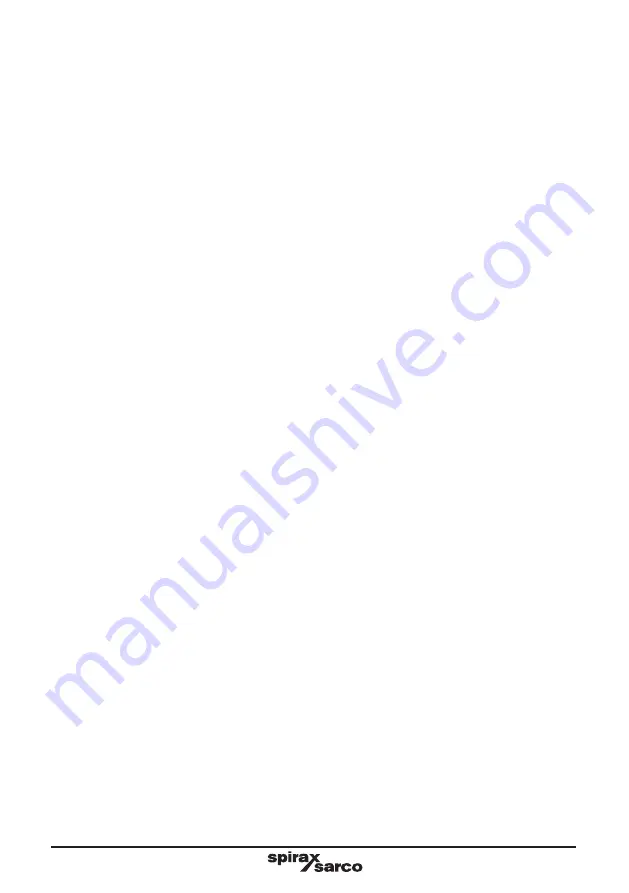
IM-P361-02-EN-ISS1
CTLS
14
start of text under grey section header box
start of text continuing from previous page
TRANSLATION RUN OVER
3.2 Fitting the actuator (retract) to the valve
-
Remove the screw and nut (
13
and
14
) then the rear and front clamp (
11
and
12
).
-
Ensure the indicator scale is facing the same way as the valve name-plate.
-
Apply the control signal pressure to the top of the actuator to bring the spindle (
19
) to the mid-travel
position.
-
Manually push the valve spindle down to ensure that the plug is on the valve seat.
-
Screw the yoke adapter (
35
) onto the valve and tighten it to 50 Nm (36.9 lbf ft) - (TN2 _ _ _ E_ only).
-
Put the yoke sleeve (
36
) onto the valve bonnet (TN2 _ _ _ EC only).
-
Locate the actuator yoke onto the valve bonnet and fit the lock-nut (
A
).
-
Screw the lock-nut of the valve’s spindle down to the lowest part of the valve spindle.
-
Screw the bottom connector (
29
) onto the valve spindle, caution there must be no valve spindle threads
above the bottom connector.
-
Loosen the lock-nut and screw the connector (
20
) upwards 3 turns, then remove the air supply.
-
Adjust the connector (
20
) so that it touches the bottom connector (
29
). Apply the minimum signal pressure
+ 0.1 bar (1.45 psi) maximum to the top of the actuator then unscrew the connector (
20
) downwards 3
turns, and finally tighten the lock-nut (
15
).
-
Release the control air signal. Fit the front and rear clamps (
11
and
12
).
-
Fit the locking screws and nuts (
13
and
14
) loosely.
-
Operate the actuator and valve over its full travel four times to ensure alignment.
-
Tighten the mounting nut to 50 N m (36.9 lbf ft).
The air supply to the actuator must be '
dry and free from oil
'. Contact Spirax Sarco for more details with
relation to composite tube/media compatibility. For high temperature conditions, insulate the control valve
and pipework only to protect the actuator.
Note:
The actuator cannot be fitted onto an older style control valve.
Caution:
If the complete assembly is installed horizontally then the air supply
must
be connected at the
lowest point of the actuator.
Warning:
The actuator cylinder must only be pressurized on the opposite side of the piston
holding the spring. The housing vent cap must be left unrestricted. If the assembly is to be mounted
horizontally then it is essential to provide suitable support for the actuator.