/4”
open-end wrench to tighten it into the filter housing.
Torque the nut to 360–400 in./lbs.
Checking the Clutch Gap
1. Remove the plastic plug from the top of the clutch
housing. Look through the port to locate the clutch
armature and the clutch rotor.
2. Check the gap between the clutch armature and the clutch
rotor using a .016” feeler gauge and a .035” feeler gauge.
a. Insert each feeler gauge through the port and into the
gap between the clutch armature and the clutch rotor.
The .016” feeler gauge should fit in the gap. The .035”
feeler gauge should not fit in the gap.
b. Pull the engine pull cord several times to rotate the
clutch armature, checking the gap with each feeler
gauge between each pull.
c. If the .016” gauge does not fit or the .035” gauge does
fit at any checkpoint, the gap must be readjusted. This
is done by relocating the clutch hub and armature
assembly on the engine shaft. Refer to the
“Removing/Replacing the Clutch Hub and Armature
Assembly” procedure.
Servicing the Fluid Section
Use the following procedures to service the valves and repack
the fluid section.
1. Start the engine (refer to the procedures in the Operation
section of this manual). Turn the pressure control knob
clockwise to its maximum pressure setting.
2. Toggle the pump ON/OFF switch between the ON and OFF
positions in short bursts until the slider assembly stops in a
position where the fluid section connecting pin and retaining
ring are visible through the slot in the slider housing.
3. Turn off the engine and perform the Pressure Relief
Procedure.
Before proceeding, follow the Pressure Relief Procedure
outlined previously in this manual. Additionally, follow all
other warnings to reduce the risk of an injection injury,
injury from moving parts or electric shock.
4. Remove the return hose from
the clamp on the siphon tube.
Unscrew the siphon tube from
the inlet valve housing.
5. Loosen and remove the fluid
hose from the fitting on the back
of the cylinder of the fluid
section.
6. Loosen and remove the four
front cover screws. Remove
the front cover.
7. Slide the retaining ring up on
the slider assembly to expose
the connecting pin.
8. Push the connecting pin forward
through the slider assembly and
piston. The connecting pin will
fall out from the rear window of the slider housing where it
can be retrieved.
Connecting
Pin
Fitting
Retaining
Ring
Slider
Assembly
Jam Nut
Cylinder
WARNING