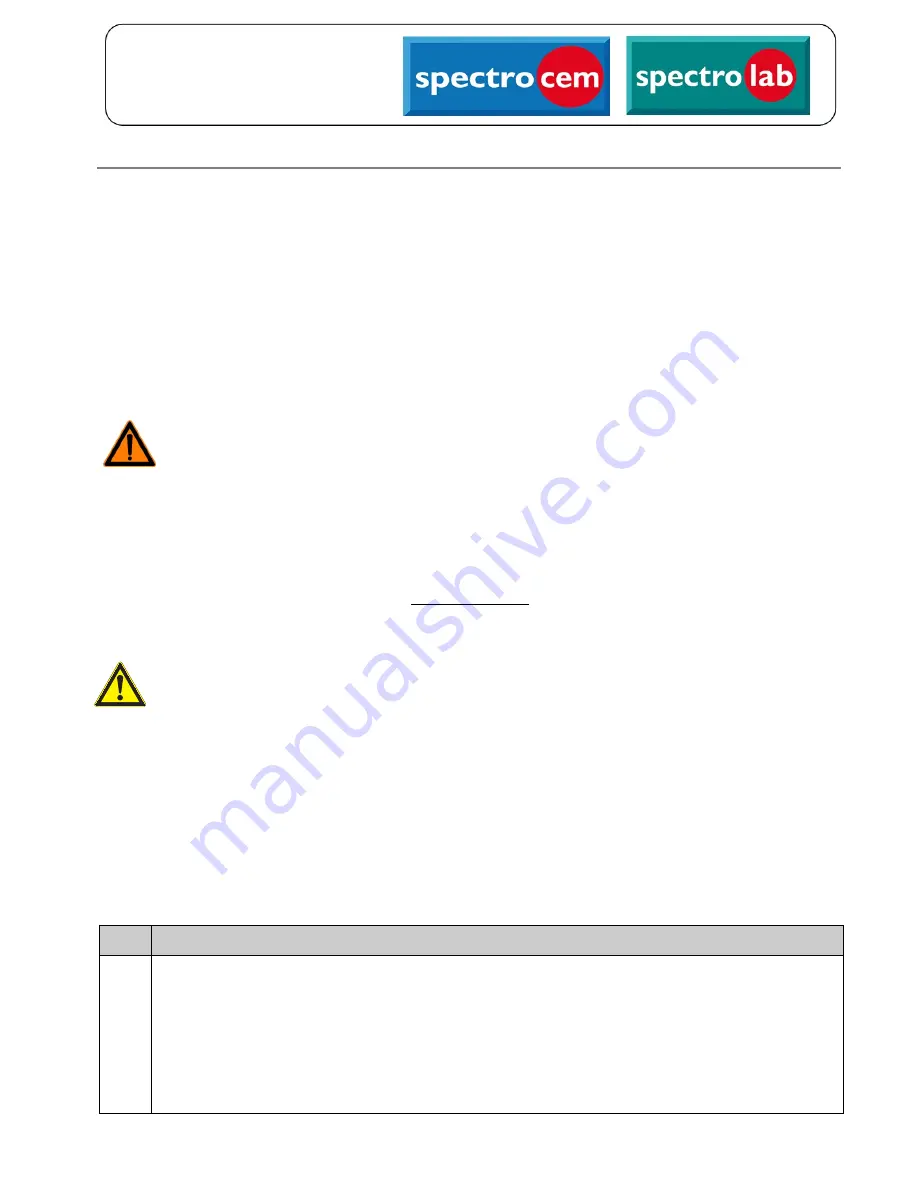
BE_55+56-2U_1212.docx
13
Operating Manual
of the BM and BE series
4.
Operation
4.1
Labelling
Labelling example
Hydrogen (H
2
)
BM55-2U-300-10-M-M-H2
P1: 300 bar
P2: 10 bar
Note
The gas type must be specified on the pressure control panel. If the gas type is not specified on
the type plate, it must be done using the attached gas-type adhesive labels before the device is
put into operation for the first time.
Warning
Only the gas type for which the pressure control panel was ordered may be specified on it.
4.2
Installing the pressure control panel
Note
You can find instructions on how to install the pressure control panel in the installation manual
MA_BM+BE.
You can view and download this at www.spectron.de.
4.3
Putting the pressure control panel into operation
Important
Before putting the equipment into operation for the first time, the entire pressure control panel must
be purged via the process gas valve right up to the consumer. It is imperative to adhere to the
direction of the gas flow when doing this. You must not purge counter to the usual direction of flow
(from the tapping point to the pressure control panel), since this can flush debris resulting from the
installation work, for example, back into the pressure regulator.
The connecting thread and connecting surfaces of the gas cylinder valves and the sealing rings of
the manual connectors of the pigtails must be checked to ensure they are in perfect condition.
Pigtails with manual connectors are connected to gas cylinder valves without the need for a tool.
Pigtails with flat faces for tightening (generally for corrosive or toxic gases) are tightened with
a suitable spanner until they are gas-tight.
Always turn shut-off valves as far as the stop when opening or closing them.
Step
Activity
1 Ensure
that:
The gas type is specified on the pressure control panel.
All protective caps have been removed.
The installation has been carried out properly.
The pigtails and other connecting points have been checked for leaks.
The waste gas valves are closed (the red marking is visible in the handwheel window).
The pressure regulator is released.