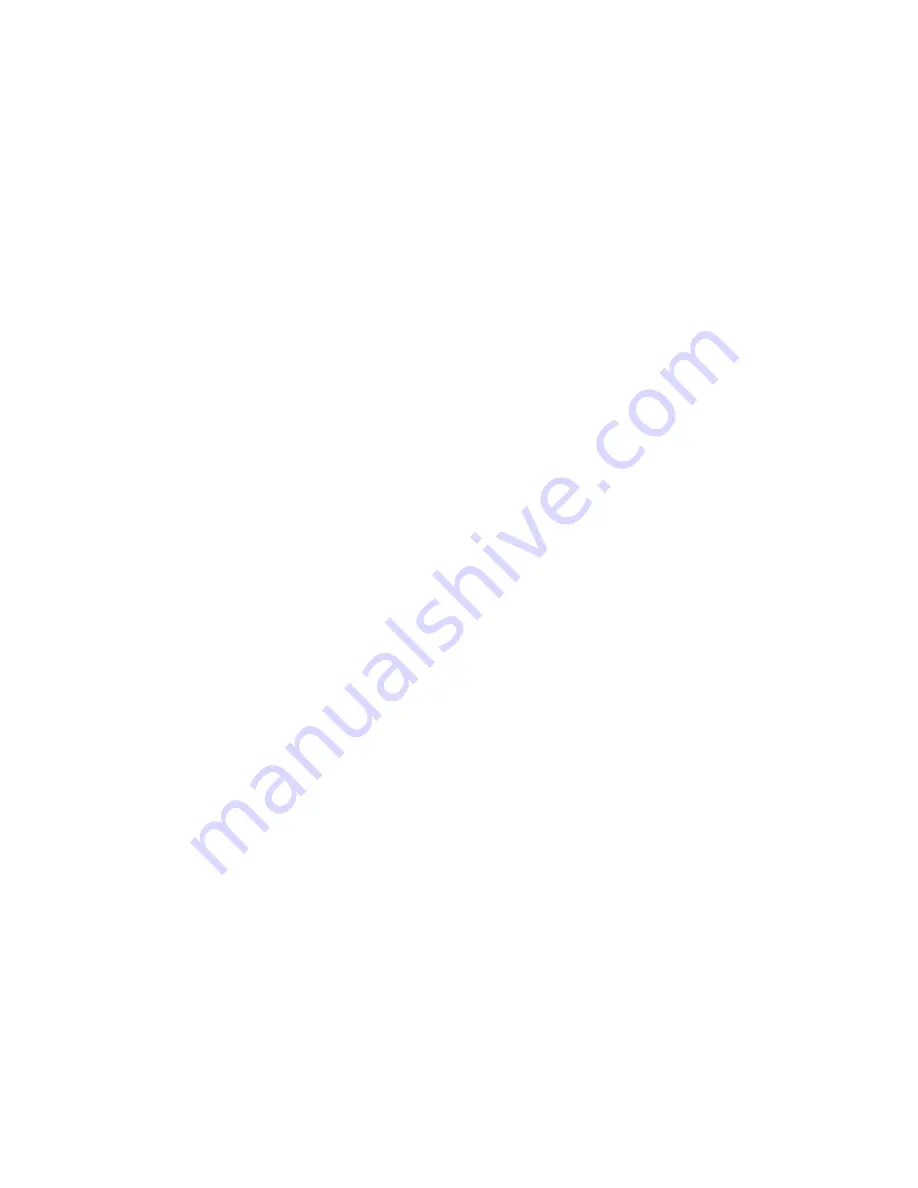
INDEX
Page No
1
Starting Work
2
General Operation
Dust Control
3-4
Maintenance
5
Basic Maintenance Checklist
6
Safety
7-8
Accessories
9-11
Cutter Drum Set Up
12
Spare Parts Breakdown
13
Body Components
14
Undercarriage Components
15
Height Adjuster Components
16
Drum Drive Components
17
Hydraulic Tank Components
18
Hydraulic Drive Components
19
Height Control Components
20
Motor Drive Components
21
Hydraulic Flow and Main Components
22
Yanmar Engine Components
23
Specifications
24
Noise/Vibration Assessment
25
Warranty
26
Declaration of Conformity
27
Conditions of Sale
Summary of Contents for BEF320-3A
Page 12: ...12 ...