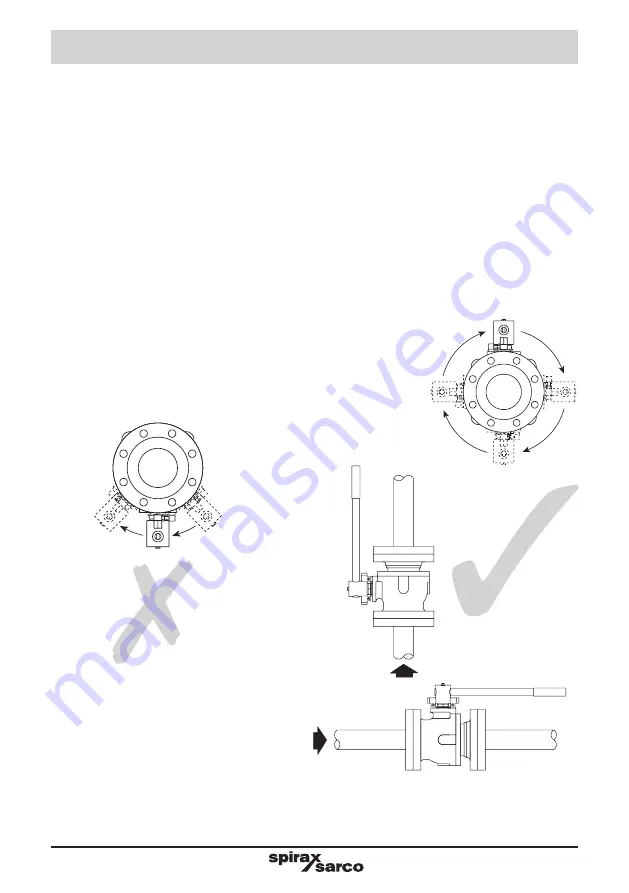
IM-P133-65
CMGT Issue 2
8
Note: Before actioning any installation observe the 'Safety information' in Section 1.
Although the valve has great structural integrity, severe misalignment and/or the pulling effect of incorrect
pipe length will have a detrimental effect on the valve and must be avoided. Particular attention should be
paid to correct pipe alignment such that the inlet pipework and valve are all on the same axis.
Valves are for on/off applications and may be operated manually.
Wherever practicable, valves should be installed where there is adequate space available so that they can
be conveniently operated and maintained.
Before installing a valve, check to ensure that size, pressure rating, materials of construction, end connections,
etc. are suitable for the service conditions of the particular application.
Care must be taken to ensure that all dirt which may have accumulated in the valve during storage is removed
before installation, maintain cleanliness during installation since the introduction of dirt can result in damage
to the valve seats and operating mechanism.
To minimise the danger of abrasive particles damaging the seats, pipeline strainers should be fitted upstream
of the valves.
Install the valve with the handle in a suitable position. The preferred position is with the spindle vertical. The
valve can be installed in any position for gas service (see Figure 3 below).
When used on steam services:
1.
Fit a trapped drain pocket upstream of the valve.
2.
Open valve slowly to prevent the risk of waterhammer damage.
Fig. 3 Correct installation for gas service
Do not mount the valve upside down
for liquid service (Figure 2).
Fig. 2 Incorrect installation for
liquid service
Valves should be installed into the
pipeline in the fully closed position.
Always open valves slowly to avoid
system shocks.
3. Installation
Summary of Contents for M33 ISO Series
Page 15: ...IM P133 65 CMGT Issue 2 15...
Page 16: ...IM P133 65 CMGT Issue 2 16...