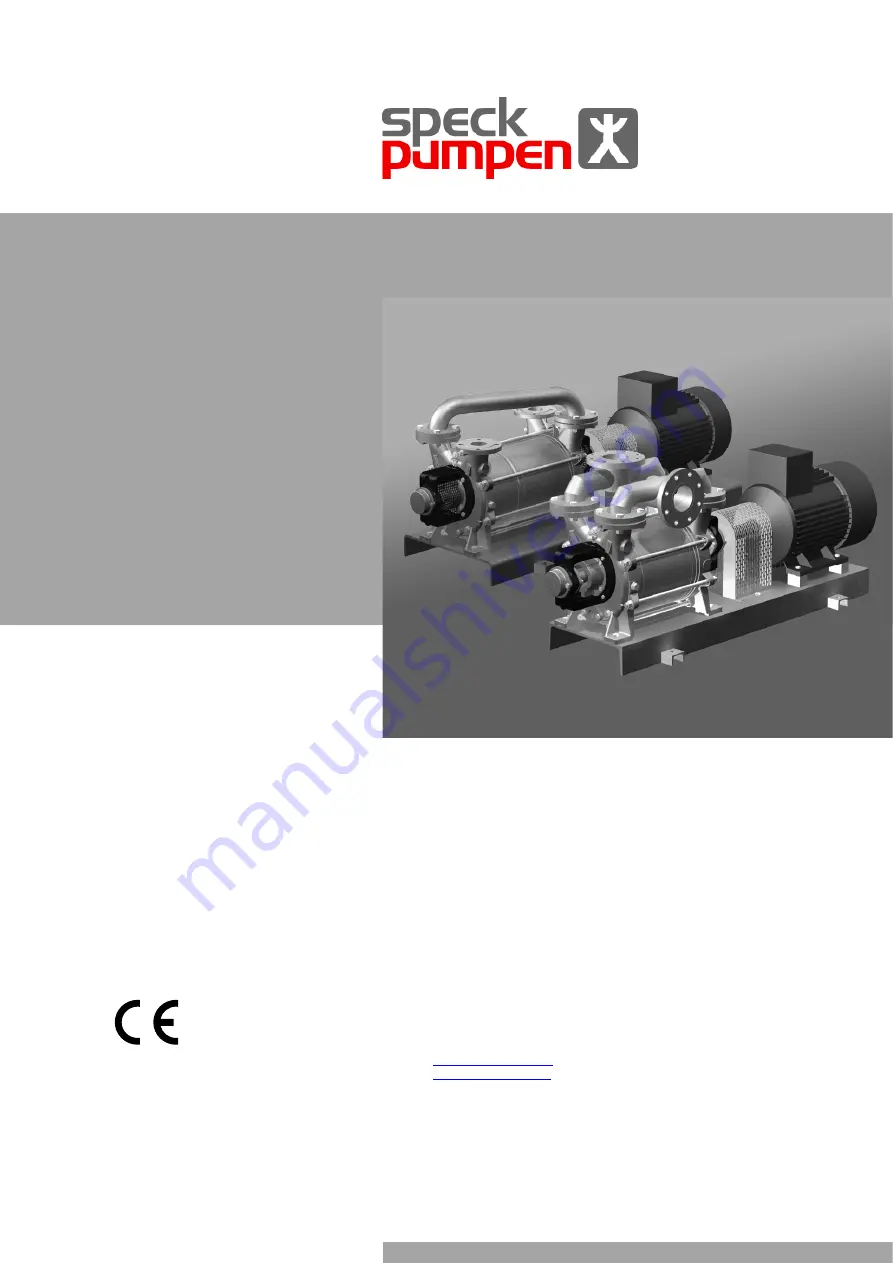
Operating Instructions
VU / VH Series
VU 20 - 1600
VH 20 - 1600
Liquid Ring Vacuum Pumps
English translation of the original operating
instructions
Documentation
It is imperative to read the operating instruc-
tions prior to commissioning!
This document as well as all documents in-
cluded in the appendix is not subject to any
update service!
Subject to technical changes.
Speck Pumpen Vakuumtechnik GmbH
Regensburger Ring 6 – 8, 91154 Roth / Germany
PO Box 1453, 91142 Roth / Germany
Phone: +49 (0) 9171 809 0
Fax:
+49 (0) 9171 809 10
E-mail:
Internet:
www.speck-pumps.de
Issue:
10/2010
Supersedes issue:
06/2010
Doc./ Item no.:
1096.0799