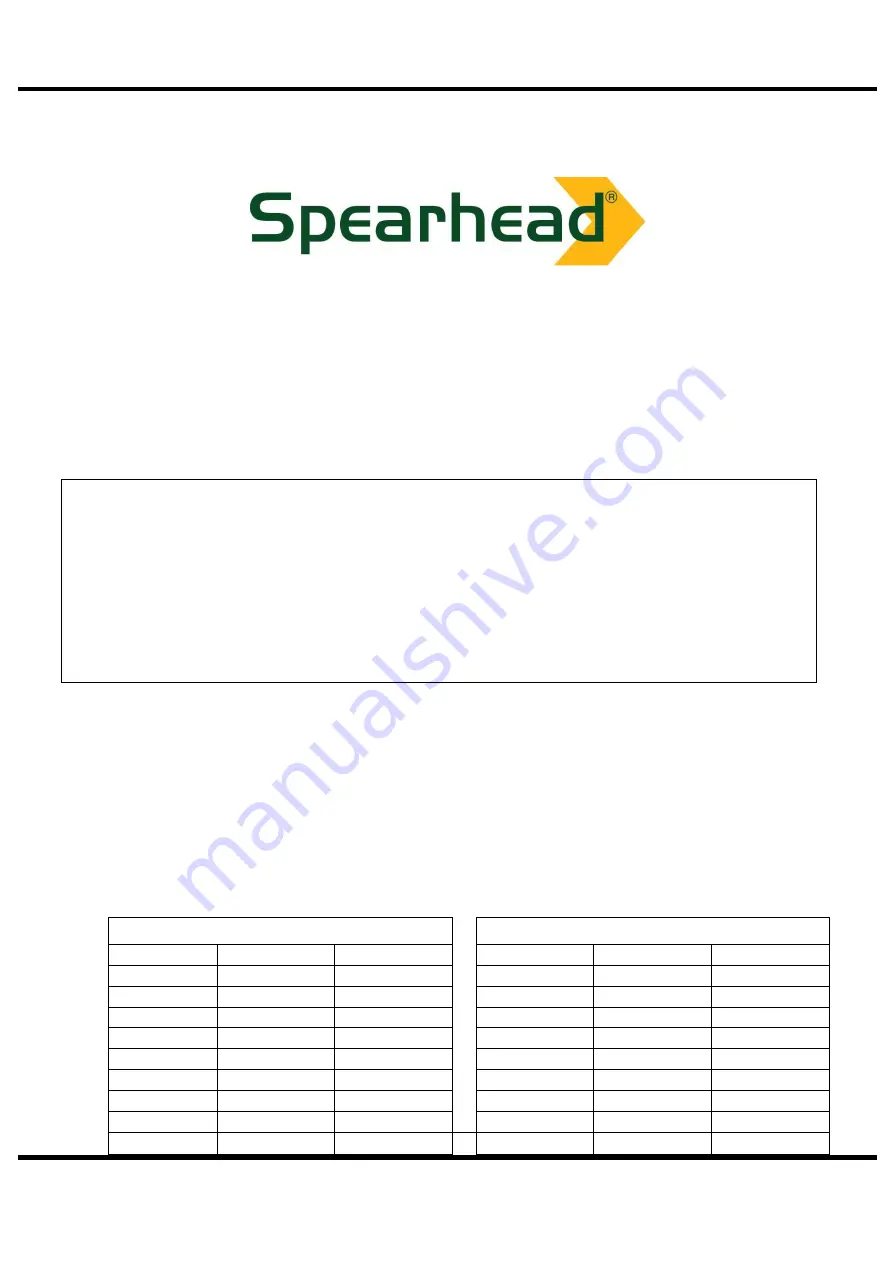
2
2
2
2
Trident 7600HD
IMPORTANT
VERIFICATION OF WARRANTY REGISTRATION
DEALER WARRANTY INFORMATION & REGISTRATION VERIFICATION
It is imperative that the selling dealer registers this machine with Spearhead Machinery Limited before delivery to
the end user – failure to do so may affect the validity of the machine warranty.
To register machines go to the Spearhead Machinery Limited web site at www.spearheadmachinery.com,
log onto ‘Dealer Inside’ and select the ‘Machine Registration button’ which can be found in the Service
Section of the site. Confirm to the customer that the machine has been registered in the section below.
Should you experience any problems registering a machine in this manner please contact the Spearhead
Service Department on 01789 491867.
Registration Verification
Dealer Name:
……………………..…………………………………………………………….
Dealer Address:
…….………………………………………………………………………….
Customer Name:
……………………..…………………………………………………………
Date of Warranty Registration:
……/……/...…… Dealer Signature: ………………..……
NOTE TO CUSTOMER / OWNER
Please ensure that the above section has been completed and signed by the selling dealer to verify that
your machine has been registered with Spearhead Machinery Limited.
IMPORTANT: During the initial ‘bedding in’ period of a new machine it is the customer’s responsibility to
regularly inspect all nuts, bolts and hose connections for tightness and re-tighten if required. New
hydraulic connections occasionally weep small amounts of oil as the seals and joints settle in – where
this occurs it can be cured by re-tightening the connection – refer to torque settings chart below. The
tasks stated above should be performed on an hourly basis during the first day of work and at least daily
thereafter as part of the machines general maintenance procedure.
CAUTION: DO NOT OVER TORQUE HYDRAULIC FITTINGS AND HOSES
TORQUE SETTINGS FOR HYDRAULIC FITTINGS
HYDRAULIC HOSE ENDS
PORT ADAPTORS WITH BONDED SEALS
BSP
Setting
Metric
BSP
Setting
Metric
1/4”
18 Nm
19 mm
1/4”
34 Nm
19 mm
3/8”
31 Nm
22 mm
3/8”
47 Nm
22 mm
1/2”
49 Nm
27 mm
1/2”
102 Nm
27 mm
5/8”
60 Nm
30 mm
5/8”
122 Nm
30 mm
3/4”
80 Nm
32 mm
3/4”
149 Nm
32 mm
1”
125 Nm
41 mm
1”
203 Nm
41 mm
1.1/4”
190 Nm
50 mm
1.1/4”
305 Nm
50 mm
1.1/2”
250 Nm
55 mm
1.1/2”
305 Nm
55 mm
2”
420 Nm
70 mm
2”
400 Nm
70 mm
Summary of Contents for 8999082
Page 20: ...20 20 20 20 Trident 7600HD ...