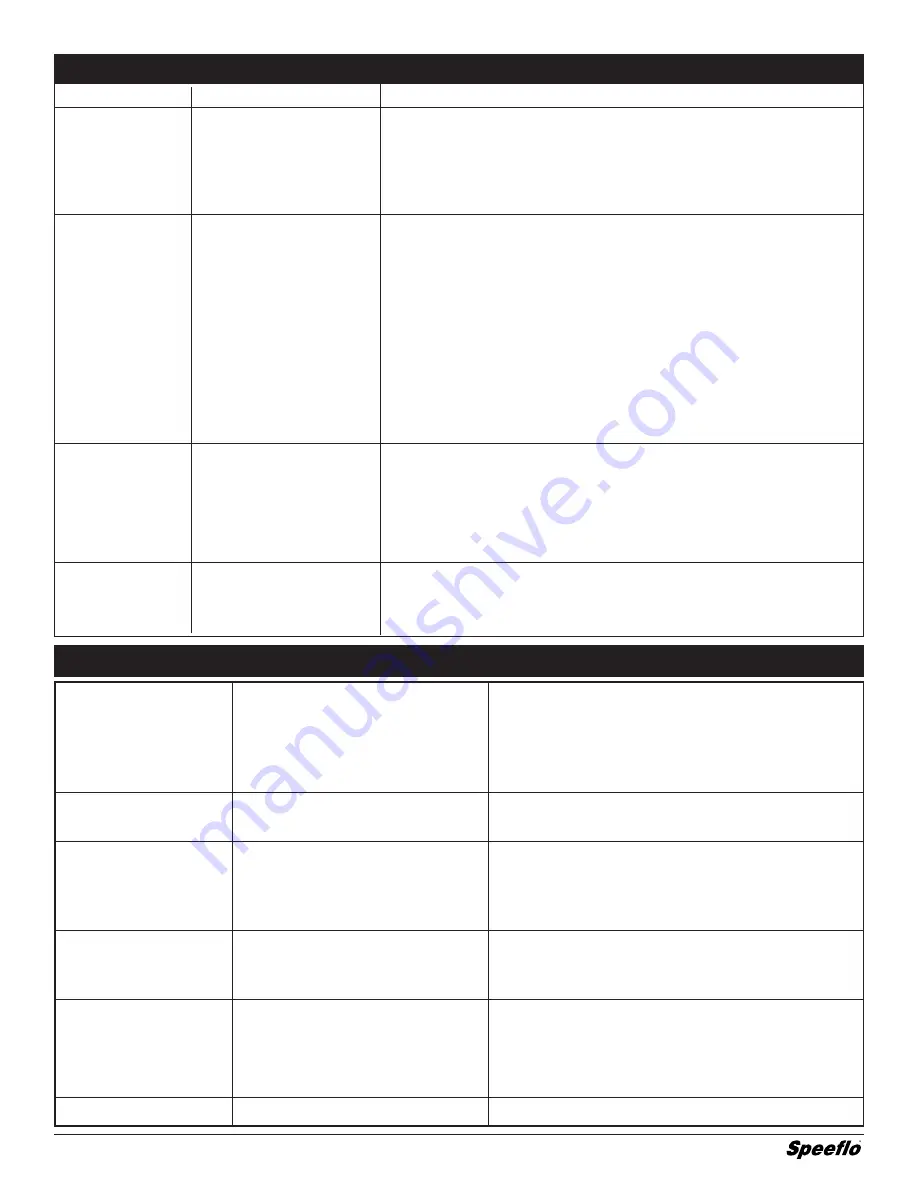
CONDITION
POSSIBLE CAUSE
CORRECTION
Oil motor stalls at bottom.
Fluid pump piston seat unthreaded.
If connecting rod is okay, remove cylinder head plug and pop valve down. Replace plug and start
(No unusual heat problems.)
machine. If machine cycles up and stops at bottom again, then problem is piston seat on fluid pump.
Check piston seat. Repair or replace as necessary. If piston seat is okay and problem does not change,
check oil motor.
