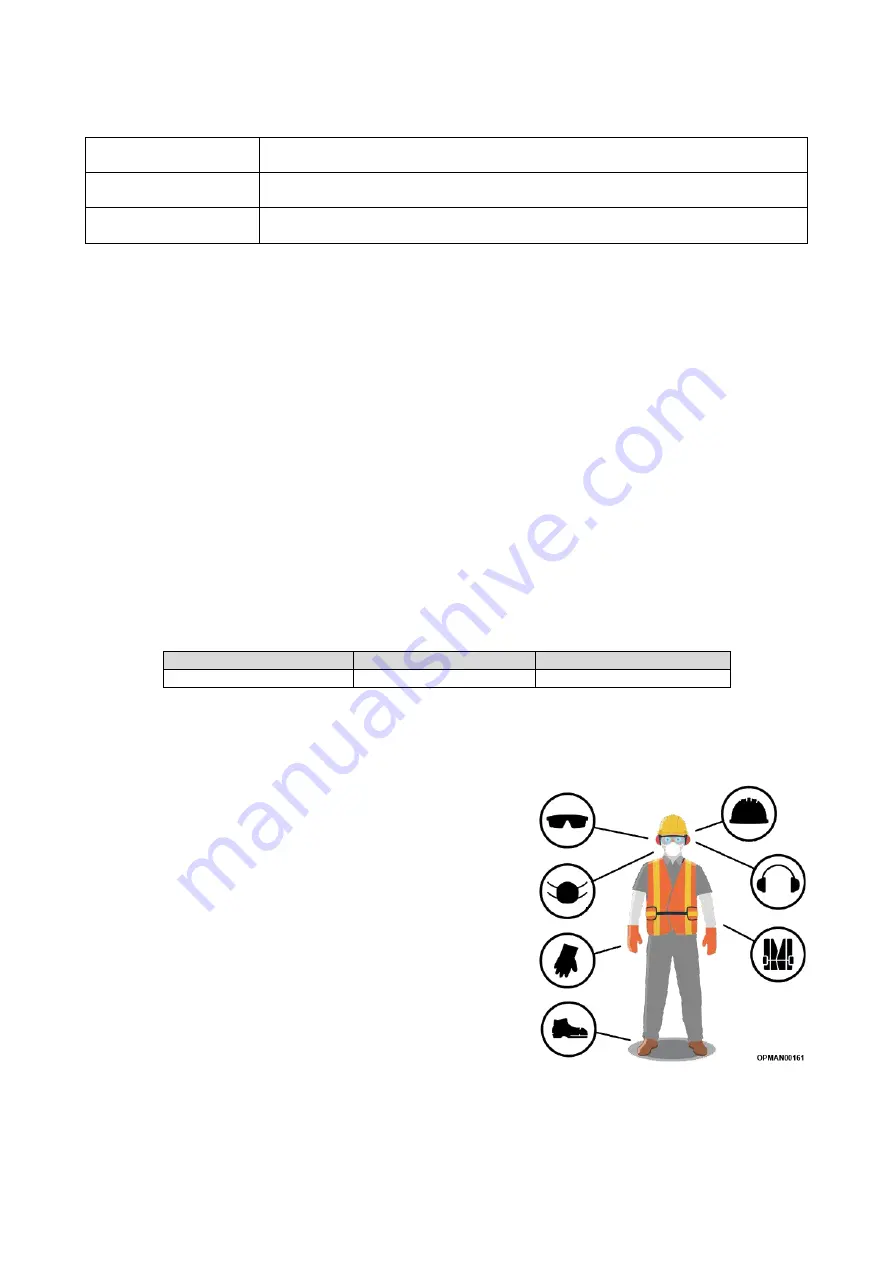
8999151EN: v1 11/03/2021
31
Original instructions (ENGLISH)
Website: www.spearheadmachinery.com
Always replace guards that have damage or wear which could impair their performance. Typical damage to
inspect for is as follows;
Drive guard and side
skids
Distorted or with sharp outer edges, exposed openings
PTO guards
Cracked, missing portions revealing moving parts
Chain guards
Missing chain lengths to permit stones or similar objects to be ejected beneath it in
normal conditions
Table 2.3
– Permanent Protection Guard Damages
2.6.1
Mandatory Guards
The General arrangement figure found in Section 1.2 and the list below show the mandatory guards required.
These along with the danger decals and warning decals are necessary for safe cutting operations with this
machine;
•
Driveline guard
•
PTO shaft guard
•
Front metal chain guards
•
Rear metal chain guards
2.7
Sound
The air noise level created by the machine under operating conditions was detected using a sound level meter
with integrator.
The measurements were carried out in accordance with ISO 1680-2 with the machine.
Tests performed under the conditions indicated by the standard produced the following results:
Machine
Tractor With Open Cab
Tractor With Closed Cab
Multicut 300
94 dB
80 dB
Table 2.4
– Multicut Sound Readings
2.8
Personal Protective Equipment
Operators should be wearing sufficient personal protection
equipment (PPE) to protect them from hearing, respiratory and
impact damages.
When working in an unsealed cab or where windows and apertures
are open to the environment, operators are advised to wear suitable
eye and ear protection, a facemask (depending on conditions) and
eye protection.
When handling cutting surfaces or hydraulic equipment, operators
are advised to wear suitable gloves.
When clearing blockages, clearing wire, or working with pressurised
hydraulic components, operators are advised to wear suitable eye
protection and suitable gloves.
Ensure that non-baggy clothing is worn to reduce the chance of
entanglement and snagging on components.
Figure 2.4- PPE Items
When working at the work site, but off the tractor unit, operators are advised to wear a ‘high-viz’ garment.