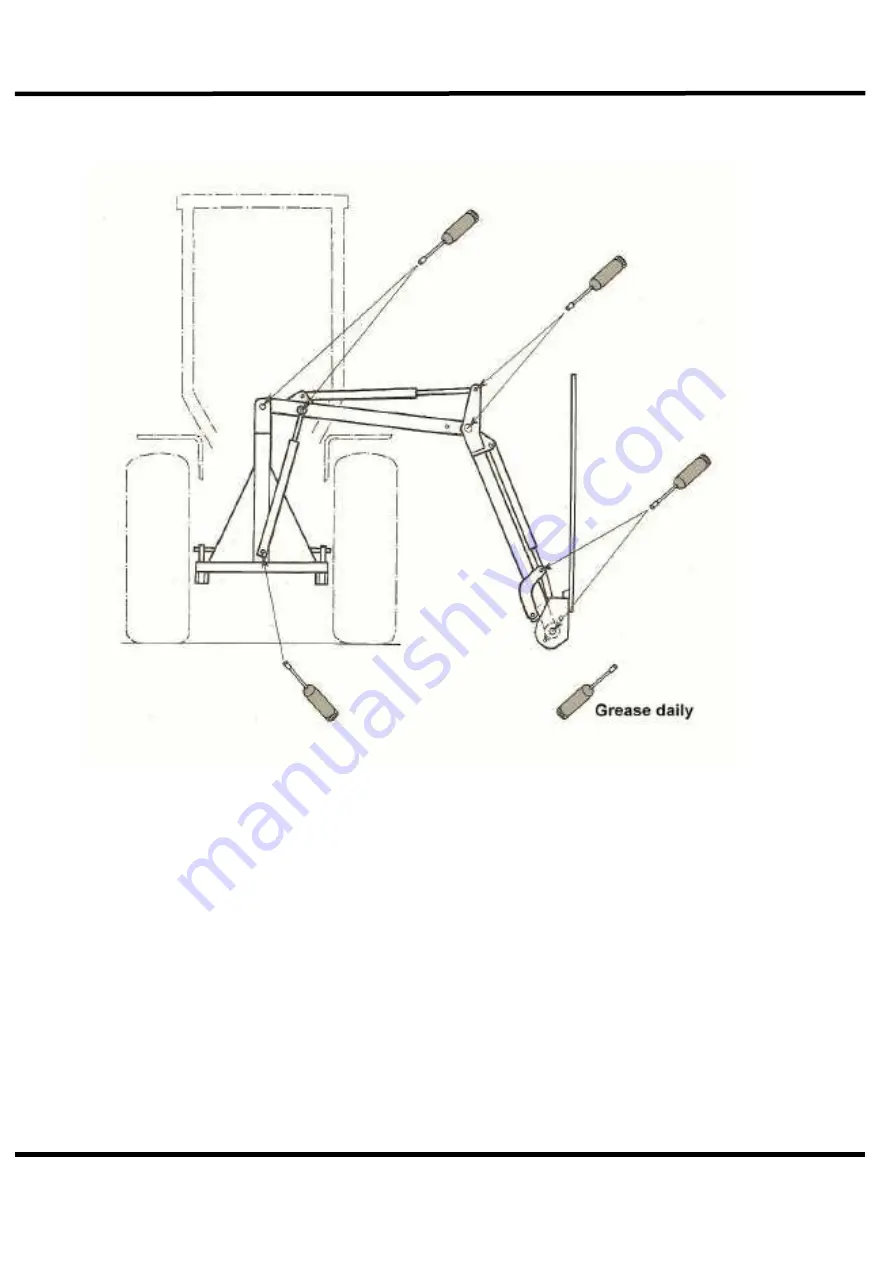
Spearhead TWIGA
120
20
20
20
20
M
M
M
MAINTENANCE
AINTENANCE
AINTENANCE
AINTENANCE
Lubrication
Refer to the lubrication diagram above and grease daily all points indicated. Remember
regular lubrication ensures longer machine life and diminishes service costs. In addition,
occasionally oil the con-rod pivots and bushes.
Fasteners
Check on a daily basis that all bolts and nuts are tight, pins are secure and hydraulic
corrections are not leaking. Regularly inspect the hydraulic hoses and always replace
them immediately at the first signs of wear or damage.
Summary of Contents for TWIGA 120
Page 33: ...Spearhead TWIGA 120 32 32 32 32...