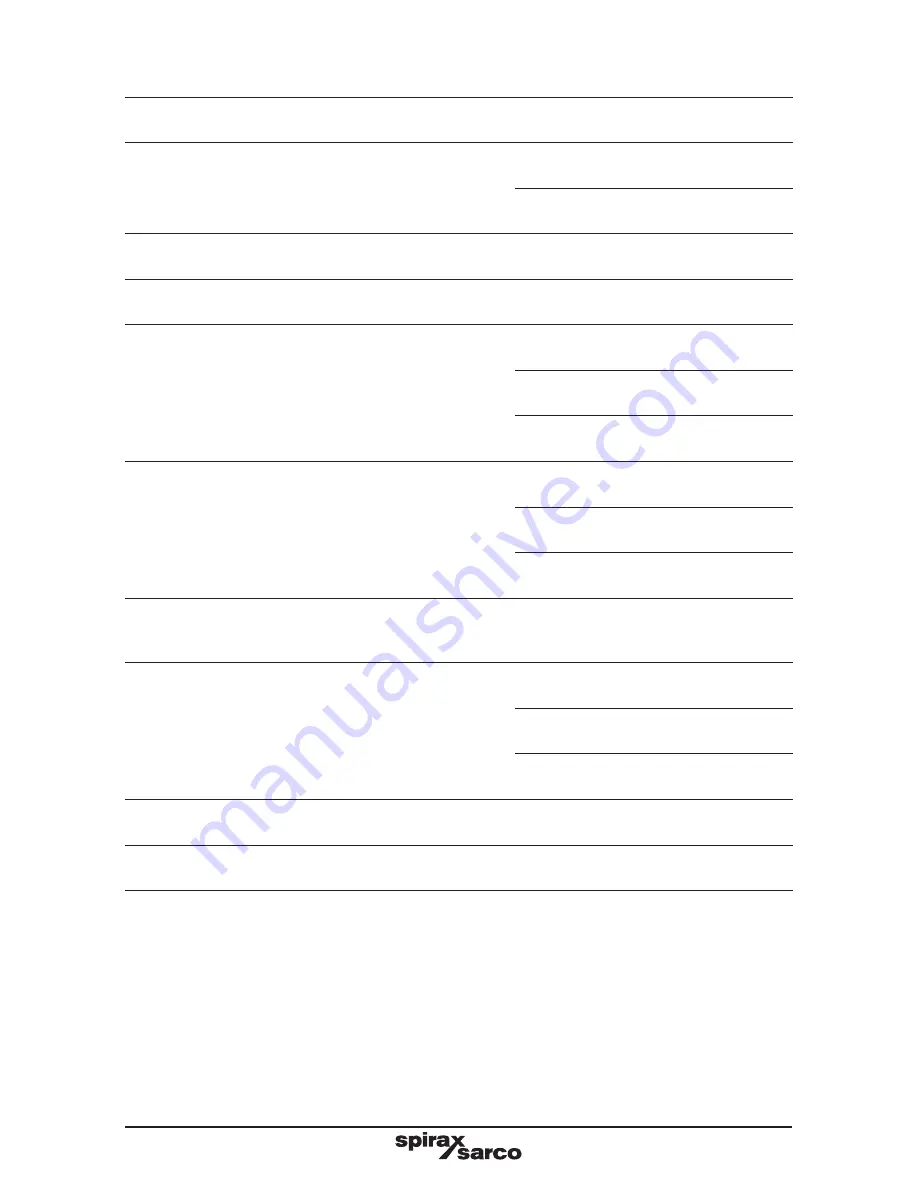
IM-P470-03
CH Issue 7
9
Body design conditions
PN25
Maximum design pressure
A-D-E
25 bar g @ 120
°C
A-B-C
17.2 bar g @ 40
°C
Maximum design temperature
232
°C @ 21 bar g
Minimum design temperature
-10
°C
Maximum upstream pressure for saturated steam
service
For ASME 150, see A-B-C
DP27
,
DP27R
and DP27Y
17 bar g
DP27G and DP27GY
25 bar g
DP27E
10 bar g
Maximum operating temperature
For ASME 150, see A-B-C
DP27, DP27Y
232
°C @ 21 bar g
DP27E
190
°C @ 10 bar g
DP27G, DP27GY
120
°C @ 25 bar g
Minimum operating temperature
Note:
For lower operating temperatures consult Spirax Sarco
0
°C
Maximum differential pressure
DP27
,
DP27R
and DP27Y
17 bar g
DP27G and DP27GY
25 bar g
DP27E
10 bar
Designed for a maximum cold hydraulic test pressure of :
38 bar g
Note:
With internals fitted, test pressure must not exceed :
25 bar g
Summary of Contents for DP27
Page 2: ...IM P470 03 CH Issue 7 2...
Page 7: ...IM P470 03 CH Issue 7 7...
Page 23: ...IM P470 03 CH Issue 7 23 14 15 13 13 16 22 20 19 18 14 21 17 17...
Page 31: ...IM P470 03 CH Issue 7 31 51 52 55 54 58 58 56 57 53...
Page 38: ...IM P470 03 CH Issue 7 38...
Page 39: ...IM P470 03 CH Issue 7 39...
Page 40: ...IM P470 03 CH Issue 7 40...