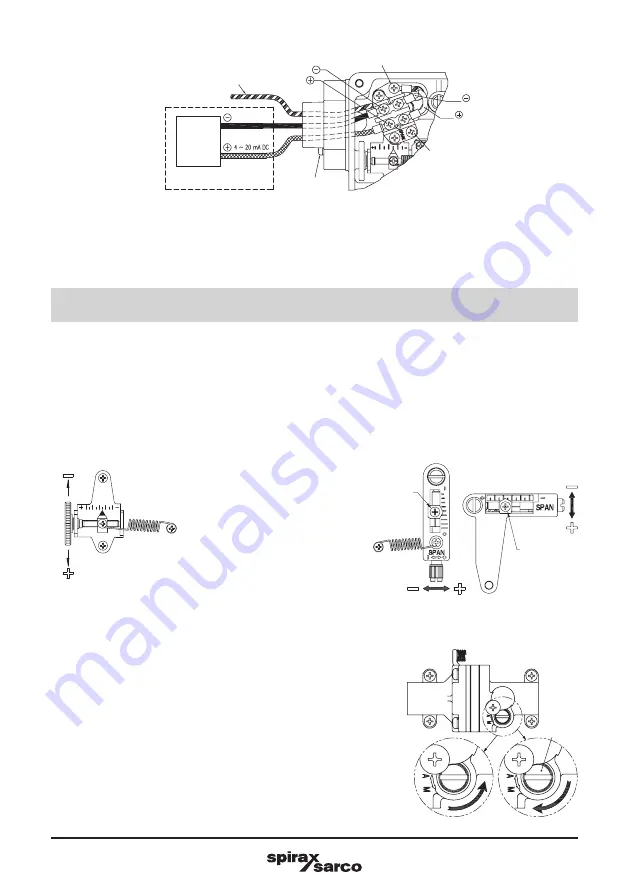
IM-P703-05
CTLS Issue 3
EP6 Positioner
3.2 Non-explosion proof type
4. Adjustments
Controller
(AO)
(DCS/PLC sourcing
output card)
Ground
Ground (M4)
Ground (M4)
Spare bolt
(M4)
Black
Red
Auto
manual
switch
Manual
Auto
4.3 Adjustment – A/M switch (Auto/Manual)
4.3.1
Auto manual switch is located on the top of pilot unit. Auto
manual switch allows the positioner to be functioned as by-
pass. If the switch is rotated counterclockwise (toward “M”,
Manual), then the supply pressure will be directly supplied to
the actuator through Out1 port of positioner regardless of input
signal. On the other hand, if the switch is turned clockwise
(toward “A”, Auto), then the positioner will operate normally by
input signal.
4.3.2
Make sure that the supply pressure does not exceed the rated
pressure level of the actuator before the switch is loosened
toward “M”.
4.3.3
After using the “Manual” function, return the auto manual switch
to “Auto”.
4.1 Adjustment -
Zero Point
Set input signal at 4mA (or 20mA)
as the initial current, then rotate
the adjust wheel of zero setting
unit upward or downward to set
actuator’s zero point.
Please refer to the figure below.
Lock
screw
Lock screw
4.2 Adjustment - Span
4.2.1
After setting zero point, supply input signal at 20mA (or 4mA) as the end point
current and check the actuator stroke. If the stroke is low, the span should be
stretched. If the stroke is high, the span should be reduced.
4.2.2
Changing span will affect zero point setting so zero point should be set again
after span has been adjusted.
4.2.3
Above two steps are
required several times
until both zero and span
are properly set.
4.2.4
After proper setting,
tighten lock screw of the
span unit.
2.2.2
Piping and cam direction setting
for rotary double actuator