Valve sticking or oil motor trip rod shifter Remove valve and check for scratches and rough movement when sliding it up and down. Replace
assembly separated.
valve and spool in this condition. Check trip rod for possible separation.
and spool in this condition. Check trip rod for possible separation.
Oil motor stalls at top.
Valve sticking.
Remove valve and check for scratches and rough movement when sliding it up and down. Replace
(No unusual heat problems)
valve and spool in this condition.
Broken spring retainer (valve rod
Replace valve rod assembly.
assembly)
Broken spring or valve rod.
Replace valve rod assembly.
Air in hydraulic motor.
Reset Valve.
Purge Air, generally accomplished by low pressure cycling of motor/pump assembly for 5 - 10 minutes.
Check for causes of air introduction.
• Loose fittings in tank.
• Loose fittings on hydraulic pump.
• Loose hose connections.
• Low oil in reservoir.
Air in fluid pump.
Stall at top can occur randomly when fluid pump picks up air. Reset valve. Avoid air in the fluid pump.
Low pressure (okay on
Blown piston seal.
Before dismantling oil motor, start machine. With pump cycling under pressure, touch the hydraulic
down stroke, sluggish on
cylinder and the head to see if cylinder or head gets hotter. This will help determine if piston seal.
up.stroke - high heat)
is blown or piston nut is broken. If heat is on the head, check the O-Rings on spool valve.
Note: Engine labors on
upstroke, idles back at stall
on the down stroke.
Cracked piston.
Dismantle oil motor and check piston seals cylinder bore and piston nut. Pay special attention to piston
nut. It can be cracked and not show externally.
Low pressure (both strokes Blown center O-Rings on spool valve.
Before dismantling oil motor, start machine. With pump cycling under pressure, touch the head to see if
- high heat)
the head becomes hotter. This will help determine if center O-Ring is blown on spool valve. If hot,
Note: Engine labors at stall
remove and replace O-Ring.
on both strokes
Bad hydraulic pump.
Replace hydraulic pump.
Troubleshooting Guide: Hydraulic Motors
© Titan Tool Inc. All rights reserved.
15
Troubleshooting Guide: Fluid Sections
CONDITION
POSSIBLE CAUSE
CORRECTION
Pump delivers on upstroke only or
Lower foot valve ball is not seating due to
Remove foot valve assembly. Clean and inspect. Test foot valve by filling with
goes up slowly and down fast.
trash or wear.
water; if ball fails to seal the seat, replace ball.
(Commonly called downstroke dive.)
Material too viscous to siphon.
Thin material - contact manufacturer for proper thinning procedures.
Air leaking in on siphon side or damaged siphon
Tighten all connections between pump and paint container. If damaged, replace.
hose. Siphon may be too small for heavy material
Switch to larger diameter siphon set.
Pump delivers on down stroke only
Upper ball is not seating due to trash or wear.
Check upper seat and ball with water. If ball fails to seal, replace seat.
.or goes up fast and down slowly
Lower packing set is worn.
Replace packing set if worn.
Pump moves up and down fast,
Material container is empty or material is too thick
Refill with new material. If too thick, remove siphon hose and immerse pump or not
delivering material.
to flow through siphon hose
add thinner to material. Change to bigger siphon set. Open bleed valve to .
remove air and restart pump.
Bottom ball stuck to foot valve seat.
Remove foot valve. Clean ball and seat.
Siphon hose is kinked or loose.
Straighten.
Pump moves up and down slowly
Loose connections. Bleed valve is open partially or
Check all connections between pump and gun. Tighten as necessary. If material
when spray gun is shut off.
bleed valve is worn. Lower packing seat is worn.
is flowing from bleed hose, close bleed valve or replace if necessary. Should
none of the above be evident, replace lower packing.
Upper and/or lower ball not seating.
Reseat balls by cleaning.
Not enough fluid pressure at gun.
Spray tip is worn.
Replace.
Outlet filter or gun filter is clogged
Clean or replace filter.
Low voltage and/or inadequate amperage.
Check electrical service. Correct as required.
Hose size or length is too small or too long.
Increase hose size to minimize pressure drop through hose and/or reduce hose
length.
Pump chatters on up or down stroke
Solvent has caused upper packing to swell.
Replace packing.