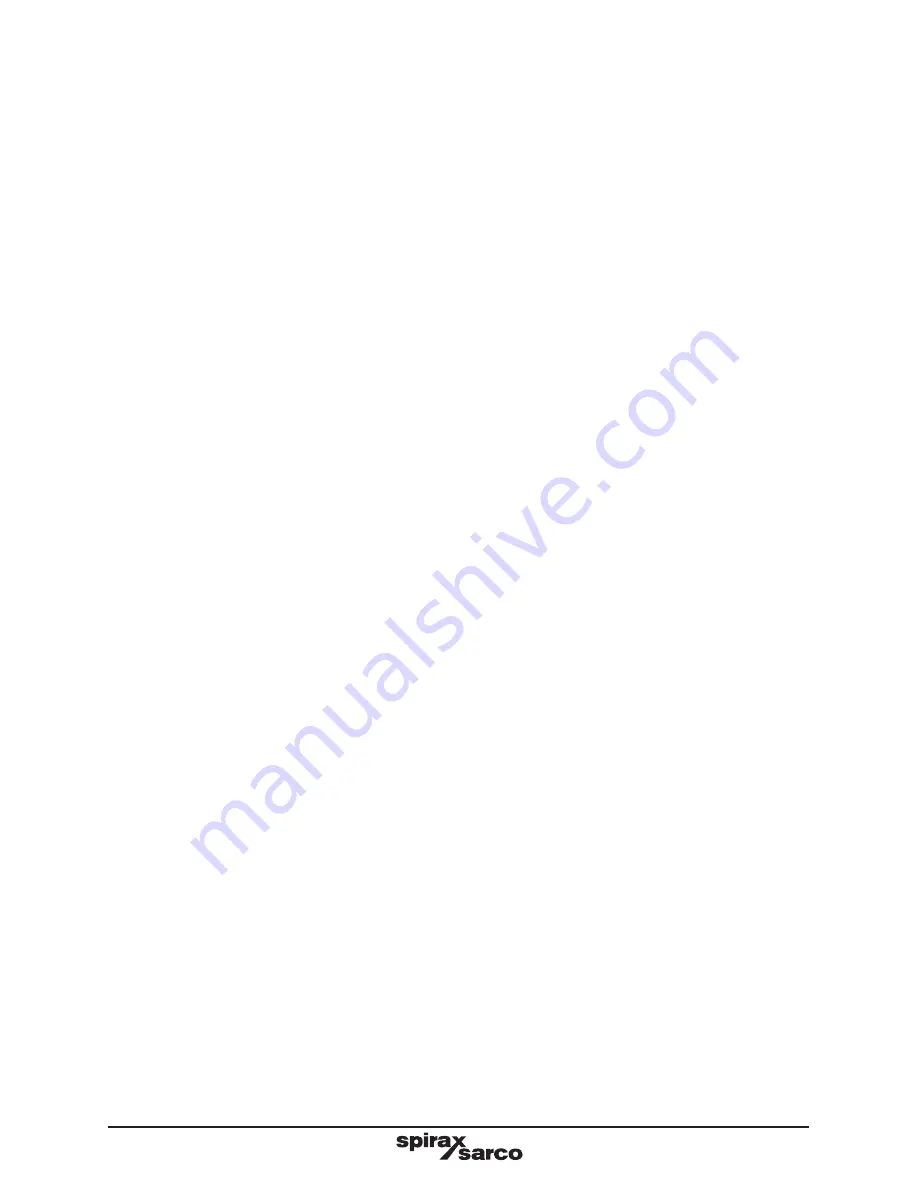
IM-P015-04-EN-ISS2
CMGT
3
1.6 The system
Consider the effect on the complete system of the work proposed. Will any proposed action (e.g.
closing isolation valves, electrical isolation) put any other part of the system or any personnel
at risk?
Dangers might include isolation of vents or protective devices or the rendering ineffective of
controls or alarms. Ensure isolation valves are turned on and off in a gradual way to avoid system
shocks.
1.7 Pressure systems
Ensure that any pressure is isolated and safely vented to atmospheric pressure. Consider double
isolation (double block and bleed) and the locking or labelling of closed valves. Do not assume
that the system has depressurised even when the pressure gauge indicates zero.
1.8 Temperature
Allow time for temperature to normalise after isolation to avoid the danger of burns.
1.9 Tools and consumables
Before starting work ensure that you have suitable tools and/or consumables available. Use only
genuine Spirax Sarco replacement parts.
1.10 Protective clothing
Consider whether you and/or others in the vicinity require any protective clothing to protect against
the hazards of, for example, chemicals, high /low temperature, radiation, noise, falling objects,
and dangers to eyes and face.
1.11 Permits to work
All work must be carried out or be supervised by a suitably competent person.Installation and
operating personnel should be trained in the correct use of the product according to the Installation
and Maintenance Instructions.
Where a formal 'permit to work' system is in force it must be complied with. Where there is no such
system, it is recommended that a responsible person should know what work is going on and, where
necessary, arrange to have an assistant whose primary responsibility is safety.
Post 'warning notices' if necessary.
1.12 Handling
Manual handling of large and/or heavy products may present a risk of injury. Lifting, pushing,
pulling, carrying or supporting a load by bodily force can cause injury particularly to the back.
You are advised to assess the risks taking into account the task, the individual, the load and the
working environment and use the appropriate handling method depending on the circumstances
of the work being done.
1.13 Residual hazards
In normal use the external surface of the product may be very hot. If used at the maximum
permitted operating conditions the surface temperature of some products may reach temperatures
of 500 °C (932 °F).
Many products are not self-draining. Take due care when dismantling or removing the product from
an installation (refer to ‘Installation and Maintenance Instructions’).
1.14 Freezing
Provision must be made to protect products which are not self-draining against frost damage in
environments where they may be exposed to temperatures below freezing point.
Summary of Contents for TD62LM
Page 20: ...IM P015 04 EN ISS2 CMGT 20 ...