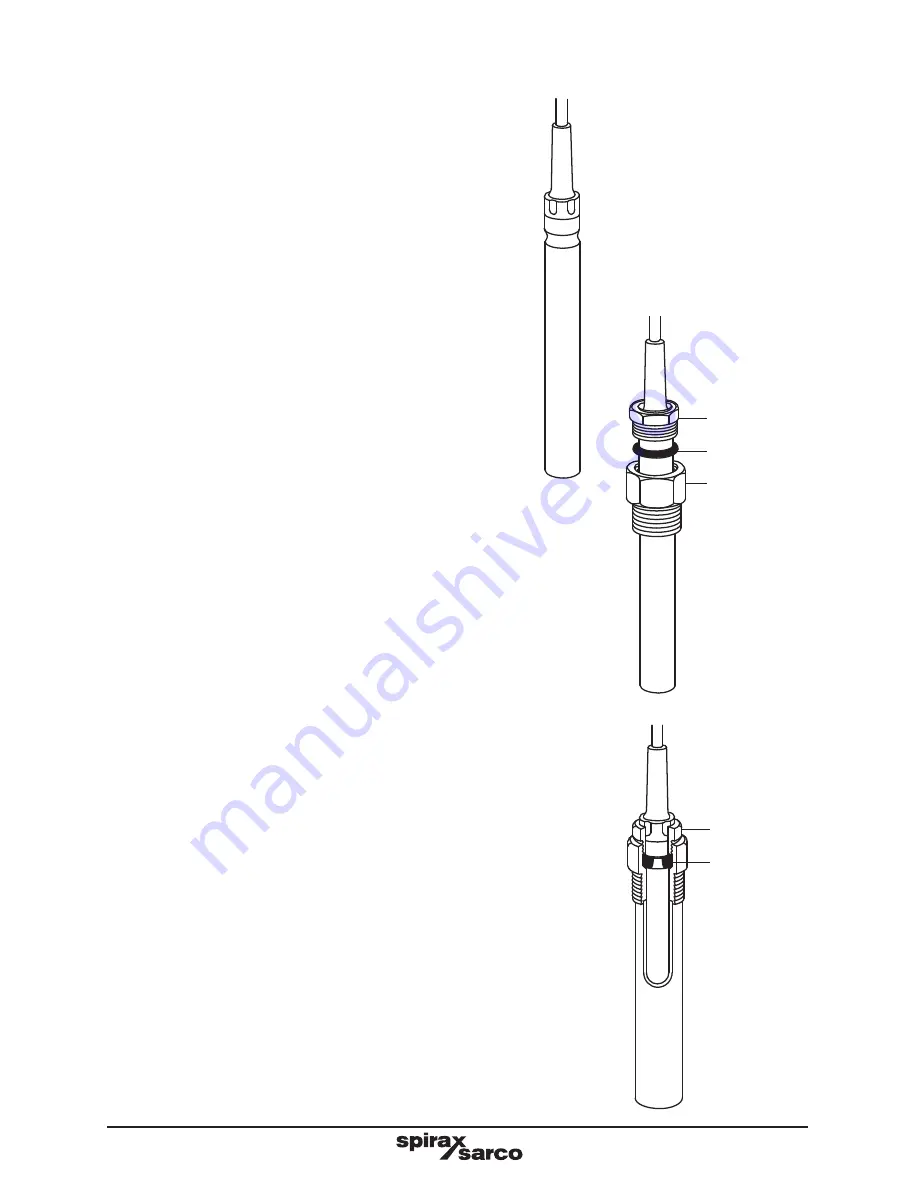
IM-P102-04
CTLS Issue 7
10
2.9 Sensor bulb
The type 37D control is fitted with a plain bulb as in Fig. 3,
but as standard this bulb is supplied with an adaptor shown
in Fig. 4, consisting of a union nipple (U), 'O' ring (
V
) and
gland nut (
W
).
2.10 Use of plain bulb
Where it is desired to use a plain bulb as in Fig. 3 the
adaptor can be removed by unscrewing the gland nut (
W
)
from the union nipple Fig. 4 and withdrawing each piece
of the assembly separately over the bulb.
2.11 Use of immersion bulb
Where it is desired, insert the bulb into a vessel under
pressure. Unscrew the gland nut (W) from the union
nipple (
U
). This will enable the union nipple to withdraw
over the bulb.
The union nipple can now be screwed into the tapping
provided at the temperature sensing point.
The union nipple is normally threaded ¾" BSP but may be
¾" NPT if specially ordered.
Insert the bulb through the union nipple (
U
) until the 'O'
ring (
V
) seats in the union nipple as shown in Fig. 4 and
screw home the gland nut (
W
) to compress the 'O' ring.
The gland nut needs to be little more than finger tight. Do
not overtighten otherwise damage to the 'O' ring will result.
2.12 Pockets
In all cases where the temperature sensing point is in a fluid
under pressure it is best to use a pocket so that the bulb can
be withdrawn for servicing without draining down the plant.
Pockets must also be used where the medium being
controlled would attack and destroy the material from which
the bulb is constructed.
The top of the pocket is formed exactly as the union nipple
and should be screwed into the tapping (¾" BSP or ¾" NPT)
provided at the temperature sensing point.
Insert the bulb into the pocket until the 'O' ring seats in the
union nipple as Fig. 5, and screw home the gland nut (
W
) to
compress the 'O' ring.
The gland nut (
W
) will be little more than finger tight. Do
not overtighten otherwise damage to the 'O' ring will result.
Fig. 3
Fig. 4
Fig. 5
W
V
U
W
V
¾" BSP taper
NPT available
¾" BSP taper
NPT available
Summary of Contents for 37D
Page 2: ...IM P102 04 CTLS Issue 7 2...
Page 28: ...IM P102 04 CTLS Issue 7 28...