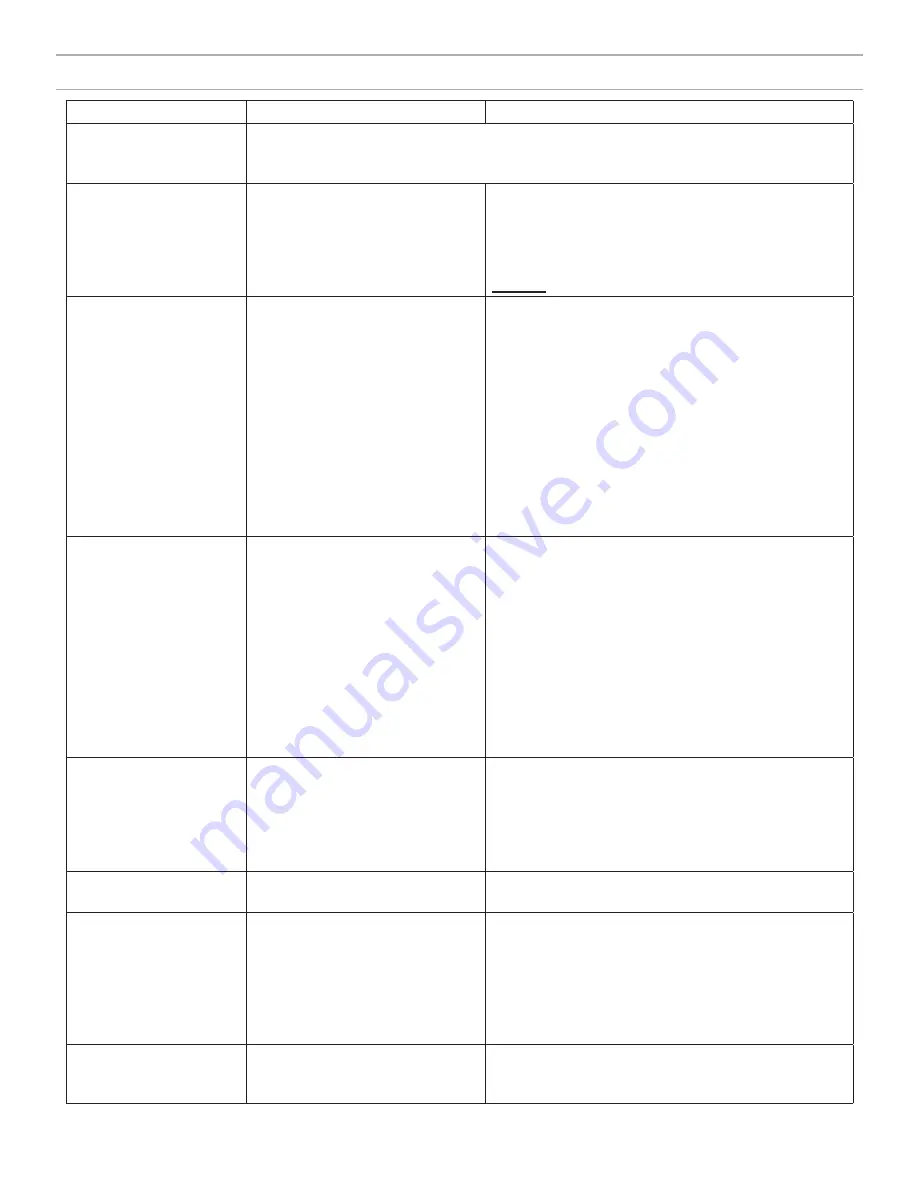
12
Trouble Shooting - continued
PROBLEM
POSSIBLE CAUSES
SOLUTION
5. Motor runs hot.
These motors will run hot to the touch, however, this is normal. They are designed that
way. Thermal overload protector will function to turn them off if there is an overload or high
temperature problem. Excessive heat can be caused by:
a. Low voltage.
b. Installed in direct sun.
c. Poor ventilation.
Increase size of electrical wire. Be sure motor is
operating on correct voltage.
Shield motor from sun’s rays.
DO NOT block motor ventilation openings.
6. Noisy operation of
pump.
a. Air leak in suction line.
b. Restricted suction line due
to blockage or under size pipe.
Indicated by high vacuum reading
at pump suction.
c. Foreign matter (gravel, metal,
etc.) in pump impeller.
d. Cavitation.
Repair leak. Check suction pipe, red filler plug, and
o-ring (See Problem 1).
Remove blockage or increase suction pipe size. Are all
suction valves fully open?
Disassemble pump and remove foreign matter from
impeller.
Improve suction conditions. (Reduce suction line
length, reduce number of fittings, increase pipe size.)
7. Motor overload
protection “kicks out”.
a. Motor is not connected properly.
b. Low voltage due to under size
wire or low incoming voltage.
c. Wrong size heaters in protective
device.
d. Overload due to binding in pump
or wrong size impeller.
Check wiring diagram on motor.
Check with volt meter. Increase size of supply wire.
Report low supply voltage to power company. Voltage
at motor must be within 10% of motor nameplate
voltage.
Heaters should be one size larger than full load amps
shown on motor nameplate.
Indicated by high amperage readings on motor, binding
shaft. Disassemble unit and correct.
8. The LED light is not
working?
a. Moisture in air tubing or bad air
button.
b. Control Box.
Remove air tubing from air switch at control box. Con-
nect a short piece of air tubing to the LED air switch.
Blow into tube and check if LED turns ON/OFF.
Contact certified electrician to diagnose control box
components.
9. The volume control
knob keeps spinning?
a. Broken Spindle.
Contact your pool service company or call 800-223-
8538.
10. My ON/OFF air
button is not working
properly?
a. Control Box.
b. Air tubing.
Check GFCI. If green LED does not stay ON, contact a
certified electrician to diagnose control box compo-
nents.
Check air tubing connection on the control box. Check
that the tubing is not bent or pinched. Tubing may
need to be replaced.
11. The system will not
turn OFF?
a. Control Box Components.
Press TEST button on the control box GFCI to turn off
system. Contact a certified electrician to diagnose con-
trol box components.