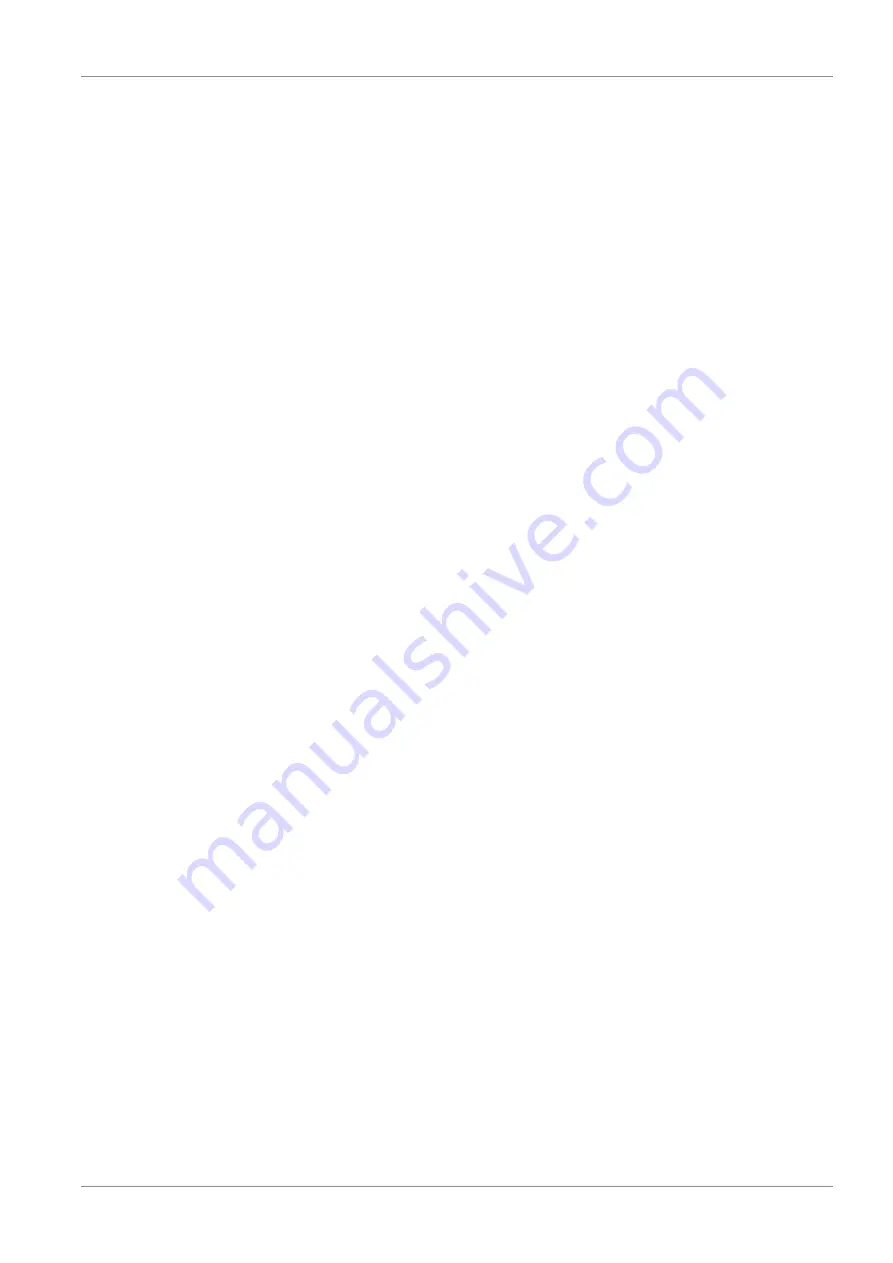
Spectron Gas Control Systems GmbH
Commissioning | 6
GES_E71-VCR_0222
15
6 Commissioning
6.1 Preparations for commissioning
Purge the armature prior to initial commissioning! It is imperative to adhere to the direction of
the gas flow when doing this! You must not purge counter to the usual direction of flow (from the
tapping point to the process gas source), as this can flush debris resulting from the installation
work, for example, back into the armature.
The connecting threads and connecting surfaces of the gas source valves as well as the sealing
rings must be checked to ensure that they are in perfect condition.
Always turn shut-off valves as far as the stop when opening or closing them.
Make sure that:
– the fittings are marked for the corresponding gas type,
– all protective caps have been removed,
– the assembly has been correctly carried out and a leak test has been performed,
– all valves are closed (the red marking is visible in the handwheel window)
– the pressure regulator has been depressurised (if possible),
– the purge gas supply (only standard for SP4 and SP6) is in operation,
– the on-site exhaust gas system is functional at all times and is in operation,
– all shut-off armatures are checked for loose connections and
– the controller is in operation.
6.2 Procedure for commissioning
Flushing in the entire line network to the process must be implemented via a waste gas valve on
the process. To do this, refer to the system documentation for the consumer.
1. Close all valves and fully depressurise the pressure regulator by turning the of the hand-
wheel anticlockwise as far as it will go.
2. Open the process gas source valve and, if necessary, the downstream valves. Ensure that
the pressure regulator is not subjected to a pressure surge.
3. Slowly set the pressure regulator to the required outlet pressure. The process source pres-
sure and the gas type properties are to be taken into account here.
During regular operation, the system will be in supply mode.
For interrupting the supply or decommissioning, close all valves and fully depressurise the pres-
sure regulator by turning of the handwheel anti-clockwise as far as it will go.